Flux cored welding wire has revolutionized the realm of welding, offering versatility and efficiency that few other methods can match. These wires are self-shielded or gas-shielded, specially engineered to cater to a wide range of metals such as carbon steel, stainless steel, and even nickel alloys. The genius of flux cored welding lies in its design; it is essentially a continuous hollow electrode filled with flux to protect the weld pool during the process.
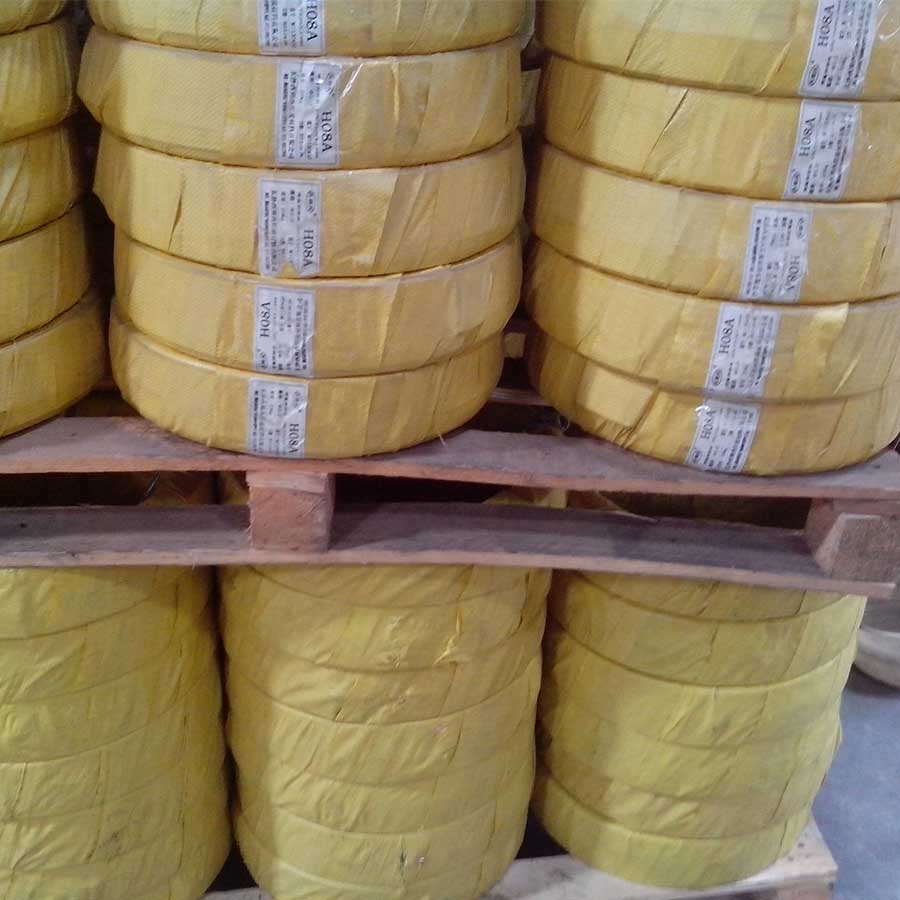
My professional journey in the welding industry has provided ample opportunities to directly observe flux cored welding wire in action. The expertise gained through years of meticulous work has solidified my understanding of its advantages and the specifics surrounding its application. Notably, the wire's performance in windy outdoor conditions is exemplary, a feature attributed to the shielded arc process. This makes it indispensable for construction projects subjected to variable weather conditions.
In my experience, the compatibility of flux cored welding wire with different metals provides versatility across diverse projects. It ensures deep penetration and high deposition rates, which significantly enhance the productivity of each task. For welding professionals, the adaptability of the wire to different types of weld joints and positions underscores its unmatched flexibility.
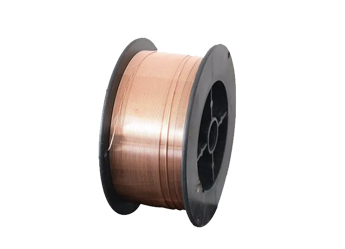
From the standpoint of expert knowledge, one critical factor for optimal results with flux cored welding wire is the meticulous selection process.
This involves choosing the correct wire type and diameter tailored to the specific welding requirements. Self-shielded wire, for instance, eliminates the need for external shielding gas, perfect for remote site operations without access to gas resources. On the other hand, gas-shielded wire is ideal in applications requiring cleaner welds with minimal spatter.
flux cored welding wire
Authoritativeness comes from establishing that flux cored welding wire offers a solution validated by numerous successful industry applications. It enjoys widespread adoption in sectors like shipbuilding, construction, and heavy equipment manufacturing due to its efficacy in handling thick sections of metal. Additionally, it is crucial to rely on reputable manufacturers with certifications that meet industry standards such as AWS (American Welding Society) and ISO, ensuring that every spool provides consistent performance.
Trustworthiness, in this context, springs from reliability. Welders have shared accounts of flux cored welding wire’s consistency, noting its stable arc and minimal cleanup requirement due to reduced slag. Understanding the intricacies of wire feed speed, voltage setting, and power source compatibility has enabled professionals to rely on these wires fully, ensuring that each weld meets rigorous quality checks and safety standards.
In sum, flux cored welding wire presents a blend of experience, expertise, and reliable performance. Its capacity to adapt to varying project demands whilst maintaining quality makes it a prominent choice for welding professionals seeking assurance in their tools. The continued advancements in flux cored technology promise an exciting evolution, further enhancing its position as a crucial component in modern welding applications.