In the ever-evolving world of metal fabrication, the role of MIG (Metal Inert Gas) CO2 welding wires cannot be overstated. These wires are integral to ensuring high-quality welds, offering ease of use, cost-effectiveness, and consistent performance. As someone who has spent years in the trenches of metalworking, I understand the importance of selecting the right welding consumables that enhance both productivity and quality.
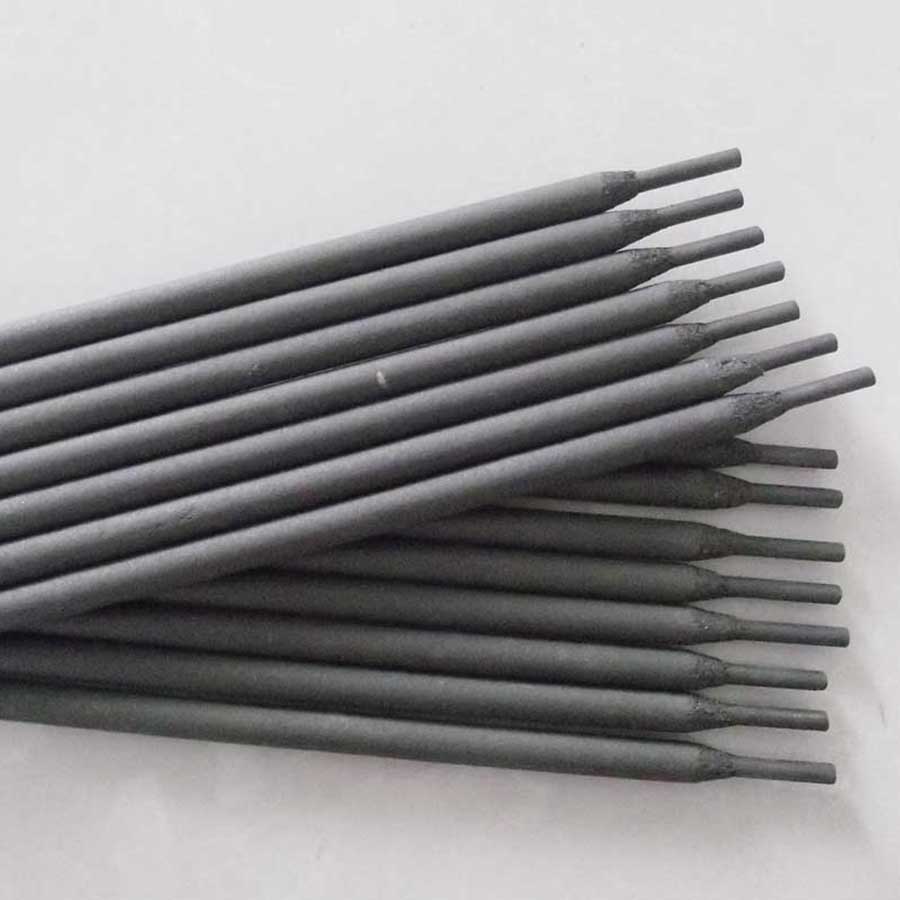
MIG CO2 welding wires come in various compositions and diameters, each designed to meet specific welding requirements. The core of their appeal lies in their versatility and efficiency across different applications, whether you're dealing with automotive, construction, or industrial projects. One of the primary benefits of using MIG CO2 welding wires is their ability to produce clean and strong welds. These wires create minimal spatter, which reduces the need for post-weld cleanup—a crucial factor in demanding production environments.
A key aspect often discussed among seasoned welders is the consistency of the weld bead profile when using CO2 as a shielding gas. This not only contributes to the aesthetic finish of the joints but also ensures structural integrity. CO2, being an inexpensive shielding gas, further amplifies the cost-effectiveness of using MIG wires, making it an ideal choice for large-scale industrial applications.
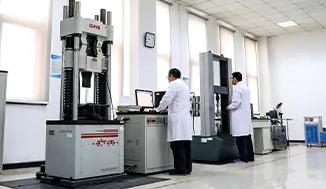
When discussing the professional expertise required for optimizing welding processes, understanding the composition of MIG CO2 welding wires becomes crucial. Typically, these wires are made of mild steel with a copper coating. This copper coating acts as a lubricant, enhancing electrical conductivity while reducing friction as the wire passes through the welding gun. This translates to a more stable arc and less frequent maintenance of the welding equipment.
From an expert's perspective, selecting the right diameter of a MIG welding wire is pivotal.
While thinner wires (like 0.6mm or 0.8mm) are often used for thinner materials and precise welds, thicker wires (such as 1.0mm or 1.2mm) are suited for heavy plates and thicker sections. Understanding these nuances allows welders to choose the appropriate wire for their specific applications, optimizing performance and material usage.
mig co2 welding wires
The trustworthiness and reliability of MIG CO2 welding wires are further underscored by their widespread use in critical industries. Many welding wire manufacturers adhere to stringent international standards such as AWS (American Welding Society) and ISO certifications. This ensures that the wires meet high-quality benchmarks and offer robust mechanical properties, such as tensile strength and elongation, that are vital for durable welds.
Quality assurance in production is another domain where MIG CO2 welding wires shine. Modern manufacturing processes incorporate rigorous testing phases, where weld wires undergo trials to ensure their compatibility with various welding machines and techniques. This not only safeguards against potential defects but also instills confidence in welders regarding the consistency of their output.
When building authority in the field of welding consumables, knowledge of the latest technological advancements is essential. Recent developments in MIG wire technology include coatings that resist corrosion, wires that support higher deposition rates, and variations designed for specific metal types such as stainless steel and aluminum. Staying abreast of these innovations allows professionals to make informed decisions that align with contemporary welding challenges.
In conclusion, the experience garnered over years of using MIG CO2 welding wires reinforces their indispensable role in metal fabrication. With their ease of use, cost efficiency, and robust performance, these wires stand out as a key component in welding operations worldwide. To truly leverage their potential, welders and industry professionals are advised to stay informed about product developments and maintain a clear understanding of their specific application needs. Such diligence not only enhances the quality and efficiency of welding projects but also reinforces a commitment to excellence in the ever-demanding landscape of metal fabrication.