Welding electrodes play a crucial role in the world of fabrication and metalworking, serving as essential components in the welding process. These electrodes are specialized tools that facilitate the joining of metal parts, ensuring strong, durable bonds that are critical in various industries such as construction, automotive, shipbuilding, and aerospace.
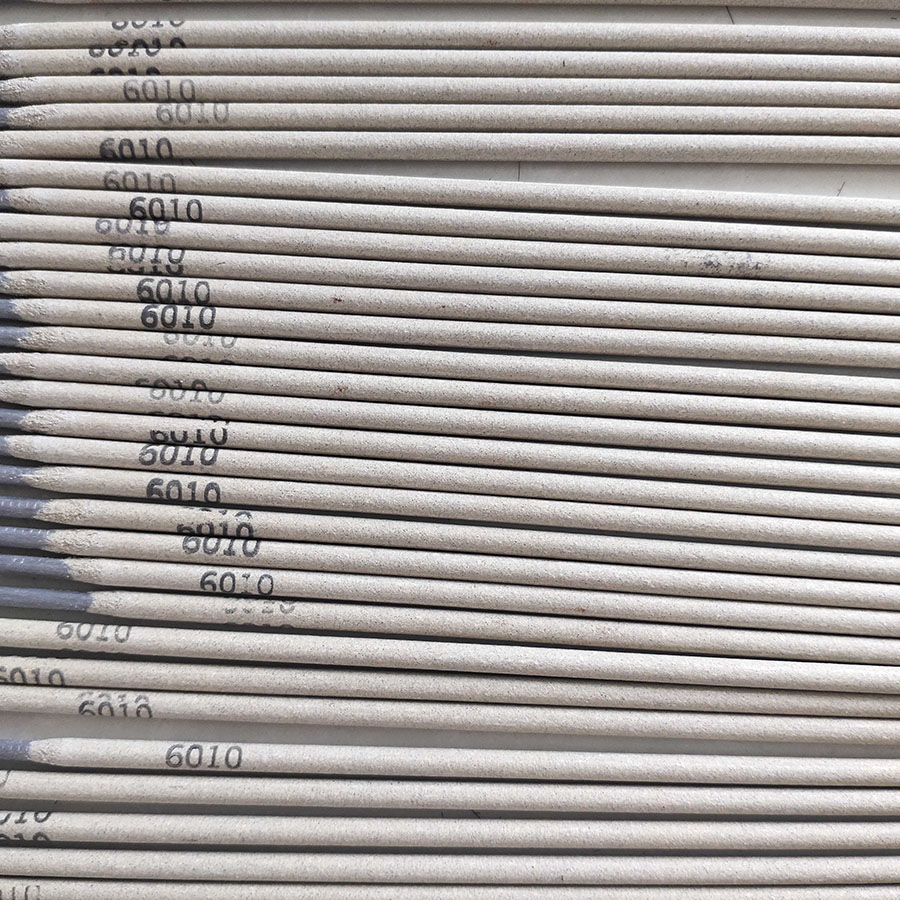
Professionals in the welding industry understand that the choice of welding electrode can significantly impact the quality and integrity of a weld. This makes knowledge about electrodes not just beneficial but necessary for those striving to achieve excellence in their craft. From experience, using the right electrode tailored to the specific materials and conditions of a project can enhance both efficiency and overall outcomes.
Welding electrodes are characterized by their composition, which matches or complements the metals being welded.
There are primarily two categories of electrodes consumable and non-consumable. Consumable electrodes, often coated in a flux material, melt during the welding process, contributing to the weld pool. These are typically used in shielded metal arc welding (SMAW) and gas metal arc welding (GMAW), with popular variants including E6010, E6011, and E7018, each suitable for different applications and conditions. Knowing when to use a specific type, such as E7018 for structural welding due to its high strength and ductility, can elevate the quality of the final structure.
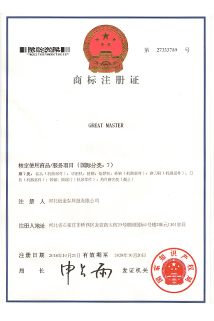
In contrast, non-consumable electrodes like tungsten are used in tungsten inert gas (TIG) welding, where they remain relatively intact. These electrodes are preferred for tasks demanding precision and clean welds, as they provide greater control and minimize contamination.
welding electrode
Exhibiting expertise involves understanding factors such as amperage settings, polarity, and base material compatibility. An expert welder will adjust these variables to suit the electrode type and metal thickness, achieving optimal penetration and fusion. This deep knowledge allows for adaptation in varied scenarios, whether welding in open environments susceptible to wind or in constrained spaces within complex assemblies.
Authority in welding dictates adherence to established standards and protocols, ensuring safety and compliance with industry regulations. Electrode handling, storage, and maintenance also fall under this scope. Proper storage conditions, such as controlling humidity to prevent moisture absorption, preserve electrode integrity and performance. Reputable sources, like AWS (American Welding Society), offer guidelines and certifications that reinforce best practices and confidence in electrode use.
Trustworthiness in the field is built through consistent delivery of quality welds and adherence to safety protocols, minimizing defects and rework while maximizing project lifespan. Transparency in sharing detailed observations and troubleshooting common issues, such as porosity or slag inclusion, further establishes reliability.
Welding electrodes, when chosen and utilized correctly, form the backbone of successful welding projects. Insight gained through hands-on experience and continuous learning carves the path to mastery in welding, ensuring safety, efficiency, and longevity of welds across all applications.