The world of welding is an expansive and intricate domain, filled with tools, techniques, and technologies that cater to both simple and complex projects. Among the numerous tools employed by welding professionals, the welding stick - commonly referred to as a welding rod or electrode - plays an indispensable role. For both novices and seasoned welders, understanding the subtleties of welding sticks is crucial not only for the quality of the weld but also for safety and efficiency. Let's delve into the core aspects that make welding sticks a focal point of discussion in welding communities and industrial setups alike.
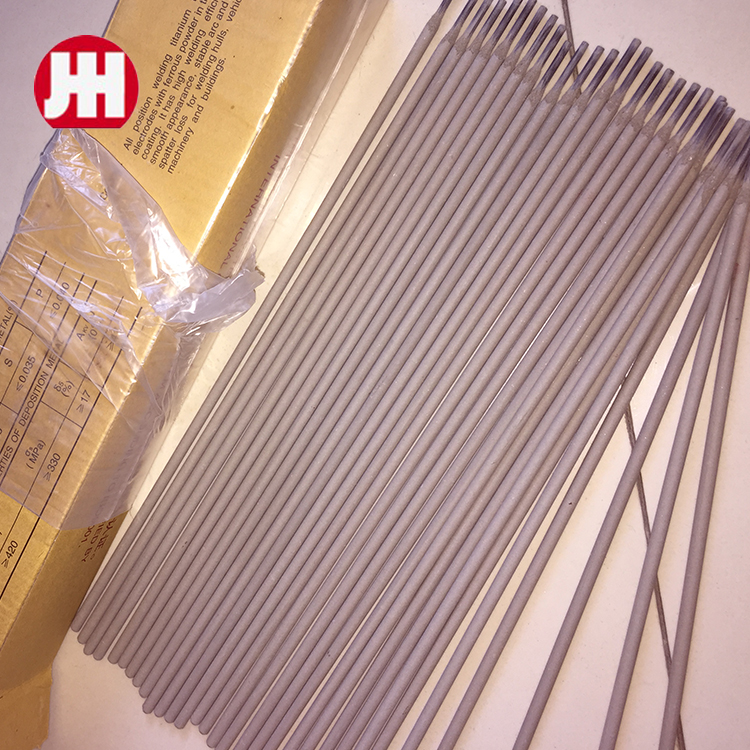
Welding sticks are at the heart of the Shielded Metal Arc Welding (SMAW) process, which remains one of the most versatile and widely used welding techniques worldwide. The selection of a welding stick is critical, influenced by the base metal type, thickness, and desired weld properties.
The composition of the welding rod, coated with flux, adds another layer of complexity. This coating is not merely a protective layer but actively contributes to stabilizing the arc, preventing oxidation, and influencing the mechanical properties of the weld.
Manufacturers provide welding sticks with specific identifiers, indicating their tensile strength, weld position capabilities, and current type - whether alternating current (AC) or direct current (DC). For instance, a popular choice like the E6010 would denote a versatile electrode for all positions, demanding a profound understanding of the underlying material to optimize weld quality. Professional welders often emphasize the importance of choosing the right electrode to achieve a strong, clean weld, minimizing defects such as porosity or cracking.
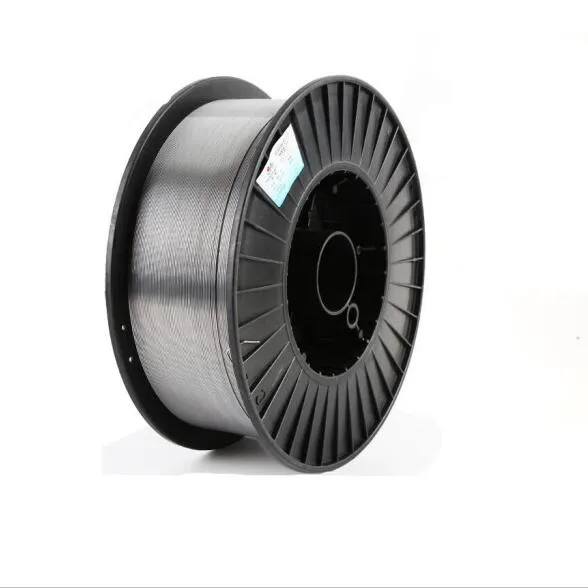
welding stick
Moreover, welding rods are pivotal in projects needing structural precision and integrity, from routine maintenance jobs to constructing massive infrastructure. Experienced welders, drawing from years of hands-on expertise, often play a mentoring role. They warn of the pitfalls of improper stick selection, such as the availability of moisture-resistant options that reduce hydrogen-induced cracking - a significant issue in outdoor or high-moisture environments.
Advanced training programs and certifications underscore the importance of knowledge about welding sticks. These programs stress the necessity to couple expertise with quality equipment - a factor that reinforces trustworthiness and safety when employing welding sticks in any project. High-quality brands have built their reputation on reliability and consistent performance, which matters not only when undertaking a large industrial project but also on a personal level, where amateur enthusiasts forge and bond metal art in their own spaces.
The evolution of welding technology continues to advance, but the core essence of welding, including tools such as the welding stick, remains pivotal. Experts predict a future where welding rods will integrate even more with technology, potentially improving efficiency, reducing human error, and offering more sustainable solutions. Such advancements promise an exciting horizon, but the timeless wisdom rooted in experiential knowledge and skilled handling of welding sticks will continue to ensure the art of welding flourishes, underscored by professionalism and an unyielding commitment to quality.