Flux core MIG welding wire stands as a pivotal element in the realm of welding, renowned for its versatility and efficiency across various projects. A profound understanding of this wire type not only amplifies welding success but also optimizes the quality and durability of the welds produced.

Flux core MIG welding wire is prized for its ability to facilitate welding in challenging conditions and positions. Unlike other kinds of welding wire, the flux core variety does not require a shielding gas, making it especially advantageous for outdoor projects. The absence of a need for gas protection is due to the wire’s core, which contains flux compounds that, upon melting, produce a shielding gas that protects the weld pool from atmospheric contamination. This feature alone makes flux core wires a preferred option for welders dealing with windy environments or remote locations where gas cylinders are impractical.
The welding community acknowledges flux core MIG welding wire for its high deposition rates. Higher deposition rates translate to faster project completion times—an invaluable advantage in large-scale constructions where time efficiency is crucial. The ability of the flux core wire to deliver substantial weld penetration on thicker materials also renders it an essential tool in heavy machinery fabrication and repairs. For these applications, the enhanced penetration ensures stronger welds, resilient to substantial mechanical stress.
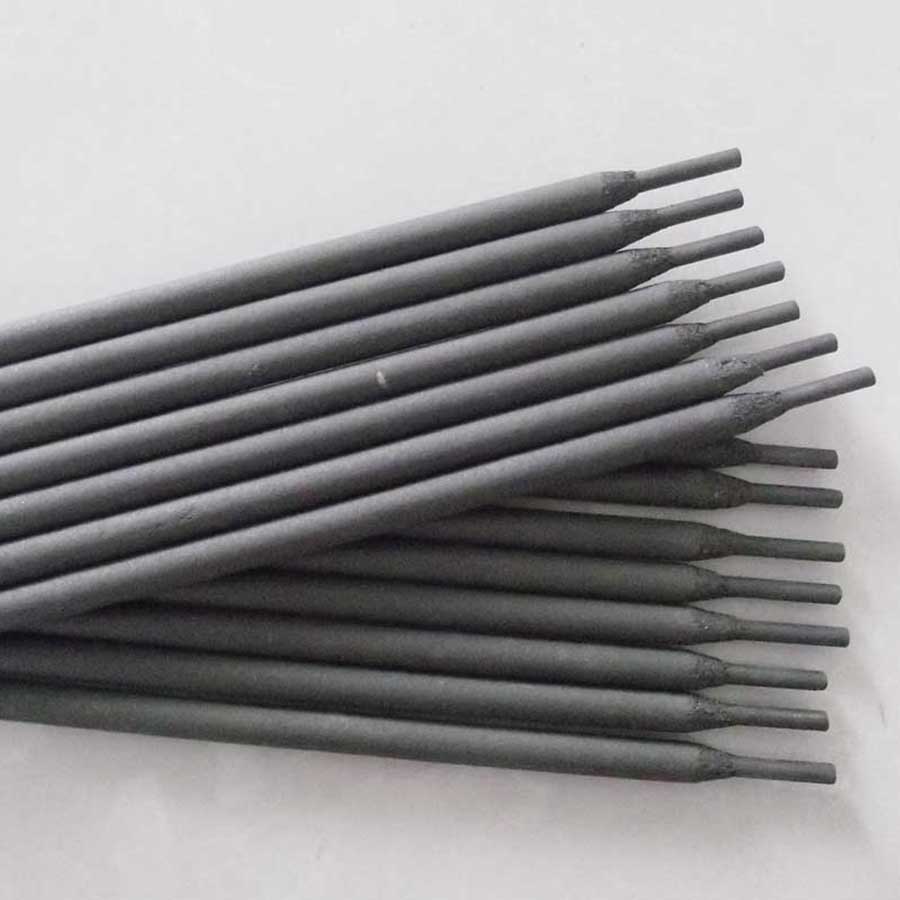
A critical aspect of using flux core MIG welding wire is selecting the appropriate wire type. The market offers a variety of wires, each designed for specific metal types and thicknesses. For example, E71T-1 is a commonly used wire, praised for its superior performance on mild steel. Understanding the specific characteristics and optimal working conditions of a given wire type is imperative. An incorrect selection can result in suboptimal welds, leading to structural weaknesses or surface imperfections.
Expertise in machine settings is equally crucial when working with flux core MIG welding wire. Properly calibrating voltage, wire feed speed, and travel speed are fundamental to achieving a sound weld. Too high a voltage can cause excessive spatter, while too low a setting might result in insufficient penetration. Similarly, mastering the correct wire feed speed helps in maintaining a stable arc, critical for consistent weld quality. Welding practitioners must invest time in fine-tuning these parameters to suit the specific wire and base material in use.
flux core mig welding wire
Another consideration is the position of welding. While flux core welding is advantageous for out-of-position welds such as vertical or overhead, it requires a refined technique to control the weld pool and minimize defects like slag inclusion or excessive spatter. Practicing and honing these skills are recommended for operators to leverage the full potential of flux core welding.
Manufacturers’ guidelines and recommendations serve as a cornerstone in the reliable application of flux core MIG welding wire. These guidelines provide insights into operating parameters, recommended base material types, and performance characteristics, ensuring weld integrity and safety. Trustworthy manufacturers will offer comprehensive datasheets and user support to ensure successful application.
Safety remains a pivotal concern in any welding operation. Though shield gas isn’t required for flux core wires, other safety measures should not be dismissed. Proper protective gear, including welding helmets, gloves, and aprons, mitigate the risks of burns and UV radiation exposure. A well-ventilated workspace is essential to prevent inhalation of fumes generated during the welding process, further safeguarding the welder’s health.
In consequence, flux core MIG welding wire represents a sophisticated tool in a welder’s arsenal, delivering unmatched flexibility and performance across various applications. Incorporating the right type of wire, adjusting settings accurately, and following safety protocols are indispensable practices in harnessing the full capabilities of this welding process. As this wire continues to evolve, staying informed about the latest developments and techniques ensures optimal results and maintains safety standards, fortifying a welder’s expertise and reputation in the field.