Stick welding, often referred to as shielded metal arc welding (SMAW), is a widely employed technique in the metal fabrication industry due to its versatility and simplicity. Among its various electrodes, the 6010 welding rod stands out as a popular choice for many welders. This article delves into the intricacies of using the 6010 electrode in stick welding, offering insights and expert advice to enhance your welding endeavors.
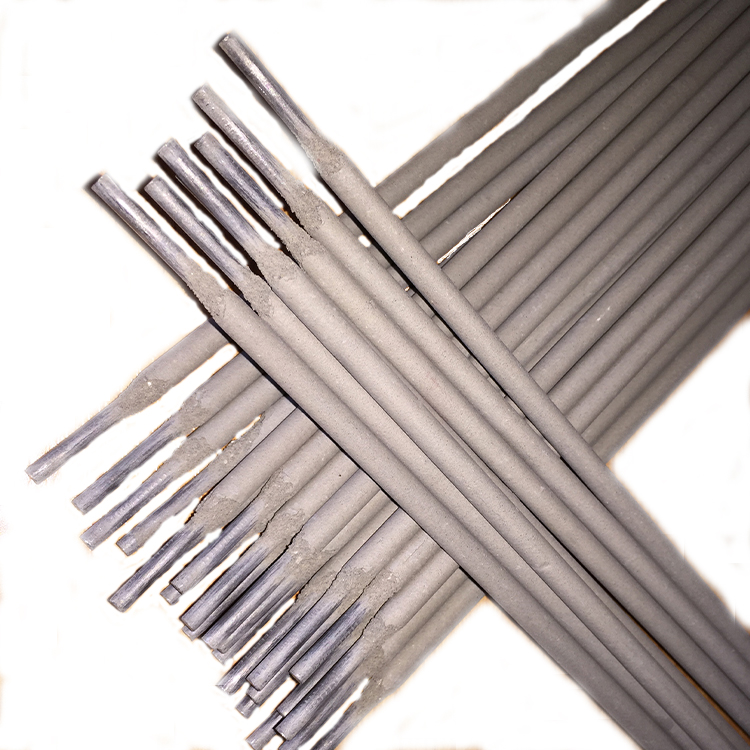
A notable feature of the 6010 electrode is its deep penetration capability. This makes it an excellent choice for welding through rusted, painted, or unclean surfaces where other electrodes might falter. This advantageous trait is attributed to the cellulose-based coating of the 6010 electrodes, which produces an aggressive arc capable of cutting through impurities. For beginners and experts alike, understanding the arc characteristics of the 6010 rod is crucial. The arc tends to be forceful and spatter-prone, thus requiring a steady hand and precise control to achieve clean welds.
When discussing the real-world application of the 6010 electrode, it’s essential to highlight its preferential use in high-pressure pipe welding industries. Welders working on pipelines, storage tanks, and pressure vessels frequently choose 6010 rods due to their ability to deliver reliable and robust welds in challenging conditions. This electrode excels in all positions, particularly vertical-up and overhead, proving itself indispensable across different environments and structures.
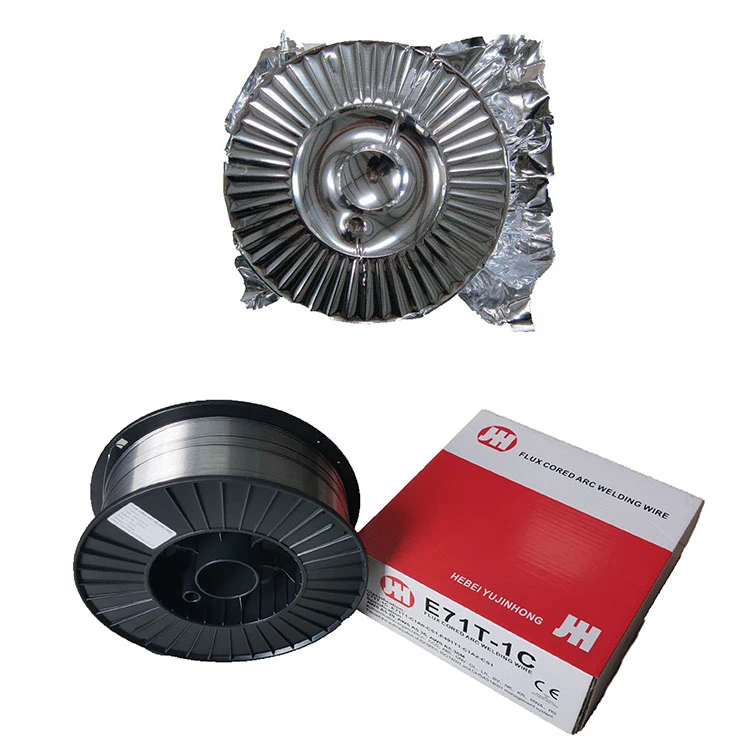
The versatility of the 6010 electrode extends to its compatibility with different welding machines. Most welding outfits, whether old transformer-based welders or modern inverter-type machines, support 6010 rods, provided the welder possesses the right skill to handle them. However, due to their particular arc characteristics, beginners might find it slightly challenging to master initially. It's essential to start with practice runs on scrap materials, focusing on maintaining a consistent travel speed and angle to minimize defects like undercut or excessive spatter.
stick welding 6010
Despite its strengths, the 6010 electrode also presents some challenges which are imperative to address to ensure high-quality welds. The rod can generate substantial spatter, a typical inconvenience when welding in a clean workshop environment. Wearing appropriate personal protective equipment (PPE) is crucial, especially given the intense arc brightness. Grinding and post-weld cleaning are often necessary steps to ensure a clean finish, particularly in visible weldments. Moreover, meticulous attention to electrode storage is required to prevent moisture absorption that could negatively impact weld quality.
Trusted voices in the welding community often emphasize the role of electrode manipulation in maximizing the 6010 rod’s potential. Techniques such as the whip and pause, or weaving, are commonly used to control heat input and ensure thorough fusion while minimizing defects. James T., a seasoned welding instructor with over 25 years of experience, shares that “Mastering the whip and pause technique with 6010 rods is akin to learning the rhythm of the weld; it’s what separates a good welder from a great one.” This testimonial underscores the importance of ongoing practice and skill refinement when working with 6010 electrodes.
Safety cannot be overstated when handling any welding process,
and using 6010 rods is no exception. Welders should ensure proper ventilation to mitigate inhalation of harmful fumes, especially given the cellulose coating’s tendency to produce more smoke. Safety glasses, gloves, and flame-resistant clothing form the basic protective gear every welder should wear to prevent injuries from sparks and spatter.
In conclusion, the 6010 stick welding electrode continues to be a staple in the industry due to its versatility and robust performance under various conditions. Whether you are welding in a fabrication shop or on-site pipeline project, the knowledge and expertise surrounding the use of 6010 rods will significantly impact the quality and durability of your welds. By mastering this electrode’s distinct characteristics and adhering to best practices in safety and technique, welders can harness its full potential to produce outstanding results.