In the world of metal fabrication, achieving precision, strength, and reliability in welds is crucial, and the right choice of welding wire can make a significant difference. Among the options available, TIG and MIG welding wires stand out for their unique benefits, each playing a vital role depending on the specific requirements of the project. Drawing from years of experience in welding and a thorough understanding of industry standards, one can appreciate the intricate details that influence the selection process for TIG and MIG wires.
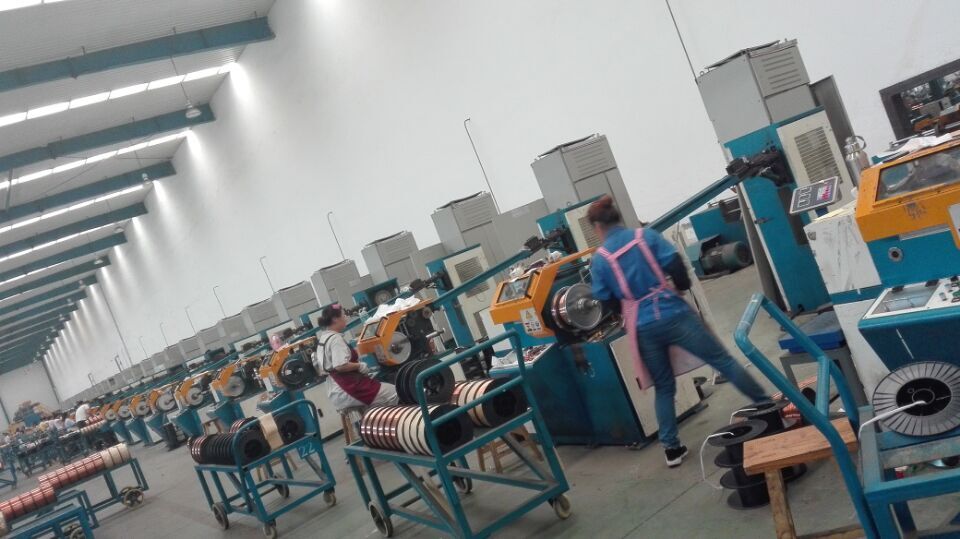
TIG (Tungsten Inert Gas) welding wire is renowned for delivering high-quality, precise welds, making it indispensable for tasks requiring finesse and a polished finish. TIG welding wires are often employed in scenarios involving thinner materials, such as stainless steel and non-ferrous metals like aluminum and magnesium. The ability of TIG welding wire to produce a clean and aesthetically pleasing weld without spatter or slag is highly valued in industries where appearance and integrity are paramount, such as aerospace and automotive sectors.
Expertise in TIG welding reveals that the choice of filler material is crucial. For instance, ER 70S-6 is a versatile TIG wire that provides excellent puddle control and is adept at handling surface contaminants like rust or oil. This particular wire is favored for its adaptability to a wide range of welding applications, enhancing productivity without compromising quality. Additionally, the low splatter and smooth bead appearance it offers contribute significantly to reducing post-weld cleanup time, which is often a hidden cost factor in welding operations.
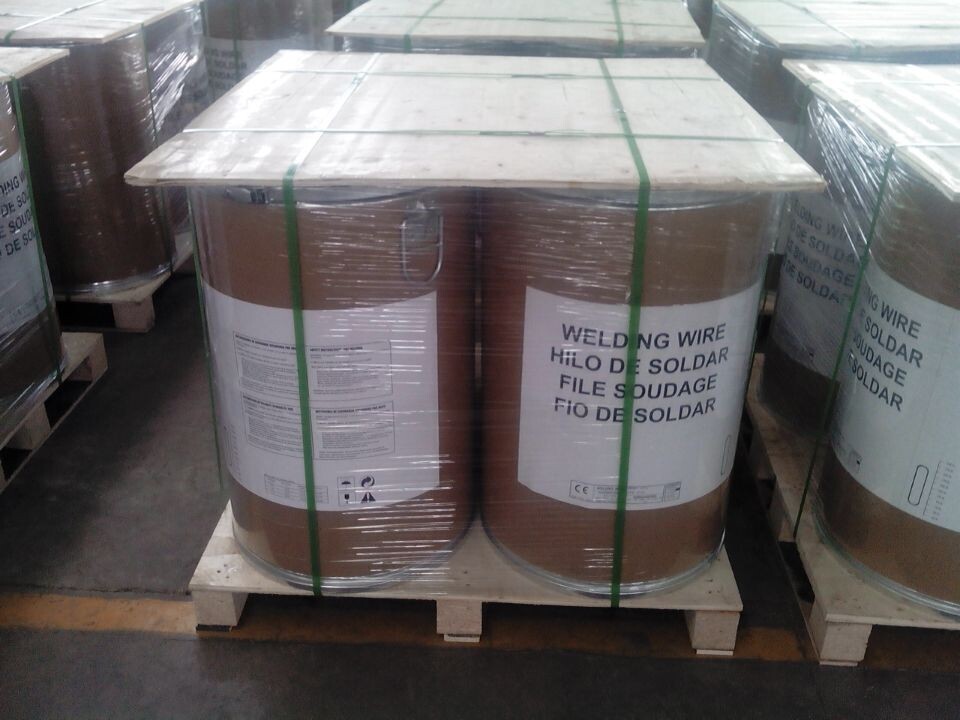
In contrast, MIG (Metal Inert Gas) welding wire is prized for its speed and efficiency, making it the preferred choice for high-volume production environments. MIG welding wires are typically used for thicker materials that require robust penetration and a stronger weld. The fast deposition rates of MIG wires ensure that projects are completed quicker, optimizing operational workflow and resource allocation.
tig mig welding wire
Understanding the technical nuances of MIG welding wires, such as ER70S-3 and ER70S-6, reveals why they are a mainstay in industries like construction and heavy equipment manufacturing. These wires provide consistent arc performance and high tensile strength, essential for structural applications. Moreover, the versatility of MIG wires allows for welding in various positions, enhancing their applicability in complex assemblies.
Authoritativeness in welding practices is not just about choosing the right wire but also about implementing welding procedures that maximize the wire's inherent properties. Trustworthiness in results comes from rigorous testing and adherence to industry standards, ensuring welds that stand the test of time and meet rigorous safety guidelines.
In conclusion, the judicious selection between TIG and MIG welding wires is integral to achieving desired outcomes in metal fabrication.
Each type of welding wire has its own advantages that cater to specific needs. Professionals equipped with the right knowledge and insights can leverage these characteristics to deliver exceptional results, ensuring efficiency, quality, and reliability in their welding projects. Passionate dedication to mastering these welding processes not only enhances one's skill set but also builds a foundation of trust and authority in the competitive field of metal fabrication.