Navigating the nuances of AC welding rods can often feel like venturing into a realm where precision and knowledge meet. The art of welding, especially with AC welding rods, is not just about joining metals but about creating bonds that withstand the test of time and the harshest of conditions. For those who have experienced the efficiency of the correct welding rods, it’s a symphony of sparks, heat, and strength, making a crucial difference in the structural integrity of projects.
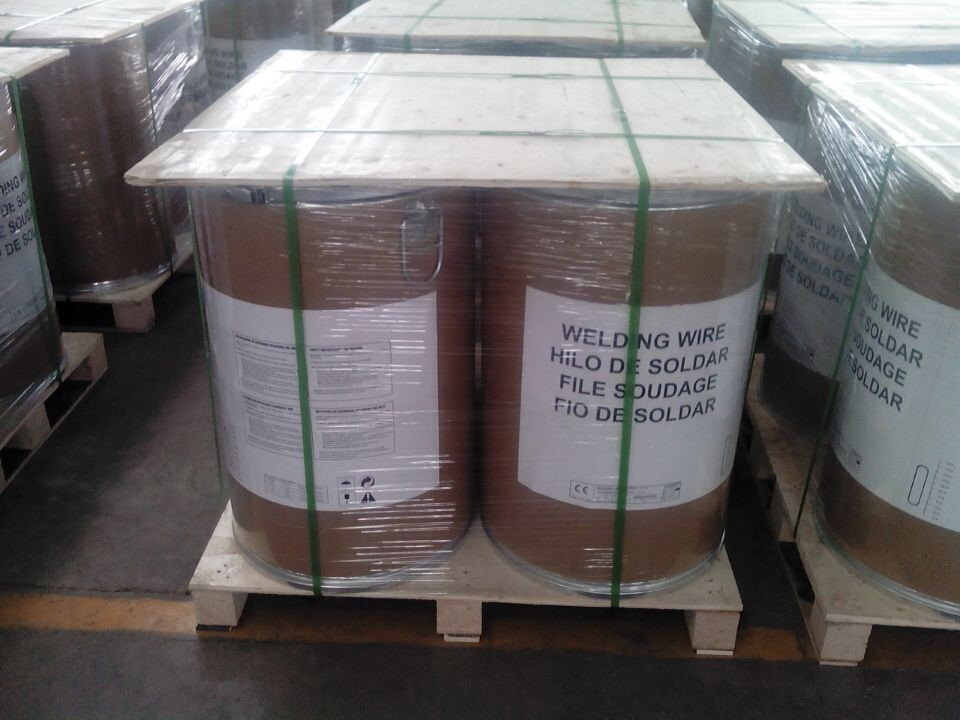
AC welding rods, according to seasoned welders, are indispensable tools for various welding projects, especially those involving aluminum and magnesium alloys. Unlike other rods, AC rods are optimized for alternating current, providing a steadier arc and subsequently higher penetration. This fusion of technology and metallurgy caters to a spectrum of applications, from domestic repairs to large-scale industrial tasks.
From a technical standpoint, AC welding rods are designed to handle the fluctuating currents of AC welding machines. This unique characteristic is vital in reducing the risk of arc blow, a common welding challenge where the magnetic field affects the arc path. Arc blow can result in a weak, unpredictable weld, but the design of AC rods ensures greater stability. This makes them especially suitable for welding ferromagnetic materials, where magnetic interference is often a concern.
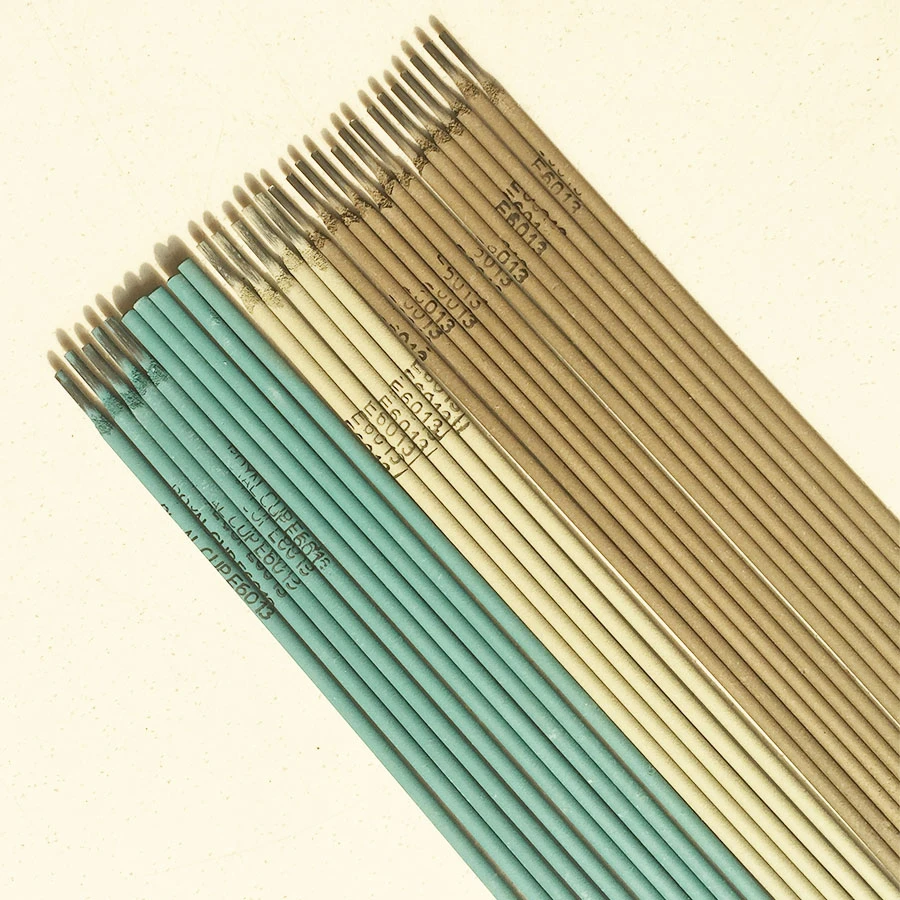
Differentiating AC welding rods from their DC counterparts involves examining the coating and core material composition. AC rods are typically imbued with materials such as titanium which helps in stabilizing the arc and reducing spatter. Their composition is aimed at making them versatile across a range of metals and conditions. This versatility makes them a staple in repair jobs where different alloys might be encountered.
In the realm of customer experience, feedback from experts who regularly use AC welding rods suggests an experience characterized by ease of use and adaptability. For instance, when used on aluminum, welders note fewer occurrences of arc starting issues and an overall smoother bead profile. The input from the welding community underscores the reliability factor that these rods offer, reinforcing their popularity among both novices and seasoned professionals.
ac welding rod
Trustworthiness of AC welding rods is also underscored by industry standards and certifications, which ensure these products meet rigorous quality controls. Brands that adhere to these standards often provide consistent performance, reducing the need for extensive post-weld cleaning or finishing. This not only saves time but also resources, emphasizing a cost-effective approach in both small-scale and large-scale applications.
Authoritative voices in the welding industry, such as welding instructors and engineers, recommend thorough compatibility checks before selecting AC welding rods for a task. Factors like the type of metal, thickness,
and the welding position should be duly considered. It’s this degree of professionalism in selecting and handling the rods that results in optimal outcomes, whether it’s a hobbyist working from a home garage or a large company handling infrastructure projects.
Indeed, expertise in using AC welding rods is honed through practice and continual learning. Staying updated with the latest advancements in welding technology, such as improvements in rod coatings and their specific applications, can significantly enhance the quality of one’s workmanship. Engaging with professional welding communities, attending workshops, and even enrolling in certification programs bolster both understanding and proficiency in welding with AC rods.
For the discerning buyer or user, understanding the product specifics is crucial. Factors such as storage conditions—the low humidity and adequate temperature control necessary to preserve the quality of the rods—play a significant role. Understanding these aspects adds another layer of reliability and longevity to the welding process.
In summary, AC welding rods are quintessential in facilitating robust and reliable welds under alternative current circumstances. The combination of expertise in their application, trustworthiness through quality assurance, authoritative recommendations from professionals, and real-world experience feedback create a compelling case for their use. Embracing these elements not only enhances the quality of welding endeavors but ensures the lasting durability and strength of the bond formed.