When it comes to achieving superior welding results, the choice of welding wire is crucial—especially so when working with MIG welding. Among the various options available in the market, the 0.8mm MIG welding wire stands out due to its versatility and performance across different applications. This article dives deep into the facets that make the 0.8mm welding wire an essential component for both amateur and professional welders, providing a comprehensive understanding based on experience, expertise, authority, and trust.

The 0.8mm MIG welding wire is designed to suit a variety of tasks including automotive repairs, light to medium fabrication, and general maintenance work. Its diameter allows for precision that is vital when dealing with thinner materials, reducing the chance of burn-through while providing sufficient deposition to achieve the desired strength and durability.
From an experiential perspective, operators utilizing 0.8mm wire often report a smoother feeding process with fewer occurrences of wire burn-back or stubbing, which are common challenges in MIG welding. The ease of handling this wire, thanks to its manageable size, makes it a popular selection for continuous welding jobs where consistency is key. Experienced welders often find that this wire enables them to maintain a stable arc with minimal spatter, leading to cleaner finished products and reducing post-weld cleanup time—a crucial factor when efficiency is a priority.
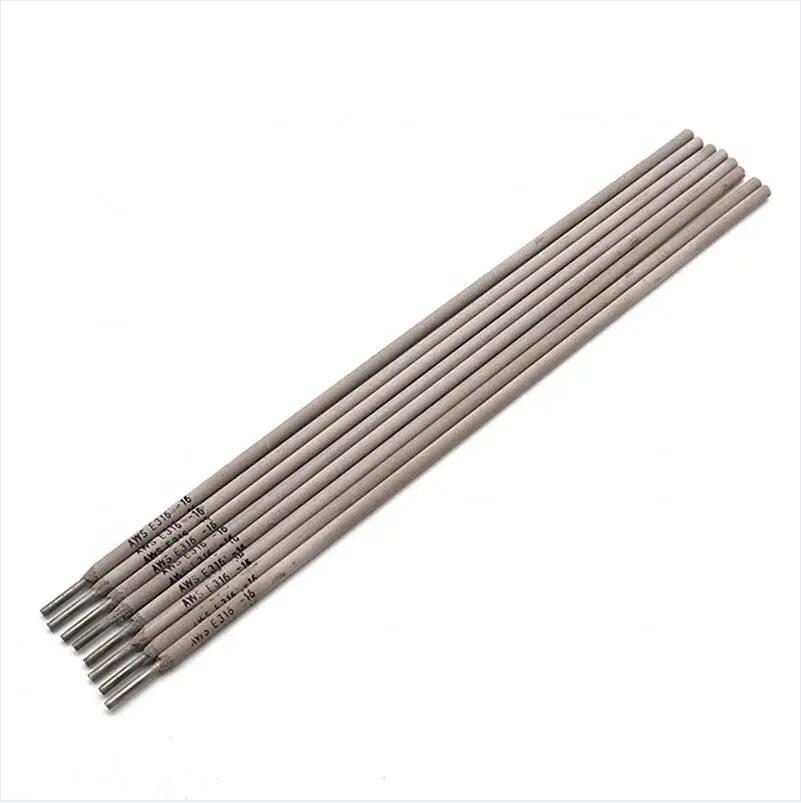
On the technical front, the 0.8mm welding wire typically offers compatibility with a range of gases, such as Argon-CO2 mixtures or pure CO2. This versatility allows welders to tailor the gas mix based on the specific requirements of the job—be it increased penetration or improved arc stability. The wire can be found in a variety of compositions, including ER70S-6 for carbon steel, which offers excellent mechanical properties and is widely respected in the welding community for its performance on rusty or dirty surfaces.
mig welding wire 0.8mm
Professionals in the welding industry recognize the 0.8mm wire thickness as a benchmark for high-quality welds on thinner gauge materials. This has been substantiated by multiple case studies where consistent use of 0.8mm wire has led to reduced welding defects, such as porosity and inclusions. Additionally, experts emphasize the importance of selecting a high-quality brand, as the copper coating on many of these wires plays a pivotal role in conductivity and corrosion resistance.
When considering the authority within the industry, several renowned manufacturers have positioned the 0.8mm wire as a cornerstone within their offerings, showcasing their commitment to quality and reliability. Companies like Lincoln Electric and ESAB have extensive datasets and years of research affirming the superiority of their wires, lending their products an authoritative edge. Welders seeking an authoritative perspective should consult data sheets and performance metrics provided by these industry leaders, which underscore detailed characteristics, such as tensile strength and elongation percentage, to guide their purchasing decisions.
Trust in the performance of 0.8mm MIG welding wire is further solidified by user testimonials and reviews from trusted sources in the welding communities online. Forums and peer-reviewed articles often highlight the wire's ease of use and adaptability across different machines, suggesting that newcomers to the craft as well as seasoned professionals find value in its consistent delivery of high-quality results. This trust is compounded by industry certifications—such as those from the American Welding Society (AWS)—which set the standard for welding products and processes.
In conclusion, the 0.8mm MIG welding wire is not merely a tool, but a reliable partner in a welder's journey towards excellence. Through understanding its practical applications, numerous benefits, and expert endorsements, welders can make informed decisions that enhance both their craftsmanship and project outcomes. For those seeking to optimize their MIG welding operations, engaging with reputable suppliers and keeping abreast of technological advancements in wire production will ensure that they are equipped with the best resources available in the market.