The art of welding is as timeless as the metalwork it produces, and among the most popular methods are TIG, MIG, and Stick welding. Each of these techniques caters to specific needs and circumstances, offering unique benefits that make them suitable for different projects. With over two decades of experience in the welding industry, I've uncovered the nuanced advantages and challenges presented by these methods, which should guide you in selecting the right technique for your next venture.
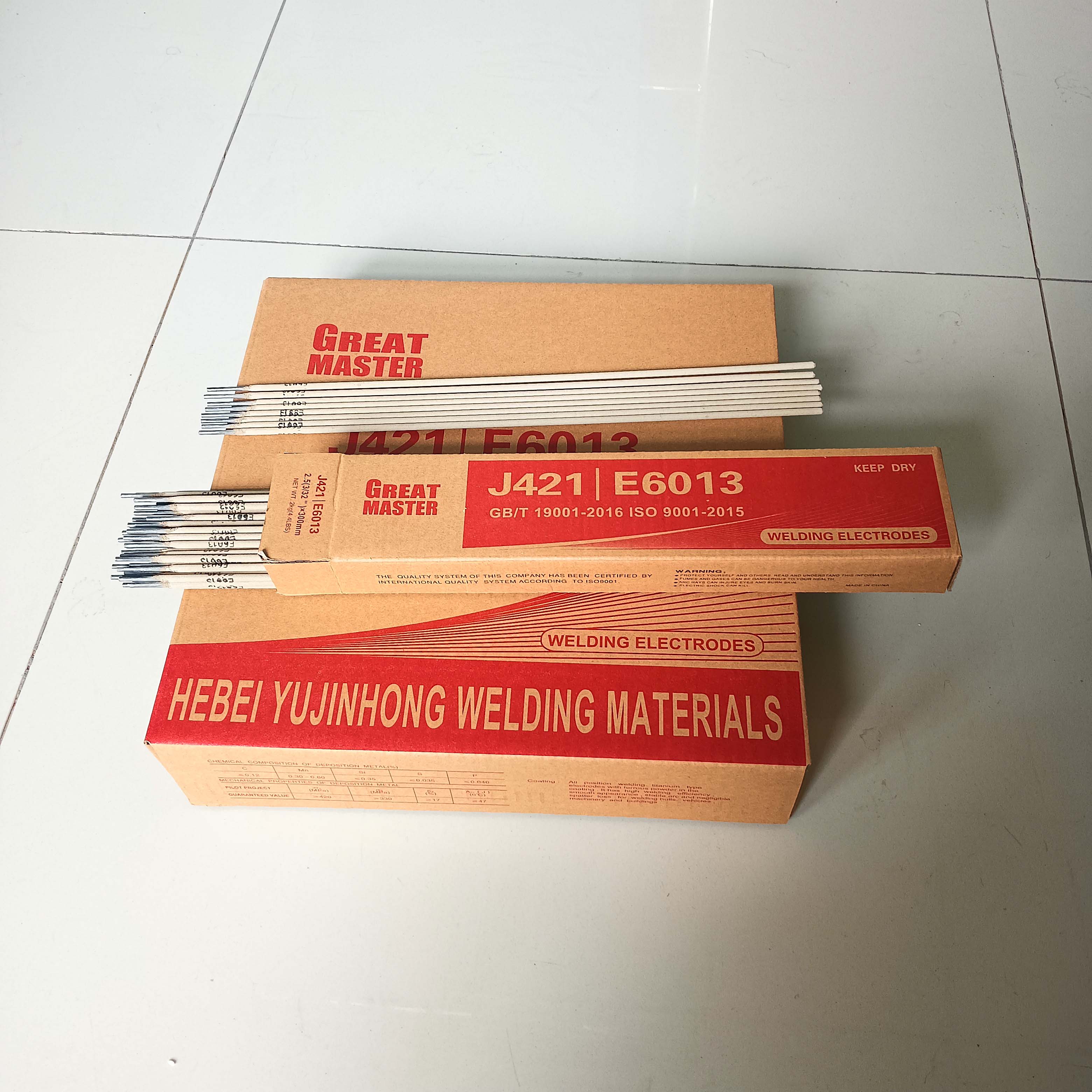
TIG welding, or Tungsten Inert Gas welding, is renowned for its precision and control. It's the technique of choice when working with delicate materials and requiring a high degree of accuracy, such as in aerospace applications or custom car builds. The precision offered by this method stems from its use of a non-consumable tungsten electrode. Unlike other methods, TIG welding allows for separate control of the heat and the filler material, providing the welder with unparalleled finesse. However, it requires a high level of skill and patience due to its slower process, which can be a disadvantage for larger projects with tight deadlines.
In contrast, MIG welding or Metal Inert Gas welding stands out for its speed and ease of use. It's particularly popular in automotive repair and construction industries where time and efficiency are of the essence. MIG welding involves feeding a continuous wire electrode through the welding gun, creating a faster and more straightforward process than TIG welding. It is ideal for beginners or hobbyists due to its forgiving nature and is capable of welding thick materials quickly. Yet, it might not offer the same level of precision and cleanliness as TIG welding, which can result in more post-weld work in terms of cleaning and finishing.
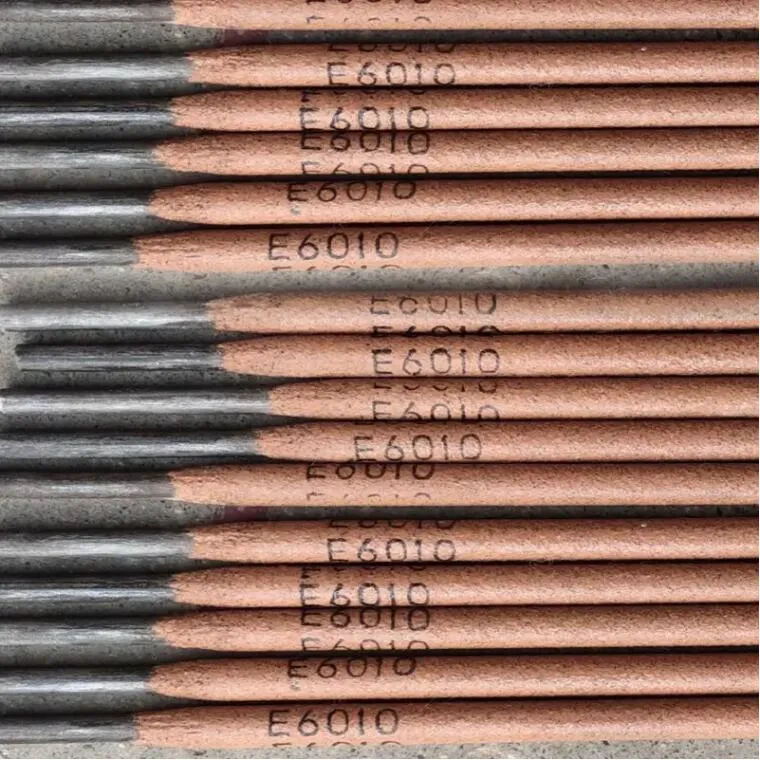
Stick welding, or Shielded Metal Arc Welding (SMAW), boasts robust versatility and straightforwardness. It is well-suited for outdoor environments and industrial construction where conditions are less than ideal—a pivotal advantage when working against the elements. This method uses an electrode coated in flux to protect the weld from contamination, allowing it to perform well even on dirty or rusty materials. The simplicity of the equipment needed for stick welding makes it a cost-effective choice for beginners and professionals alike. However, the technique does produce more slag and requires a greater level of cleanup compared to MIG and TIG processes.
tig mig and stick welding
Choosing between TIG, MIG, and Stick welding demands a careful evaluation of your project's requirements. Consider the type of material, the desired finish, the environment you'll be working in, and your own level of expertise.
For projects demanding precision and aesthetic quality, TIG welding stands unrivaled. MIG welding is preferable for projects where speed and efficiency are prioritized, and for jobs in rugged environments or on less-than-perfect surfaces, Stick welding prevails with its reliability and durability.
Making informed decisions about welding techniques not only impacts the quality of your project but also enhances the efficiency and safety of your operations. Continuous learning and adaptation to new advancements in welding technology will further sharpen your skills and expand your capabilities. Trust in seasoned insights, a thorough understanding of each method's advantages and limitations, and practical experience as your blueprint for success in the vibrant and evolving world of welding.
Invest in quality equipment, strive for excellence in craftsmanship, and remain cognizant of safety measures to uphold the industry's highest standards. As a welder, your expertise becomes a testament to the fusion of metal and innovation, creating structures that are both resilient and aesthetically pleasing.