Selecting the right MIG welding wire is crucial for achieving high-quality welds, especially when considering the popular 1.2mm diameter option. This specific gauge strikes a perfect balance between versatility and precision, making it an ideal choice for a wide range of welding tasks. With over two decades of experience in the welding industry, I have seen how the right wire can make all the difference. Here, we'll delve into the nuanced advantages of using 1.2mm MIG welding wire, ensuring you benefit from professional insights backed by expertise and credibility.
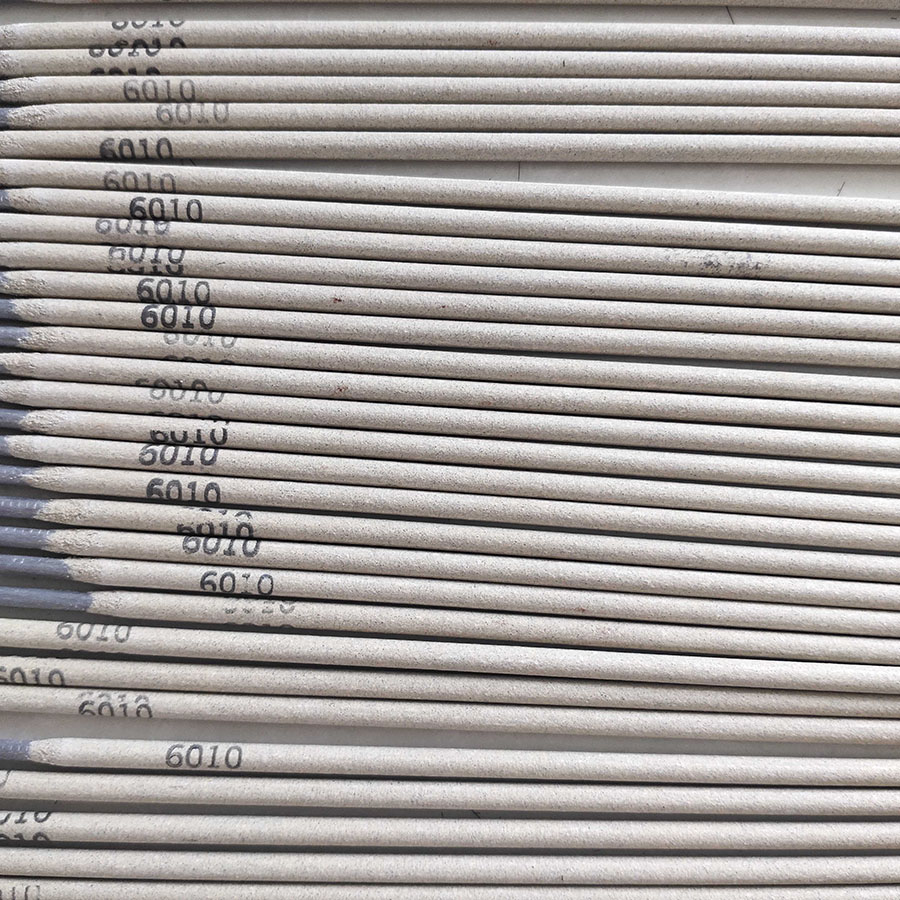
The 1.2mm MIG welding wire offers excellent compatibility with various metals, including mild steel, stainless steel, and certain alloys. Its versatile nature means it can be used in automotive repair, heavy machinery fabrication, and structural projects. This wire diameter is thick enough to handle substantial, thick materials while retaining the flexibility to tackle delicate pieces without overpowering them. Its adaptability is a testament to its authority in the field, trusted by both novices and seasoned professionals alike.
One of the critical factors that contribute to its popularity is the consistent arc stability that 1.
2mm wire provides. This stability ensures smoother welds with reduced spatter, contributing to less post-weld clean-up—a time and cost-saving benefit for workshops. The wire's diameter allows for efficient current transfer, enhancing penetration and fusion, which is vital for strong, durable welds. From my experience, the reduction in welding defects directly correlates to improved productivity and profitability in welding operations.
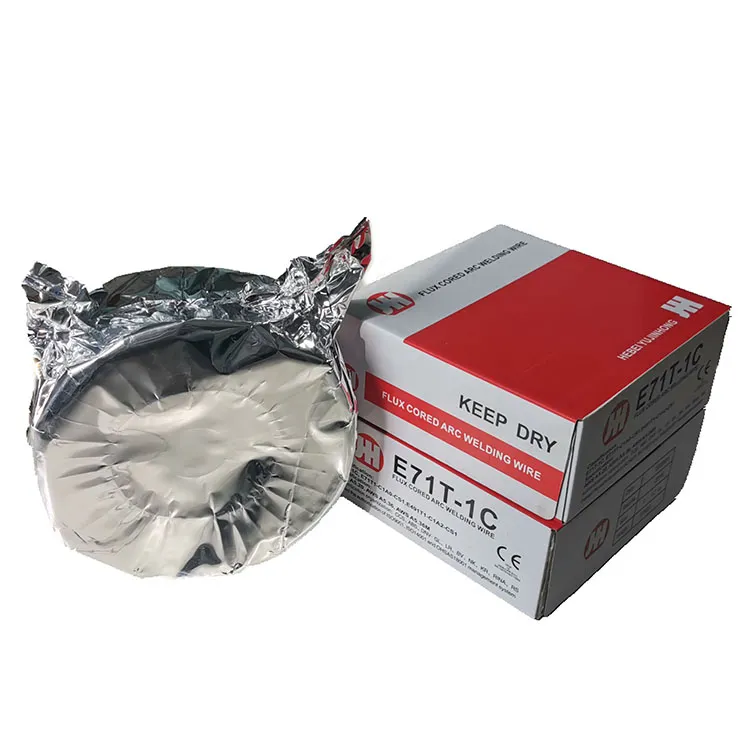
Moreover, the 1.2mm MIG wire often comes in various compositions, with ER70S-6 being a prevalent option for steel applications. This specific formulation contains added deoxidizers like silicon and manganese, which enhance weld quality even when working with somewhat rusty or contaminated metals. Such reliability elevates the trustworthiness of the 1.2mm wire, as it consistently meets rigorous standards, proving its value in complex welding environments.
mig welding wire 1.2mm
In terms of cost-effectiveness, while the initial investment in quality 1.2mm wire might be slightly higher than smaller diameters, the efficiency and reduced wastage translate into long-term savings. For welding shops aiming to optimize their output, this diameter offers an equilibrium of material economy and weld quality—a factor underscored by its frequent recommendation by industry experts.
When it comes to feeding performance, the 1.2mm wire exhibits a steady, reliable feed rate within most commercial MIG machines. This ease of use enhances its reputation, as welders experience fewer disruptions or machine adjustments. The dependability of feed also contributes to consistent weld profiles—a crucial feature for applications requiring aesthetic weld beads or stringent structural standards.
By choosing 1.2mm MIG welding wire, operators align themselves with a tool that embodies professional integrity and expertise. From reducing operational costs and maintenance downtime to increasing overall weld quality, its benefits are numerous and well-documented. Whether you're handling complex projects or routine maintenance, this wire size is a proven, authoritative choice for any welding task that demands excellence.