Electrodes welding is a foundational process in the world of metal fabrication, valued for its versatility and reliability across various industries. This method, known for its efficiency in fusing metals, relies heavily on the choice and quality of electrodes utilized, which serve as a critical component in determining the strength and durability of the weld. An understanding of electrodes welding thus demands a grasp of the types of electrodes and their specific applications.
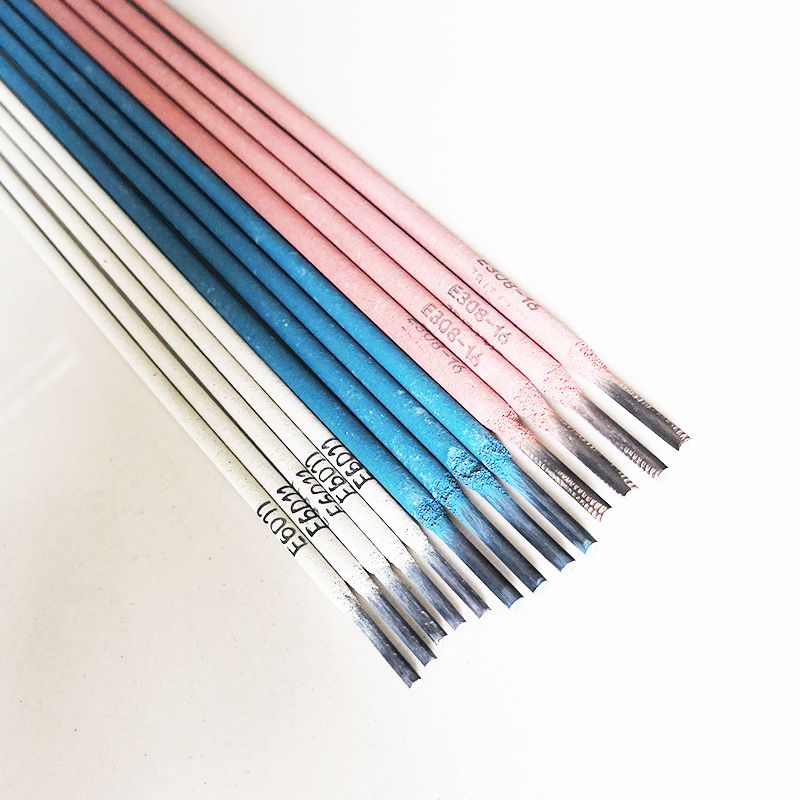
Electrodes in welding act as a conductor, transmitting current to the workpiece to melt the metals that are to be joined. There are different types of welding electrodes, primarily categorized into consumable and non-consumable electrodes, each suited to specific welding processes and materials. Consumable electrodes, such as those used in Shielded Metal Arc Welding (SMAW) and Metal Inert Gas (MIG) welding, not only conduct current but also melt to contribute filler material to the joint. The selection of consumable electrodes involves considerations of material compatibility, mechanical properties, and positional capabilities.
Non-consumable electrodes, on the other hand, primarily include tungsten electrodes used in Tungsten Inert Gas (TIG) welding processes. These electrodes conduct current to the welding arc but do not melt into the weld pool. This characteristic makes them ideal for scenarios where precise, clean welds are needed, such as in aerospace or automotive applications. The effectiveness of non-consumable electrodes is amplified by their capacity to produce a stable arc, minimal spatter, and the ability to weld multiple types of metals.
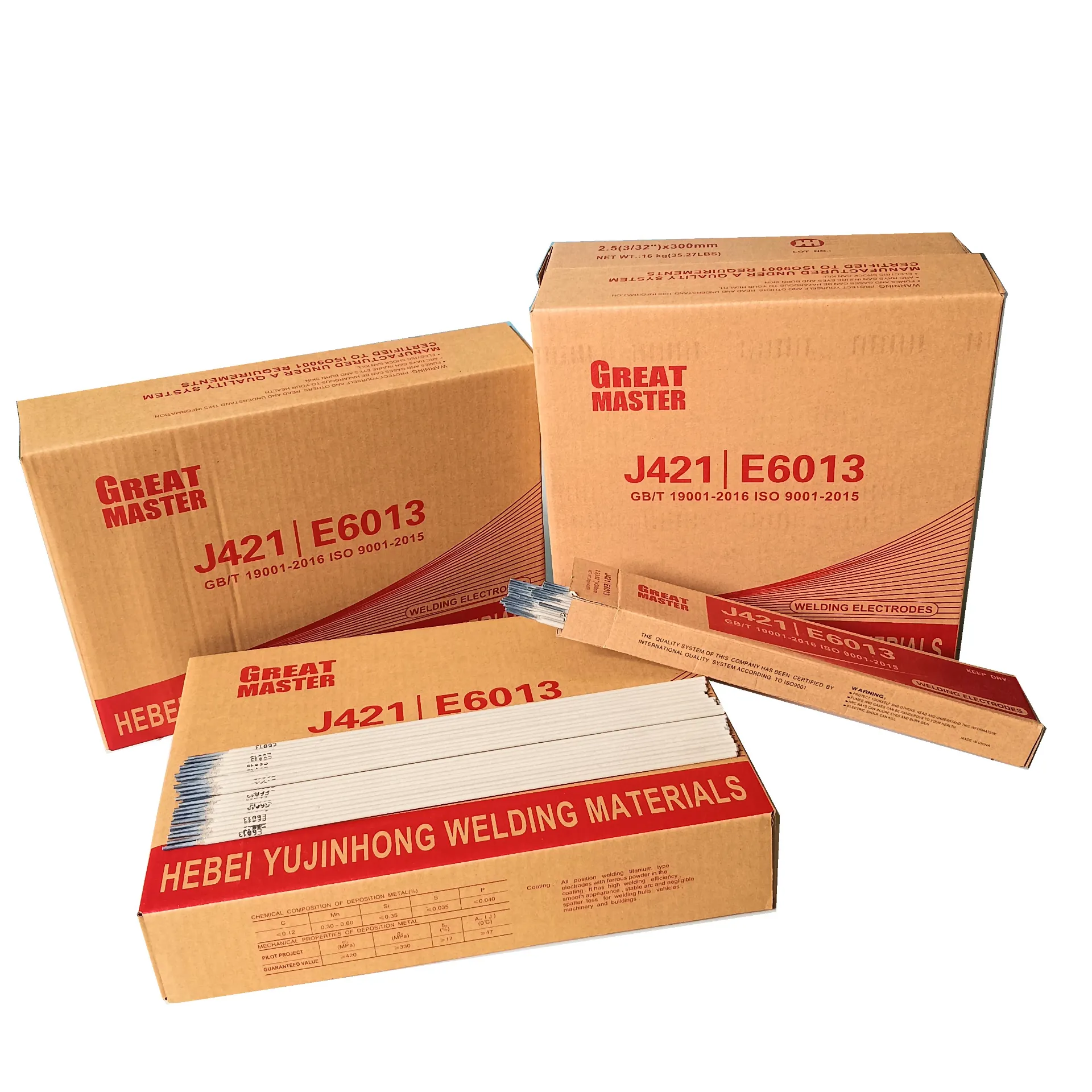
Selecting the right electrode is paramount to the success of the welding project, whether one is dealing with stainless steel, aluminum, or carbon steel, as each material demands a different approach. Factors such as electrode diameter, coating type, and current-carrying capacity play crucial roles in achieving a high-quality weld. For example, thicker electrodes are generally chosen for heavy-duty welding tasks, allowing for deep penetration and stronger joints, while thinner ones are more suitable for delicate tasks requiring precision.
electrodes welding
Coatings on electrodes are another essential consideration. They can influence arc stability, penetration depth, and ease of slag removal. For instance, cellulosic coatings, known for their deep penetration capabilities, are often preferred for vertical or overhead welding positions, whereas rutile coatings provide a smoother arc and easy slag removal, making them suitable for beginners and less experienced welders.
Moreover, the continuous advancements in electrode technology have introduced more refined options such as low-hydrogen electrodes, which significantly reduce the hydrogen content in the weld area, crucial for preventing weld metal cracking and ensuring long-term durability.
In practice, electrodes welding is augmented by the welder’s skill and understanding of the equipment. Proper electrode storage and handling also ensure that the materials maintain their integrity. Electrodes exposed to moisture can become faulty, leading to compromised weld quality and increased risk of defect formation.
Ultimately, mastery over electrodes welding requires not only knowledge of electrode selection but also a comprehensive understanding of welding dynamics and post-welding processes such as inspection and testing. As industries evolve, the need for precision and reliability in welding continues to amplify, necessitating an ever-increasing depth of expertise and craftsmanship. This intrinsic complexity underscores the importance of ongoing education and training in the field of welding, fostering innovation and upholding the standards of safety and performance.