Mastering the nuances of 025 flux core wire can significantly enhance your welding projects, be it for hobbyists or professionals. Its widespread application in industries such as automotive, construction, and small-scale manufacturing underlines its indispensableness. However, to reap the full benefits, understanding the intricate details of its usage, advantages, and potential pitfalls is paramount.
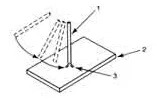
025 flux core wire, a self-shielding wire, is renowned for its ease of use and versatility. It eliminates the need for an external gas tank, as it produces its protective gas shield during the welding process. This feature proves invaluable, especially when working outdoors or in less controlled environments where wind might otherwise disrupt the shielding gas. This ability to weld in conditions not ideal for traditional MIG welding is a significant advantage, making 025 flux core wire a go-to choice for fieldwork or repair jobs.
From an expert's perspective, one of the standout features of 025 flux core wire is its ability to generate deep penetration, which is especially effective on thicker materials. This characteristic makes it particularly suited for heavy-duty welding tasks where strength and durability are critical. Moreover, its forgiving nature when working with dirty or rusty materials adds another layer of utility, offering a more robust weld even when surface preparation is less than ideal.
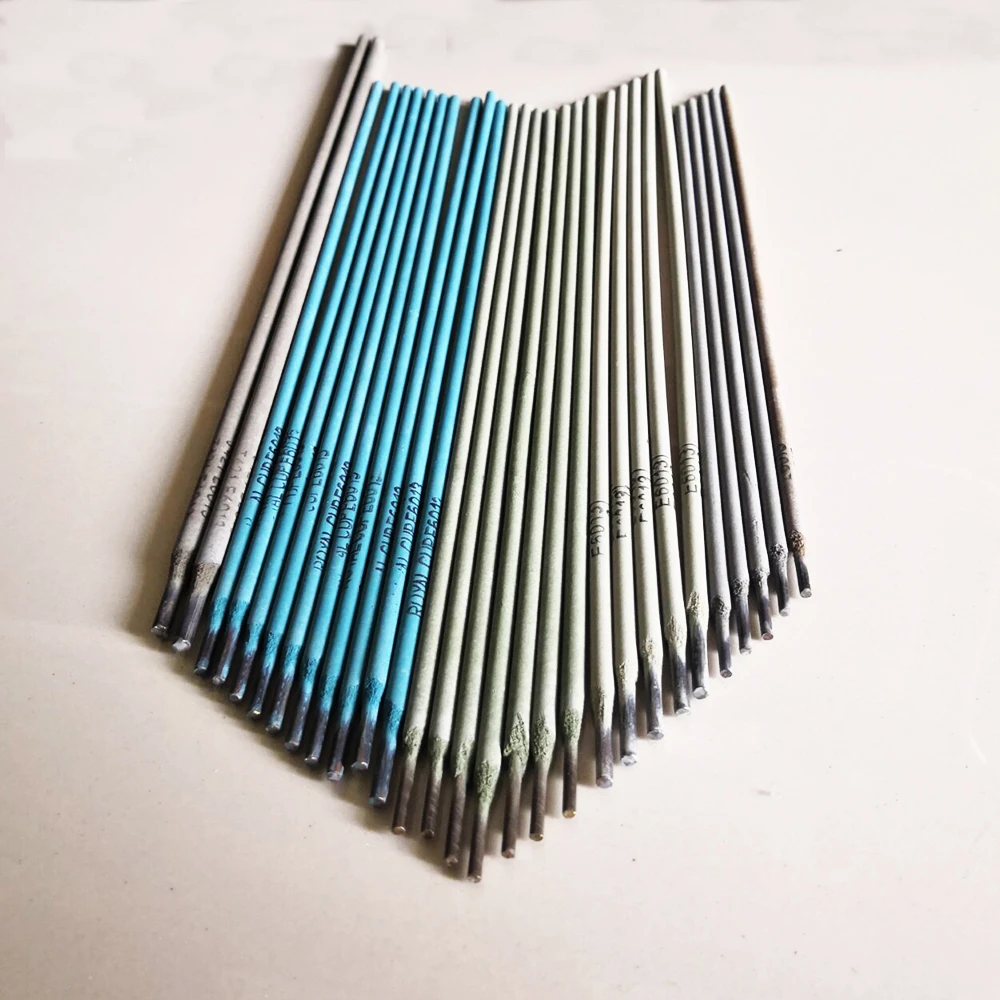
However, using 025 flux core wire isn't without its challenges. A common issue users face is slag removal,
a byproduct of the self-shielding nature of the wire. This slag needs to be chipped away after welding, which can be time-consuming and might impact the speed of production. Additionally, the use of flux core wire in thin materials requires careful adjustment of parameters, as excessive heat can lead to burn-through, compromising the integrity of the weld.
025 flux core wire
To ensure optimal performance with 025 flux core wire, attention must be paid to the machine settings and technique. Experts suggest maintaining the wire feed speed and voltage settings tailored to the material thickness and position of the weld. Furthermore, proper storage of the wire is crucial to prevent contamination that could affect the weld quality. Following these best practices and adjustments can enhance the finished product's aesthetics and structural strength.
Trustworthiness in any product-related discourse comes not just from the product's performance but also from the feedback and consensus within the welding community. Users consistently highlight the wire’s ease of operation in various forums and reviews, lending credence to its reputation. Moreover, manufacturers continue to innovate, providing users with detailed guides and tutorials to maximize the wire’s effectiveness. This ongoing support reinforces the confidence users have in relying on 025 flux core wire for their demanding projects.
Integrating authoritative voices, such as industry veterans and certified welding inspectors, is also essential in establishing the reliability of information surrounding 025 flux core wire. Testimonials from experts who have leveraged this wire in complex projects can provide invaluable insights and encourage best practices among less experienced users.
Ultimately, 025 flux core wire stands out as a versatile, powerful tool in the arsenal of modern welders. While it demands a certain level of understanding to use effectively, the benefits it offers in terms of flexibility, penetration, and ease-of-use make it an excellent choice for a wide range of welding applications. With the support of a strong community and ongoing manufacturer advancements, adopting best practices and learning from real-world experiences can lead to high-quality, durable results that stand the test of time.