Flux-cored welding wire has revolutionized the welding industry, offering a unique combination of efficiency, performance, and versatility. This product category, known for its distinctive tubular design filled with flux, provides several benefits over traditional solid welding wires, particularly in challenging welding environments.
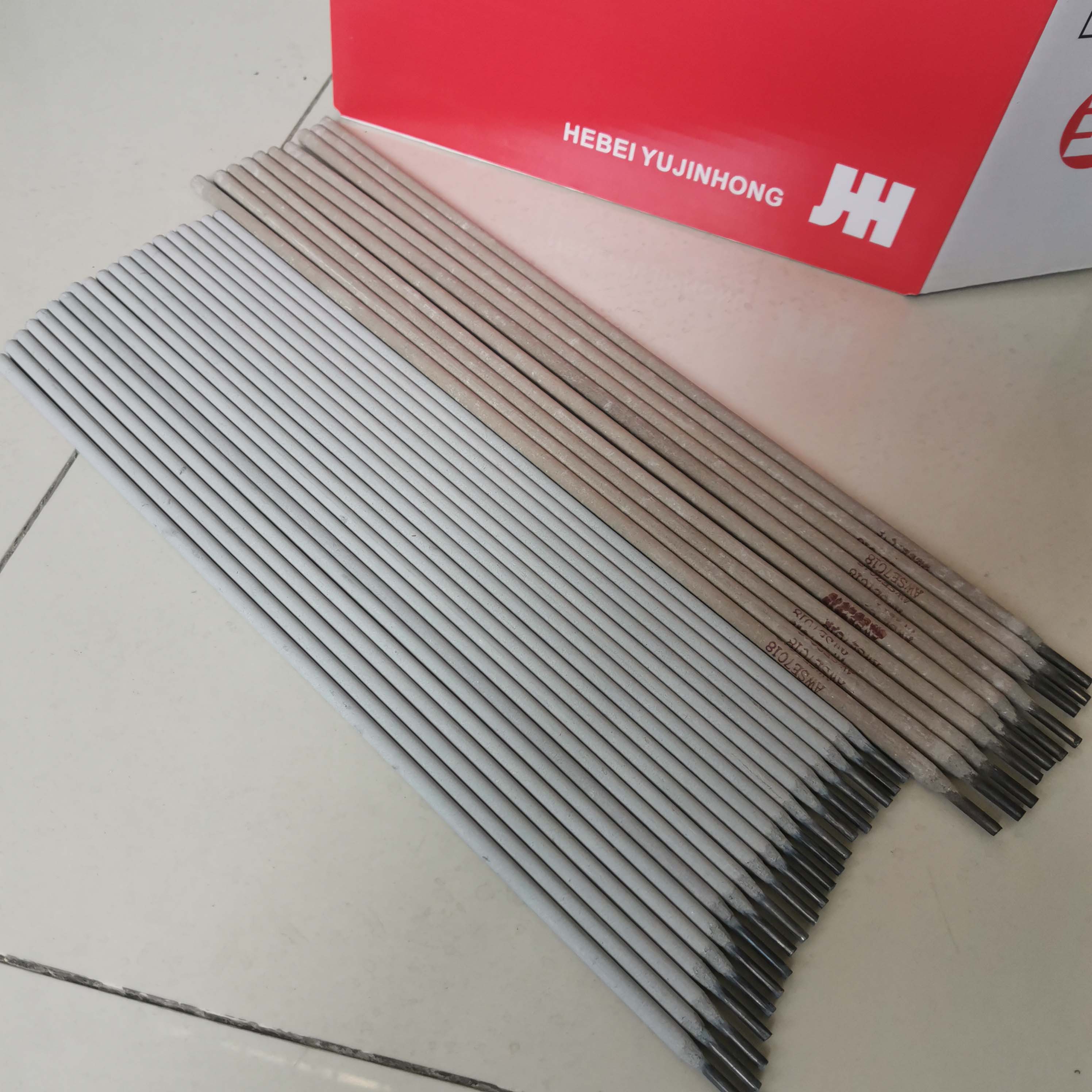
Expert welders often choose flux-cored welding wire for its ability to produce strong, high-quality welds in diverse situations. One of the most notable features is its capacity to work effectively even in windy conditions, a scenario where gas-shielded wire might fail due to shielding gas being blown away. With flux-cored wire, the arc stabilizes through the flux that forms a protective gas shield when heated, ensuring consistent and reliable welds.
Furthermore, flux-cored welding wire excels in different material thicknesses, from thin sheets to heavier structures, without compromising the integrity of the weld. This makes it an adaptable choice for a variety of industries, including shipbuilding, construction, pipeline welding, and heavy equipment repair. Its versatility extends beyond industrial applications, becoming a staple in hobbyist garages and small-scale repair shops as well.
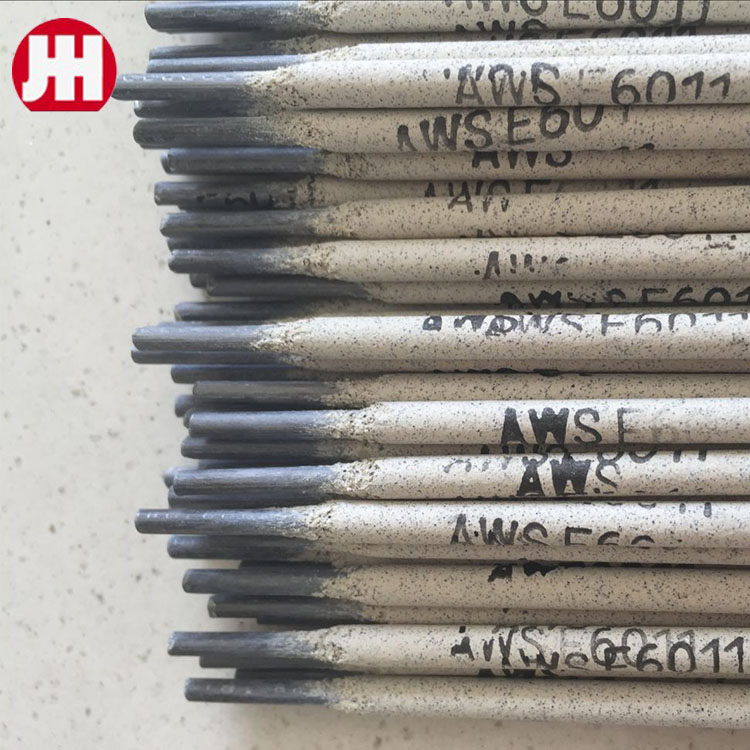
The expertise embedded in the design of flux-cored welding wires accounts for its increased deposition rates, allowing for faster welding speeds and higher productivity. This efficiency is further bolstered by its reduced cleanup needs; the slag produced during welding is typically easier to remove compared to other methods, saving precious time in post-weld processing.
Selecting the right flux-cored welding wire involves understanding the specific needs of the task at hand. It requires a comprehensive evaluation of factors such as the base materials involved, the required mechanical properties of the welds, the welding position, and environmental conditions. Experienced welders emphasize testing different types of flux-cored wires to match the unique demands of each project.
flux-cored welding wire
The authority of choosing flux-cored welding wire often comes with considering the brand's reputation and the product's technical specifications. Leading manufacturers provide detailed specifications and recommendations, backed by rigorous testing and quality assurance processes, to guide users in selecting the most suitable wire for their projects. Reviews from industry professionals and credible welding forums also shed light on the real-world performance and reliability of various flux-cored wire options.
In building trust, manufacturers typically highlight the consistency in manufacturing processes and the use of high-quality materials in producing flux-cored wires. This reliability is critical for maintaining safety standards, especially in projects where any compromise in welding quality could lead to significant consequences.
Personal experience with specific flux-cored welding wires is invaluable and often shared among professional circles to provide insights into the product's performance in specific conditions. Such exchanges of information between seasoned welders form a trusted basis for making informed purchasing decisions, further solidifying the reputation of this welding wire category.
In conclusion, flux-cored welding wire continues to be a central tool in the welding industry due to its efficiency, adaptability, and superior performance in varied conditions. The combination of experience, expertise, authoritative guidance, and trusted feedback ensures that welders can maximize the advantages of this technology to deliver outstanding results in their projects.