Solid welding wire, integral to numerous manufacturing and construction processes, significantly affects the quality and strength of welds. With years of hands-on welding experience, I have come across various versions and brands, allowing me to delve deeply into the specifics that optimize its usability and performance.
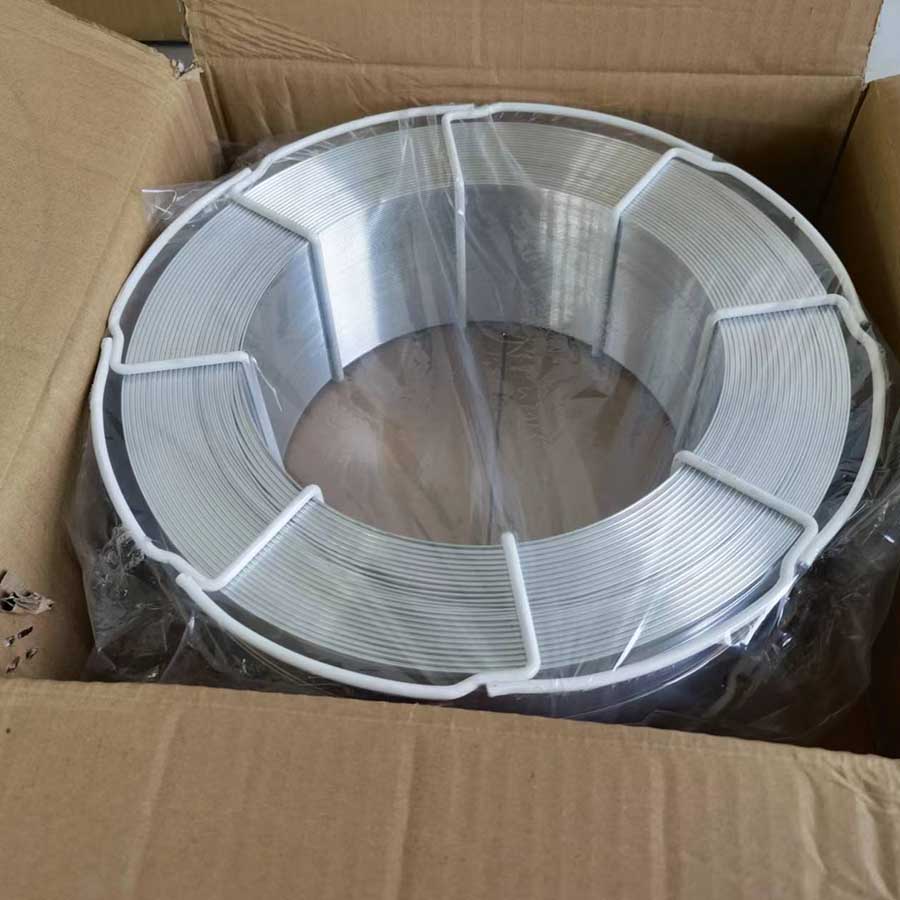
Understanding solid welding wire begins with recognizing its composition and the scenarios it best suits. Typically made from steel, including mild steel or stainless steel, these wires are devoid of flux and are ideal for MIG (Metal Inert Gas) welding. In industries ranging from automotive to structural engineering, solid welding wire excels where a clean, precise weld is essential. Its application ensures minimal spatter and excellent control over the weld pool, making it indispensable for projects demanding high aesthetic standards.
Having worked alongside seasoned welders and in diverse project settings, one consistent factor that influences the weld's outcome is the wire's diameter. Generally, the smaller diameter solid wires are preferable for thinner materials, providing finesse and reducing the risk of burn-through. In contrast, larger diameter wires are suited for thicker materials, offering deeper penetration and greater strength in the weld joint. Selecting the right diameter wire is an expertise-driven decision, one that could make or break the project at hand.
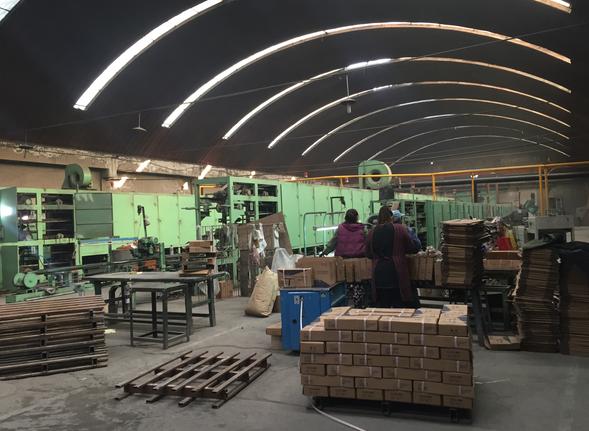
Another essential aspect of solid welding wire lies in its coating. Copper-coated wires, for example, are renowned for their enhanced conductivity and corrosion resistance. In my expert opinion, these attributes extend the lifespan of welding components like contact tips and liners, ultimately leading to cost-efficiency in projects. On the other hand, non-copper-coated wires may serve better in specific environmental conditions where copper-related fumes could pose a health risk to operators.
solid welding wire
Given the myriad options on the market, trustworthiness involves opting for reputable manufacturers who adhere to international quality standards. These brands often offer consistent wire feeding and predictable melting rates which are essential for maintaining the integrity of the weld under varied working conditions. In my experience, when you trust a brand known for its quality assurance, the reliability and performance in critical applications stand unquestioned.
Alongside selecting the highest quality solid welding wire, it is equally important to consider the equipment used alongside it. In my professional practice, pairing the wire with the right power settings and inert shielding gases, such as argon or CO2, plays a crucial role in achieving optimal weld quality. The expertise lies in fine-tuning these elements to reduce oxidation and improve the weld's mechanical properties.
Reflecting on years of welding applications, the authoritativeness on solid welding wire also stems from ongoing education and adapting to technological advancements. Welding seminars, practical training, and manufacturer workshops continually update practitioners on innovative wire compositions and improved techniques. Staying informed ensures that one harnesses the full potential of the solid welding wire available today.
In conclusion, selecting and using solid welding wire is not just a basic component decision; it involves a blend of experience, expertise, authority, and trustworthiness. Understanding the nuances of its application can drastically enhance the performance and longevity of the welds, ensuring that every project is executed to the highest standards, maintaining both the structural integrity and aesthetic excellence that clients deserve.