DC electrode welding is a critical process in modern manufacturing, offering unique advantages and requiring specific expertise for optimal execution. Understanding its intricacies ensures high-quality results, essential for maintaining product integrity and meeting industry standards.
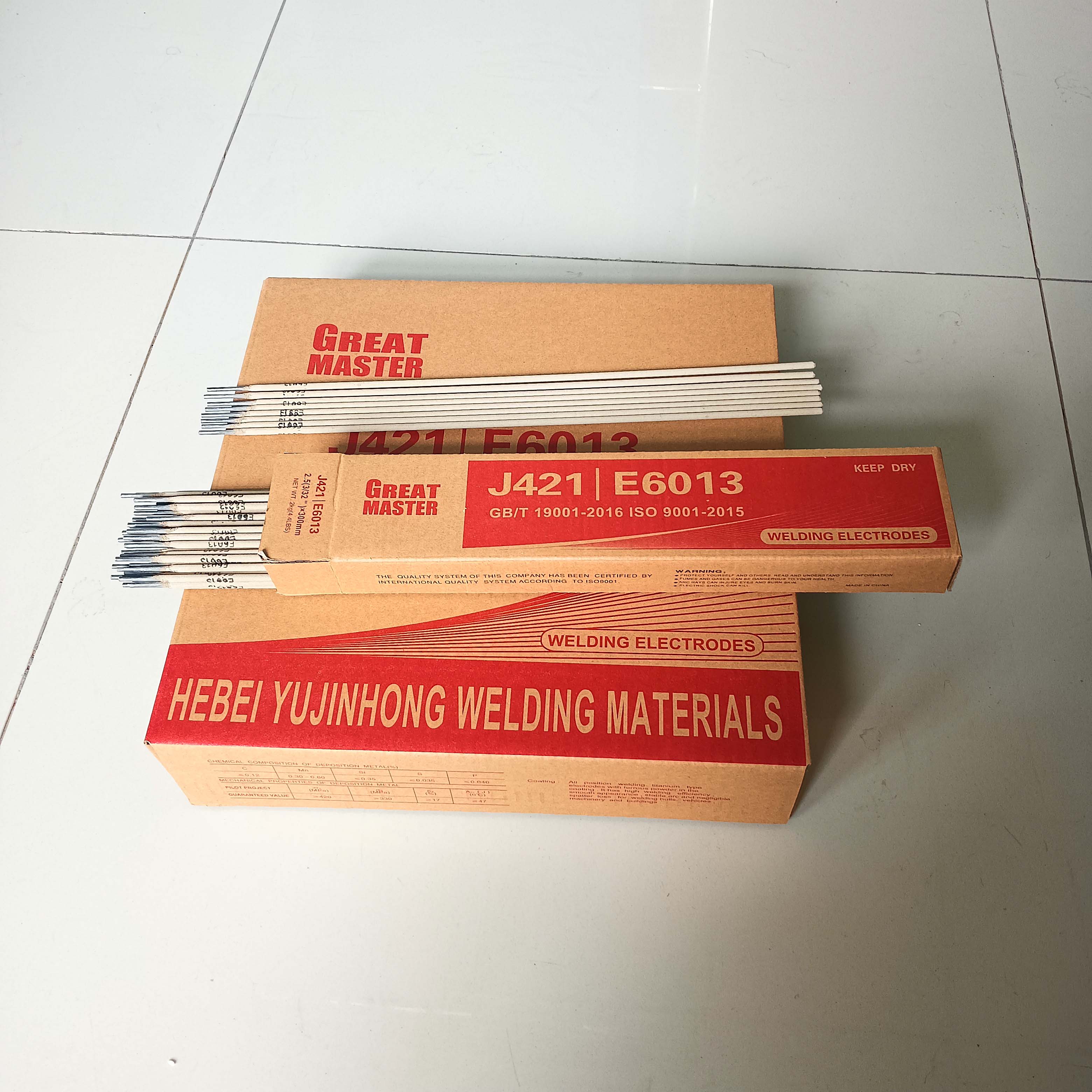
Direct current (DC) electrode welding is a preferred method for a variety of industrial applications due to its stable arc and deep penetration capabilities. This welding technique uses a constant direct current power source where the electrode is negatively charged (DCEN) or positively charged (DCEP), each configuration offering distinct benefits. DCEN is often used for thinner materials, providing fast welding speeds with less heat input. On the other hand, DCEP is more suitable for thicker materials, delivering deeper penetration with increased heat for robust welds.
A key advantage of DC electrode welding is its versatility. It’s compatible with a broad range of materials including steel, stainless steel, and titanium. This compatibility is particularly advantageous in fields like automotive, shipbuilding, and structural engineering where varied materials and thicknesses are common. Understanding the material properties and choosing the appropriate DC electrode welding technique is crucial for achieving optimal results.
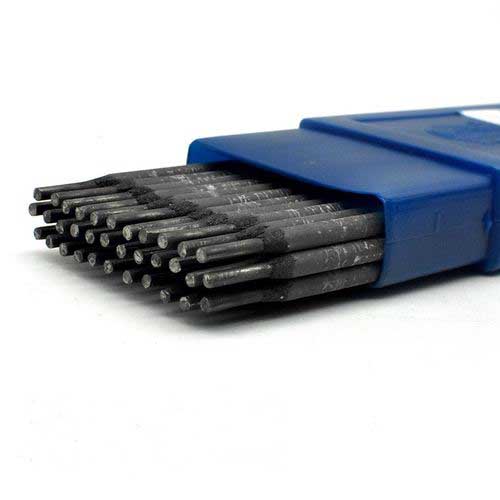
Experience plays a vital role in maximizing the benefits of DC electrode welding. Experienced welders are adept at manipulating the electric arc, adjusting the current, and maintaining the correct angle and speed, all of which are essential for producing clean and precise welds. This skill, honed over years, ensures minimal defects and optimizes the structural integrity of the welded materials. Expertise in this area provides a competitive edge, ensuring products meet stringent quality and safety standards.
Expertise also involves a deep understanding of welding equipment and maintenance. Regular equipment checks and adherence to safety protocols prevent malfunctions and accidents, safeguarding both the welder and the work environment. Moreover, innovations in welding technology, such as inverter-based power sources, enhance the efficiency and portability of welding equipment, making them more adaptable to various job sites.
dc electrode welding
Authoritativeness in DC electrode welding is established through adherence to recognized standards and certifications. Welding professionals often pursue certifications from authoritative bodies like the American Welding Society (AWS) or the International Institute of Welding (IIW). These certifications attest to a welder’s skills and knowledge, boosting credibility and instilling confidence in clients and employers.
Furthermore, trustworthiness is paramount in sectors where welding is integral to product safety and longevity. Consistent quality control and adherence to industry regulations ensure that welded products perform reliably under stress. Accurate documentation and traceability of welding procedures add an additional layer of accountability and confidence in the manufacturing process.
For manufacturers, investing in skilled welders and maintaining high-quality welding equipment directly impacts product quality and operational efficiency. As such, companies that prioritize expert training and uphold stringent welding standards distinguish themselves from competitors, offering robust and reliable products to the market.
In conclusion, DC electrode welding is a cornerstone of modern fabrication, requiring a blend of experience, expertise, authoritativeness, and trustworthiness for optimum performance. By focusing on these attributes, manufacturers can enhance their product offerings, boost operational efficiency, and ensure compliance with industry standards, thereby fortifying their position in the competitive landscape.