Stick electrode welding, also known as shielded metal arc welding (SMAW), is a widely used process in the fabrication and construction industries. This time-tested welding method is renowned for its versatility, simplicity, and effectiveness, making it an invaluable tool for professionals across various fields. In this article, we delve into the world of stick electrode welding with insights born from years of practical experience and expert knowledge, ensuring a comprehensive understanding of this essential technique.
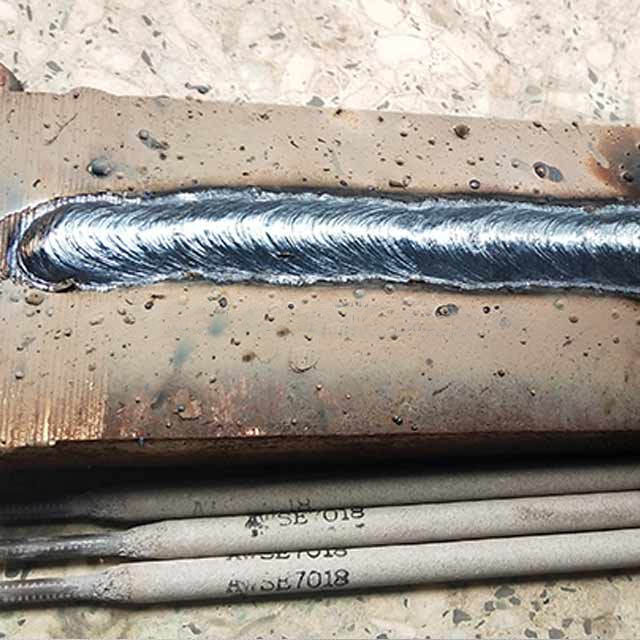
Understanding the Fundamentals of Stick Electrode Welding
At its core, stick electrode welding involves the use of a consumable electrode coated in flux to create an electric arc between the electrode and the workpiece. This process results in the melting of both the electrode and the workpiece, forming a weld pool that solidifies into a strong joint upon cooling. The flux coating serves multiple purposes it stabilizes the arc, shields the molten metal from atmospheric contamination, and adds alloying elements that enhance the properties of the joint.
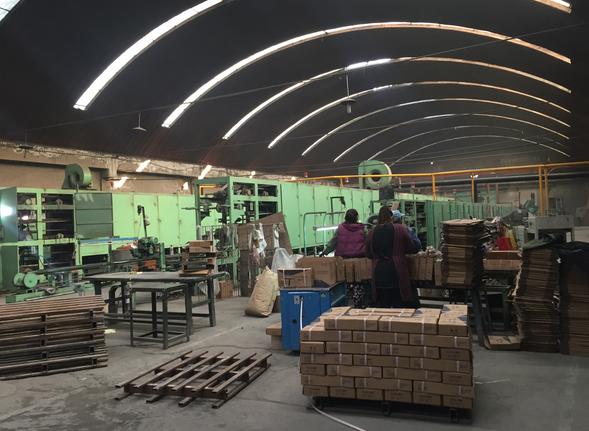
Stick electrode welding is revered for its ability to work with a variety of metals, including steel, stainless steel, and cast iron. Moreover, it is effective in various positions—flat, vertical, horizontal, and overhead—making it an adaptable solution for complex welding scenarios.
Professional Insights into Electrode Selection
A critical aspect of successful stick electrode welding is the selection of the appropriate electrode. Experienced welders understand that choosing the right electrode depends on factors such as the type of metal, the welding position, and the desired mechanical properties of the finished weld. Common electrodes like E6010, E6011, E6013, and E7018 each offer unique attributes suited to specific applications. For instance, E6011 electrodes are favored for their deep penetration capabilities, making them ideal for welding in challenging conditions such as rusty or dirty surfaces.
The selection process also extends to considering the diameter of the electrode, which plays a vital role in determining the strength and appearance of the weld. Thinner electrodes provide greater control and are preferred for thin materials, while thicker electrodes facilitate higher deposition rates for larger structures.
Mastering Technique Through Expert Practice
stick electrode welding
Perfecting the technique of stick electrode welding involves honing skills in electrode manipulation, arc length control, and travel speed. Seasoned welders emphasize the importance of maintaining a consistent arc length, typically equal to the diameter of the electrode, to ensure a stable arc and optimal weld bead.
Furthermore, electrode manipulation—such as weaving or stringer techniques—affects the bead shape and penetration. Weaving is particularly effective in filling wide gaps or creating wider beads, while stringer techniques are preferred for root passes or thin materials.
One key insight is the management of heat input; excessive heat can lead to distortion and weaken the weld, while insufficient heat may result in poor fusion. Knowledgeable practitioners skillfully balance heat input to produce strong and aesthetically pleasing welds.
Building Authority Through Quality Control and Safety
Trustworthiness in stick electrode welding stems from adhering to stringent quality control measures and safety protocols. Experienced professionals are meticulous in their inspection of welds, employing non-destructive tests like ultrasonic or radiographic testing to detect internal defects. By ensuring the integrity of each weld, they uphold industry standards and customer expectations.
Additionally, maintaining a safe working environment is paramount. Experts stress the importance of proper protective gear, such as welding helmets, gloves, and flame-resistant clothing, to mitigate the risks associated with arc radiation and spatter. Adequate ventilation is equally essential to prevent the inhalation of harmful fumes generated during welding.
Conclusion
Stick electrode welding remains an indispensable technique for metallurgical fabrication and repair, backed by decades of proven success. Armed with a thorough understanding of electrode selection, mastering technique, and commitment to quality and safety, welders not only enhance their expertise but also affirm their role as authoritative figures in the welding community. As industries evolve and new challenges present themselves, the enduring relevance of stick electrode welding continues to shine, affirming its place as a trusted ally in the world of metalworking.