Choosing the right MIG wire for stainless steel applications can be a complex decision that involves understanding both material properties and the demands of specific projects. Stainless steel, revered for its resistance to rust and corrosion, plays a critical role in industries ranging from automotive to construction. As such, the MIG wires used in welding this material need to not only match the durability and aesthetics of stainless steel but also guarantee performance.
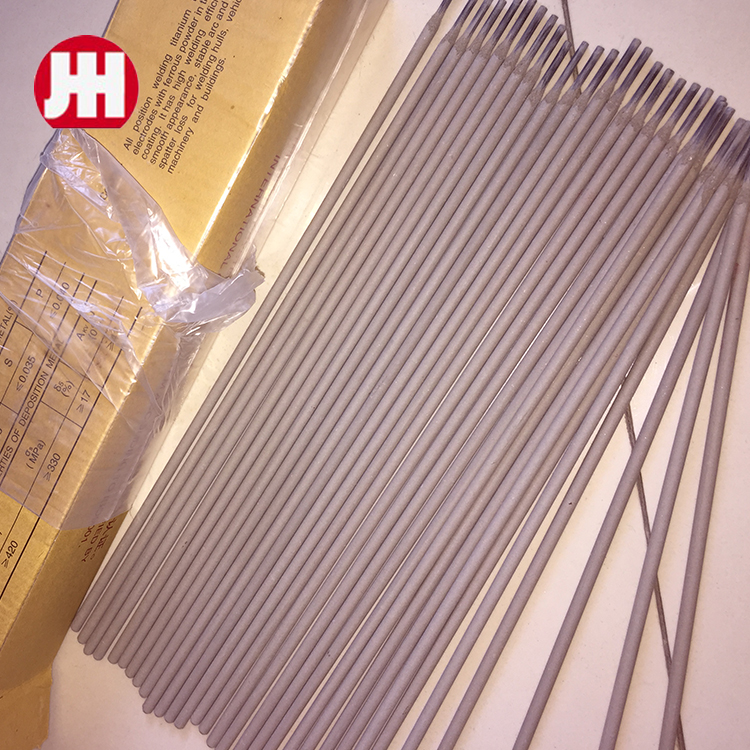
Exploring the various types of stainless steel MIG wires reveals several options, each with inherent strengths tailored to specific stainless steel grades and environments. For instance, wires with a higher CrNi content, such as the ER308L, are particularly suited for welding the majority of austenitic stainless steels like 304. These wires are known for their ability to produce welds that are both aesthetically pleasing and reliable, maintaining the mechanical properties of the base material with minimal risk of corrosion.
However, to achieve optimal weld results, the MIG process demands more than just the selection of premium wire. Expertise in managing welding parameters such as amperage, voltage, and travel speed is essential. Through a precise understanding of arc characteristics and the synergistic behavior between wire and shielding gas, welders can minimize spatter, porosity, and other common weld defects. This highlights the necessity for tailored training, which arms welding professionals with the skillset to maximize the capabilities of their chosen wire.
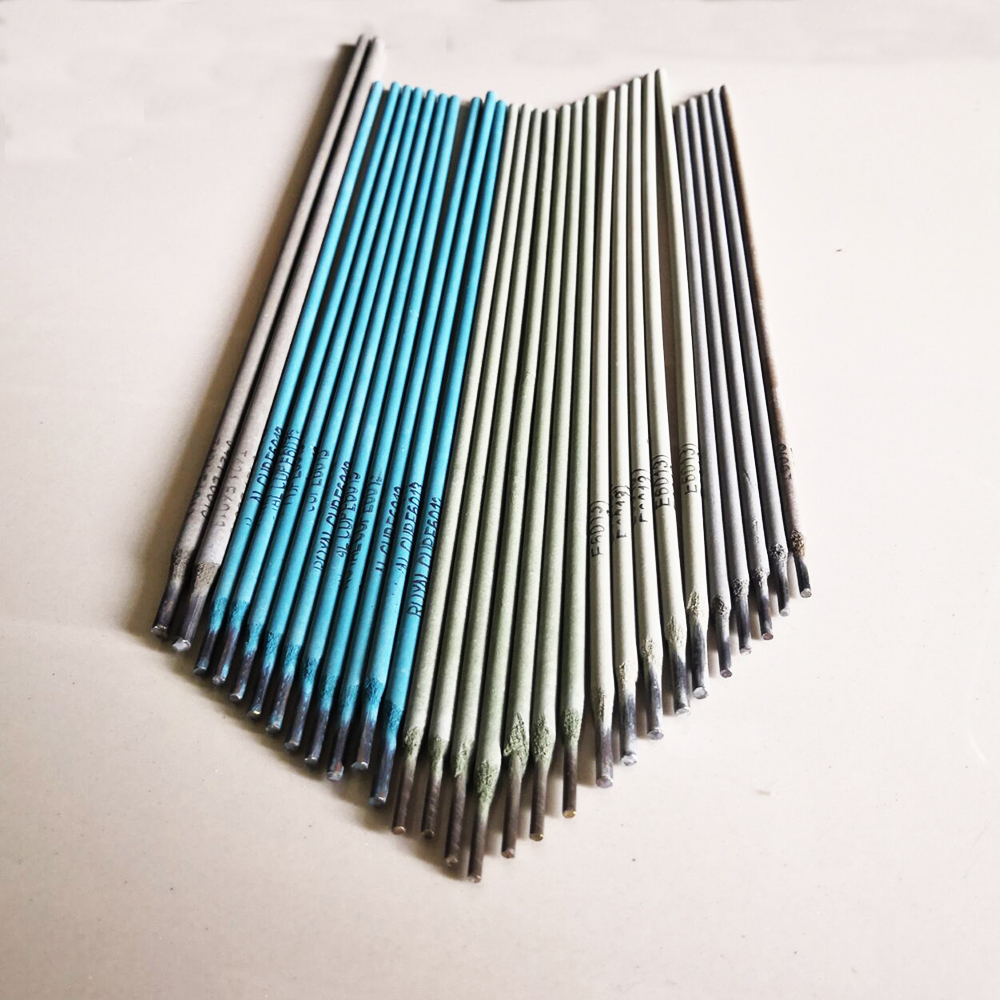
Experience is invaluable in troubleshooting the wide array of potential issues inherent in welding processes. Professionals recount instances where adjustments in wire feed speed or alterations in electrode angles have transformed problematic welds into showcases of precision and strength.
Such insight proves invaluable when dealing with problematic batch runs or unique project constraints. Moreover, professional forums and user communities often serve as reservoirs of collective knowledge, offering advice and shared experiences that contribute to a deeper, more practical understanding of stainless steel MIG welding.
china mig wire ss
Authoritativeness in the field of MIG welding stainless steel cannot be overstated. Consultation with manufacturers and seasoned industry veterans can provide access to a wealth of information about the latest developments in wire technology, from flux-cored options to innovative coating advancements that impact feeding characteristics and arc stability. Trusted industry publications and certified training courses offer in-depth insights into how wires are fabricated and tested, ensuring compliance with rigorous industry standards.
When discussing trustworthiness in MIG wire for stainless steel, the importance of certification and quality assurance processes comes to the fore. Manufacturers who adhere to stringent ISO standards and provide thorough documentation of their quality protocols instill confidence. Additionally, third-party certifications and endorsements by recognized welding bodies offer invaluable assurances that the wire will perform as expected under demanding conditions.
In conclusion, the use of stainless steel MIG wire is an essential component in achieving high-quality welds that are both functional and visually appealing. By leveraging experience, expertise, authoritativeness, and trustworthiness, industry professionals are well-positioned to select the appropriate wire type for their specific applications, ensuring both project success and long-term durability of the welds they produce. As the stainless steel industry continues to evolve, so will the technologies and techniques used in MIG welding, promising ongoing advancements and improved outcomes for welders across various sectors.