When it comes to welding techniques, the choice between TIG, MIG, and Stick welding often hinges on the specific requirements of your project, including material type, thickness, and finishing needs. These three welding styles each offer unique advantages and disadvantages, and understanding their differences is crucial for anyone looking to make informed decisions in fields ranging from automotive repair to heavy machinery fabrication.
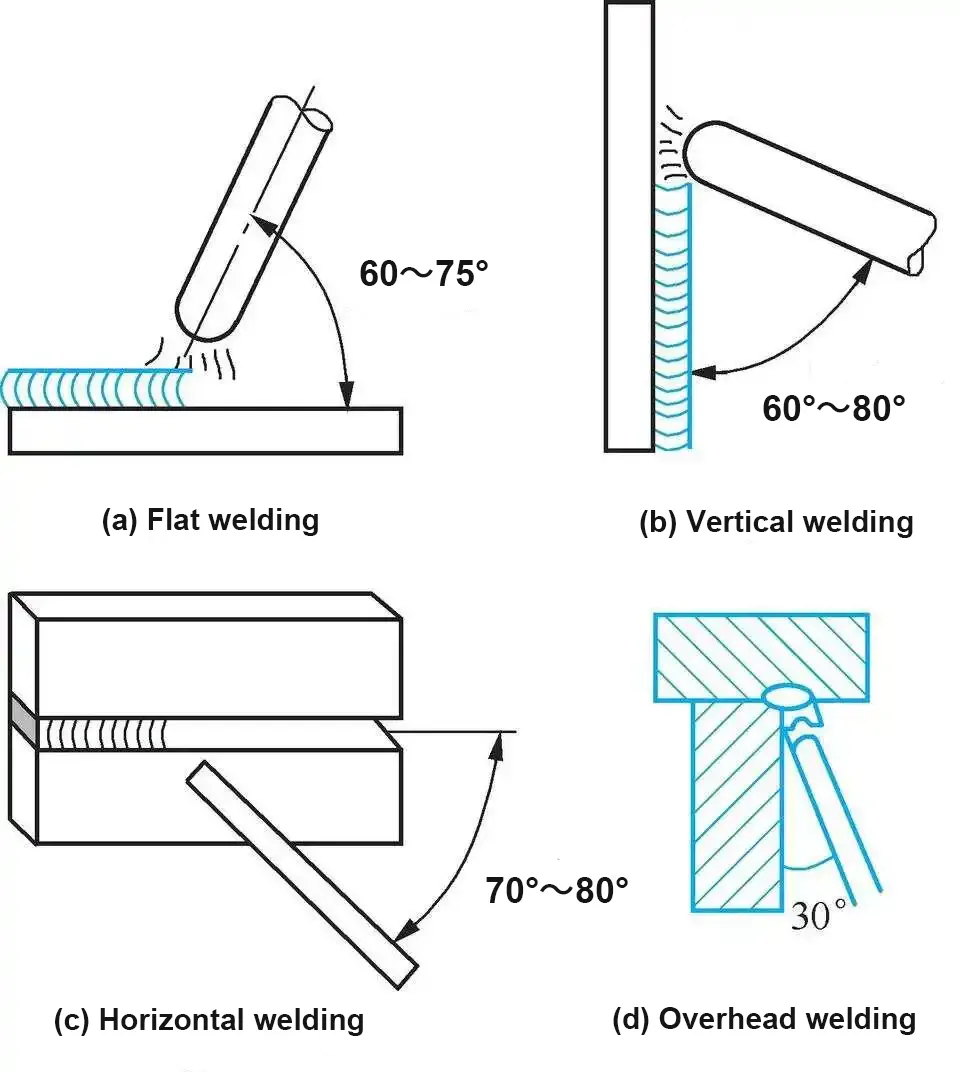
TIG welding, or Tungsten Inert Gas welding, is renowned for its precision and clean welds. This method is ideal for thin materials such as aluminum and stainless steel, providing welds that are highly aesthetic and free of spatter. The process involves using a non-consumable tungsten electrode which delivers current to the welding arc. One of the standout features of TIG welding is its ability to control heat input via a foot pedal or hand control, allowing for intricate applications that require high precision. Professionals in the aerospace and motorsport industries often favor TIG welding because of its ability to create neat, high-quality welds necessary for critical components.
On the other hand, MIG welding, or Metal Inert Gas welding, is known for its simplicity and efficiency, making it a popular choice for both hobbyists and industrial welding applications. This process uses a consumable wire electrode fed through the welding gun, allowing for continuous welding. MIG welding is typically faster and more forgiving than TIG welding, handling thicker materials like mild steel with ease. It's an excellent choice for projects where speed is a priority without sacrificing weld strength. Many manufacturing sites employ MIG welding due to its flexibility and ease of use, particularly in producing automotive parts and large structures.
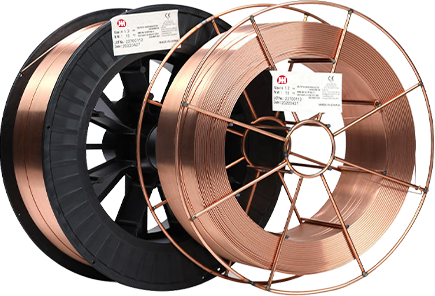
Stick welding, also known as Shielded Metal Arc Welding (SMAW), is one of the oldest and most versatile welding techniques. It excels in outdoor environments and on rusty or dirty metals where other methods might falter. Stick welding uses a consumable stick electrode coated with flux, which helps protect the weld from atmospheric contamination. While not as clean as TIG or as fast as MIG, stick welding is revered for its ability to perform in adverse conditions, making it the go-to method for construction and fieldwork. Its equipment is also generally more affordable and portable compared to TIG and MIG setups.
Selecting the right welding method depends largely on the specific context of the task at hand. For instance, if dealing with intricate metal art or thin-walled tubing, TIG welding delivers the precision needed. MIG welding should be the choice for large-scale production work where speed and efficiency are critical. Stick welding remains unmatched when tackling tasks in environments where other techniques may not sustain acceptable performance levels, such as in windy outdoor conditions.
tig mig stick welding
Another crucial facet is understanding the equipment demands associated with each process. TIG welding often requires the most investment in terms of equipment sophistication and operator skill but returns are seen in the superior finish quality. MIG welding sees a balance between cost and ease of use, with moderate equipment setup that often includes a gas tank setup for inert gas coverage. Stick welding, while somewhat rougher in finish, compensates with equipment that’s rugged and tailored for ease of transport and use in remote locations.
The materials themselves impose additional considerations. TIG handles non-ferrous metals like aluminum well, which is not often the case with Stick welding. Conversely,
thick materials form a domain where Stick and MIG welding shine.
All three welding techniques demand a thorough understanding and respect for safety protocols. Proper personal protective equipment (PPE) such as helmets, gloves, and aprons must be utilized to safeguard against the high heat and potential UV exposure inherent to these processes.
Mastery of TIG, MIG, and Stick welding empowers fabricators to tackle a diverse array of projects efficiently and safely while ensuring the integrity and aesthetic of the final product are never compromised. Each method brings specific strengths to the table, and when applied with expertise and precision, can achieve incomparable results that resonate in durability and visual appeal.