Selecting the right welding rod is crucial for achieving optimal results in any welding project. Understanding the subtle nuances and specific benefits each type offers can significantly impact both the quality and efficiency of your work.
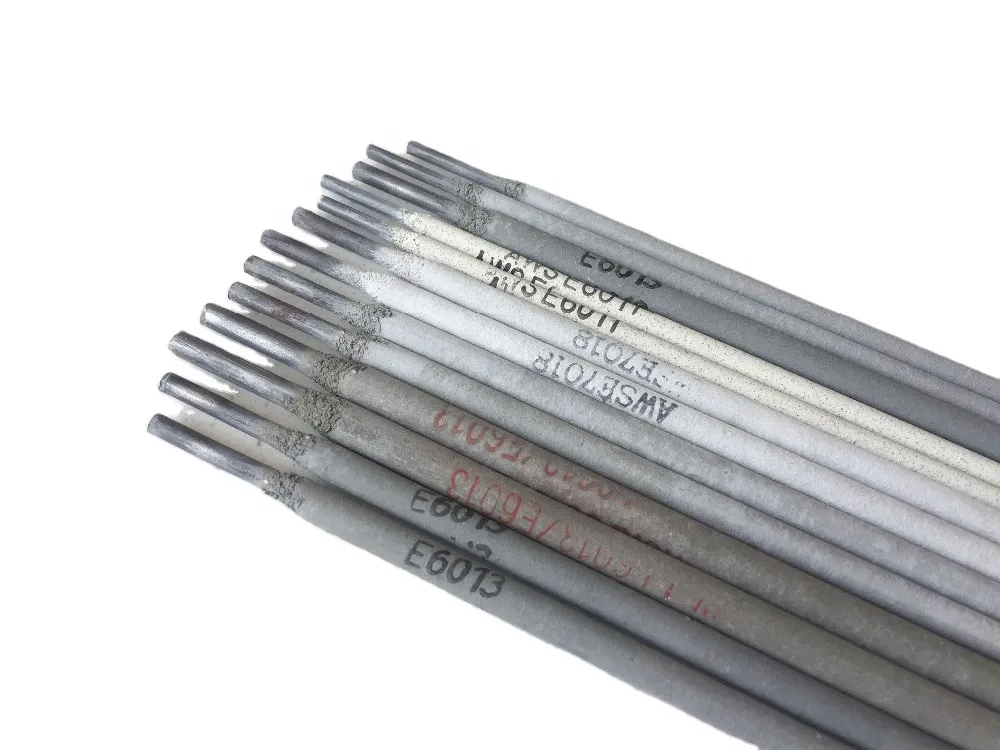
Welding rods, also known as filler metals, serve as the connecting agent between two pieces of metal, enabling the fusion process during welding. They come in various compositions and coatings, each designed for specific materials and conditions. One of the most widely used categories is the consumable electrode for manual metal arc welding, commonly referred to as SMAW or MMAW.
Operators must first assess the base material to choose an appropriate welding rod. For instance, mild steel rods are versatile and commonly employed across numerous industries due to their compatibility with a wide range of metals and ease of use. For stainless steel applications, stainless steel rods are essential to prevent corrosion and maintain the integrity of the welded joint.
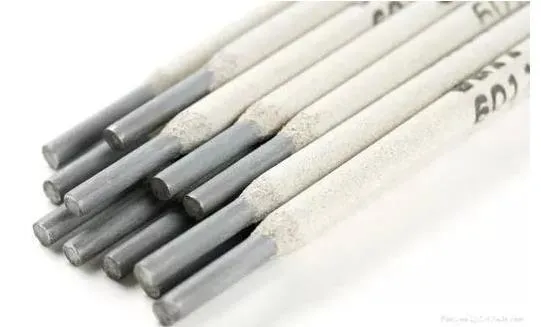
Apart from the base metal, the position of the weld greatly influences rod selection. Some rods are designed specifically for vertical and overhead positions, an often-overlooked detail that can significantly affect the ease of welding and the quality of the weld in challenging orientations. For vertical welds, E7018 rods are a popular choice due to their reliable penetration and strong tensile strength.
Understanding the coating of welding rods is another key aspect. Coatings serve multiple functions they stabilize the arc, protect the weld pool from atmospheric contamination, and can also influence the mechanical properties of the weld. Rutile-coated rods, for instance, are known for their smooth arc and aesthetic finishes, making them ideal for projects where presentation is critical. On the other hand, cellulose-coated rods provide deep penetration and are preferred for structural welding and fieldwork.
welding rod
Furthermore,
considering the welding environment is paramount. Welds that will be exposed to harsh elements or require high-impact strength should employ low-hydrogen rods, such as E7018. These rods minimize the risk of hydrogen-induced cracking, thereby enhancing the durability of the weld in demanding conditions.
Safety and storage are additional factors to consider when working with welding rods. Proper storage is essential to prevent moisture absorption, which can lead to hydrogen embrittlement and porosity in the weld. Keeping rods in an oven at required temperatures ensures their prime condition and usability for critical projects.
The cost implications should also be factored into the decision-making process. While premium welding rods might have a higher upfront cost, their reliability and quality can lead to savings by reducing rework and enhancing productivity.
In conclusion, selecting the correct welding rod requires a blend of knowledge and practical expertise. By considering the base material, welding position, environmental conditions, and specific requirements of the project, operators can ensure the integrity and quality of their welds. Continuous learning and staying updated with the latest materials and technologies can further refine your skills and improve the outcomes, establishing you as a trusted and authoritative figure in the field of welding.