Understanding the various sizes of welding rod 7018 is crucial for welders aiming to enhance their craft, as it greatly impacts the quality and efficiency of welding projects. This electrode is known for its versatility and strength, making it a favorite among both professional welders and DIY enthusiasts. To leverage its full potential, it's important to match the appropriate size to the specific job required.
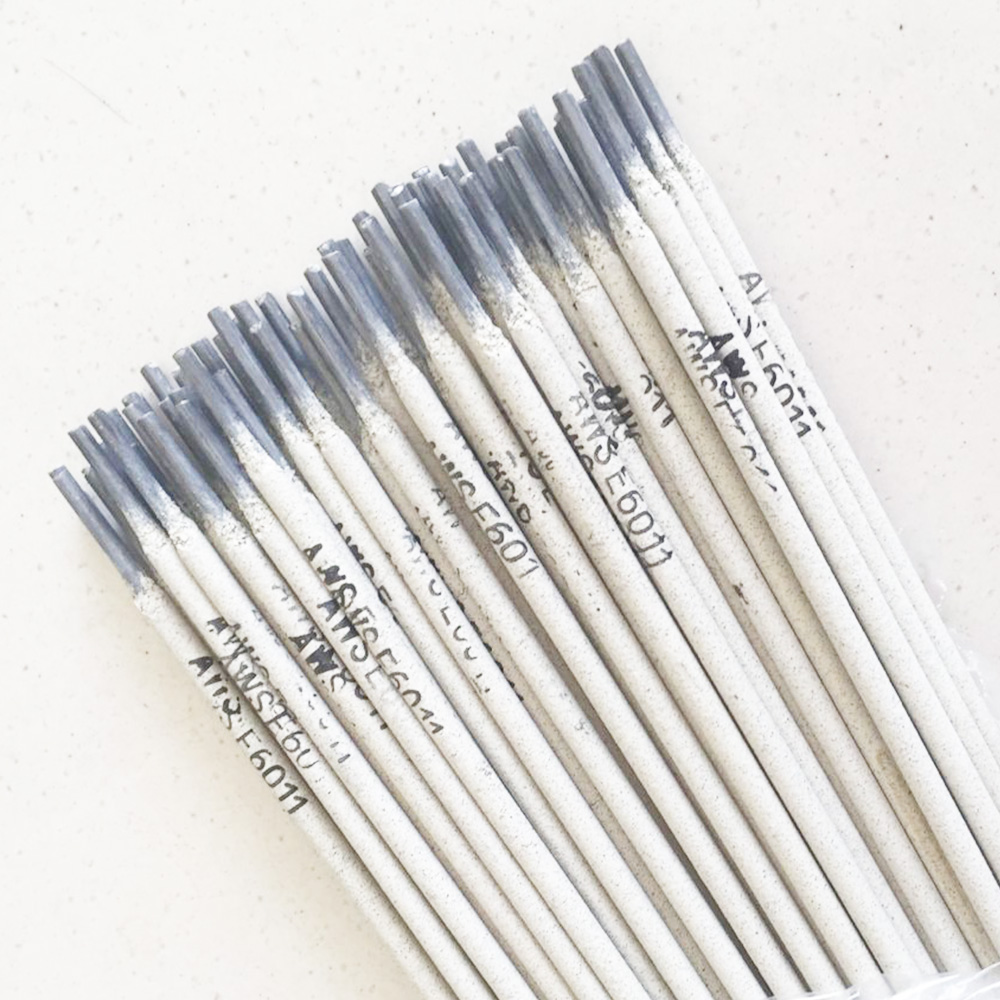
7018 welding rods are typically available in various diameters, ranging from 1/16 inch to 5/32 inch, and each size serves a different function. For instance, a smaller diameter, such as the 1/16 inch, is ideal for delicate work or for welding thin sheets of metal where precision is paramount. This size is instrumental in minimizing heat input, reducing the risk of warping or burn-through in thin materials.
In contrast, larger diameters like 1/8 inch or 5/32 inch are preferred for heavy-duty work. These sizes are adept at handling thicker metals and can produce a robust weld capable of withstanding substantial stress. The greater amount of filler metal deposited per pass increases efficiency in large projects, reducing both time and effort involved. Moreover, these larger rods are designed to deliver a deeper penetration, creating stronger joints that are less prone to defects.
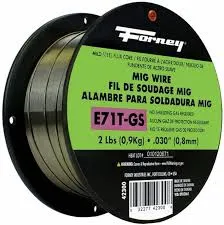
Another factor to consider when selecting the size of a 7018 rod is the position of the weld. Smaller rods are easier to manage in awkward positions, such as overhead or vertical welds, due to their manageable size and improved control. Conversely, thicker rods might be suited for flat and horizontal positions where speed and efficiency are prioritized over maneuverability.
Amperage settings also correlate with the size of the rod used. A smaller rod requires a lower amperage, which is beneficial for working with thin or sensitive materials that might distort under excessive heat. Larger rods, on the other hand, demand higher amperage settings to achieve full penetration and proper fusion, making them suitable for thicker, more resilient materials.
welding rod 7018 sizes
Beyond practical applications, the choice of welding rod size can significantly affect the aesthetic outcome of the weld. A properly sized rod ensures a clean, professional finish with minimal spatter and slag. This is particularly crucial in industries where the appearance of welds is as important as their strength, such as in automotive and decorative metalwork.
For those seeking to optimize their welding projects and boost productivity, understanding the implications of welding rod sizes coupled with knowledge of specific applications and materials is indispensable. This expertise not only improves the quality of the welds but also ensures safety by preventing potential failures due to improper welding techniques or incompatible tools.
Recognizing the nuances between different 7018 rod sizes empowers welders to make informed decisions tailored to their unique project needs. With careful selection, from basic repairs to advanced fabrications, operators can achieve superior results that are both structurally sound and aesthetically pleasing.
In summary, the strategic selection of welding rod 7018 sizes is not merely a technical consideration but a pivotal component in ensuring the success and integrity of welding endeavors. By mastering this aspect, one can ensure an enhanced level of craftsmanship that aligns with professional standards. With continued practice and understanding, welders can perfect their approach, adapting seamlessly to the diverse demands of the modern industry landscape.