Choosing the right cast iron welding rod can significantly influence the outcome of your welding projects, especially when dealing with complex materials like cast iron. This article delves into the expertise and insights needed for selecting and using cast iron welding rods effectively, ensuring your projects not only meet structural requirements but also stand the test of time.
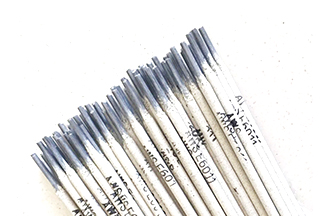
Cast iron, known for its durability and resistance to wear, presents unique challenges when welding. Its composition of iron, carbon, and silicon creates a structure that can be brittle, making it susceptible to cracking during the welding process.
This calls for a specialized approach that begins with selecting an appropriate welding rod.
The first consideration is understanding the types of cast iron you are working with. Gray irons, white irons, and ductile irons each have distinct properties. Welding rods like the nickel-based electrodes are often recommended for gray iron due to their compatibility in thermal expansion, thereby minimizing the chances of cracking. For castings that require machining after welding, consider using a nickel-iron based rod, which provides superior machinability.
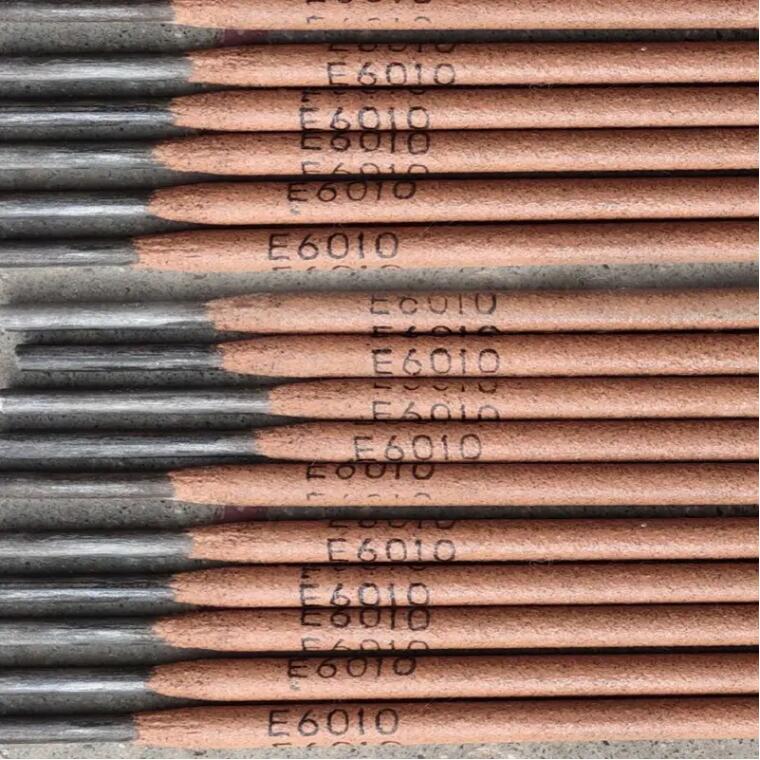
Expertise in handling cast iron also emphasizes the importance of pre-weld and post-weld practices. Preheating the cast iron to a temperature between 500°F to 1200°F is crucial as it reduces thermal shock and the risk of stress-induced cracking. This preventive measure aligns with the authoritative recommendation of welding engineers who stress temperature control as a critical factor. Similarly, allowing the cast iron to cool slowly post-welding by using insulating blankets helps in reducing residual stresses.
Trustworthiness in a product is as important as skill. Therefore, ensure that the welding rods you choose come from reputable manufacturers who comply with industry standards. Reliable brands often provide technical datasheets detailing composition, tensile strength, and recommended procedures, which are valuable resources for professionals requiring precise specifications and assurances.
cast iron welding rod
One cannot overlook the role of technique and skill enhancement in enhancing weld integrity. In terms of practical experience, it is advisable to perform practice welds on sample materials to perfect your technique. This step specifically facilitates a hands-on understanding of how the rod behaves under actual conditions, allowing you to adjust variables like amperage settings and travel speed for optimal results.
Furthermore, every welder understands the importance of safety and efficiency. Utilize personal protective equipment (PPE) rigorously, including gloves, face shields, and welding jackets, which are integral to safeguarding against the high temperatures and UV radiation inherent in welding. Efficient workspace setup, well-ventilated areas, and good lighting are non-negotiable aspects that contribute significantly to high-quality weld outcomes.
Finally, feedback loops are crucial. Engaging with a community of welders or participating in forums dedicated to cast iron welding can provide anecdotal experiences and insights into the latest techniques and products. This continuous learning loop is invaluable for maintaining relevance and authority in the ever-evolving field of welding.
In summary, achieving a successful weld with cast iron requires a nuanced understanding of material properties, a keen selection of welding rods, adherence to best practices, and relentless pursuit of safety and knowledge. By integrating these elements, one can ensure durable, effective, and professionally-acclaimed welding results.