Stainless steel welding wire with a diameter of 1.6 mm is an essential material for many welding applications, offering unmatched versatility and efficiency. When welding stainless steel structures, choosing the right welding wire is critical to ensure durability, strength, and resistance to environmental factors. As a seasoned expert in welding technologies, the insights and information shared here aim to guide professionals in maximizing the benefits of this specific wire while ensuring adherence to best practices.
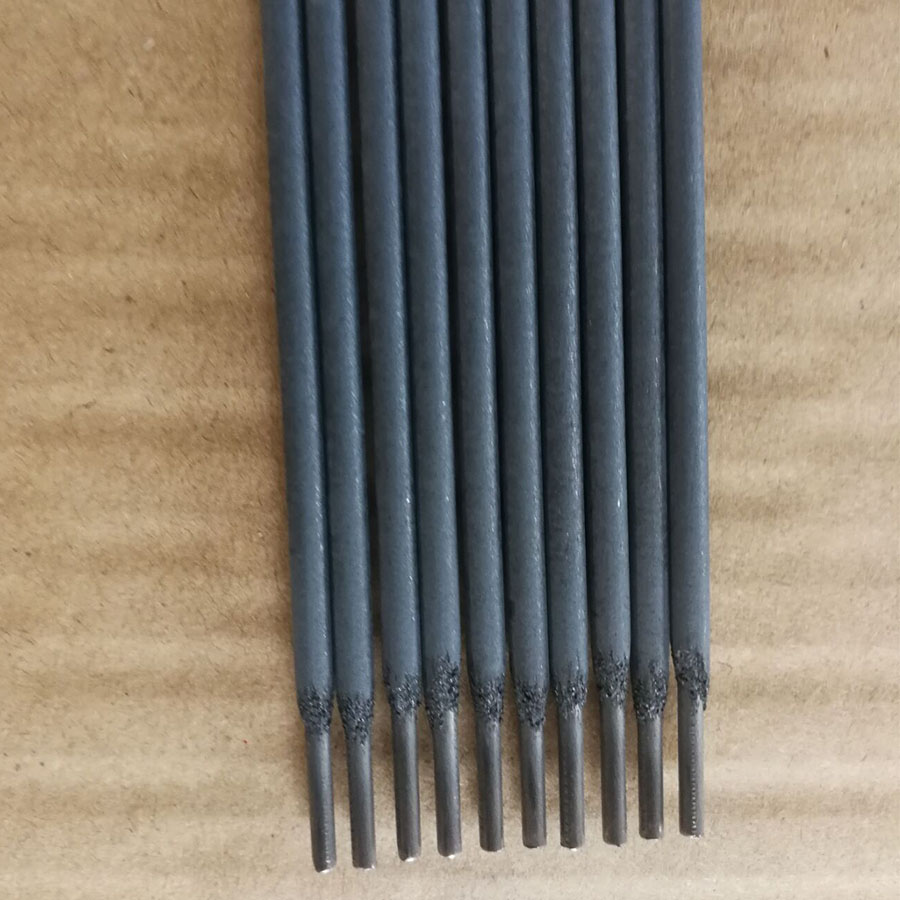
Professionals select 1.6 mm stainless steel welding wire because of its balance between strength and flexibility, making it suitable for intricate welding projects that require precision without compromising structural integrity. This diameter is ideal for automotive, architectural, and industrial applications where high performance is necessary.
In terms of expertise, utilizing 1.6 mm stainless steel welding wire demands a thorough understanding of the welding process and the properties of the metals involved. The wire's composition usually includes chromium, nickel, and molybdenum, which contribute to its corrosion-resistant properties. These elements ensure the welded joints can withstand exposure to moisture and harsh environmental conditions, which is crucial for outdoor and marine applications.
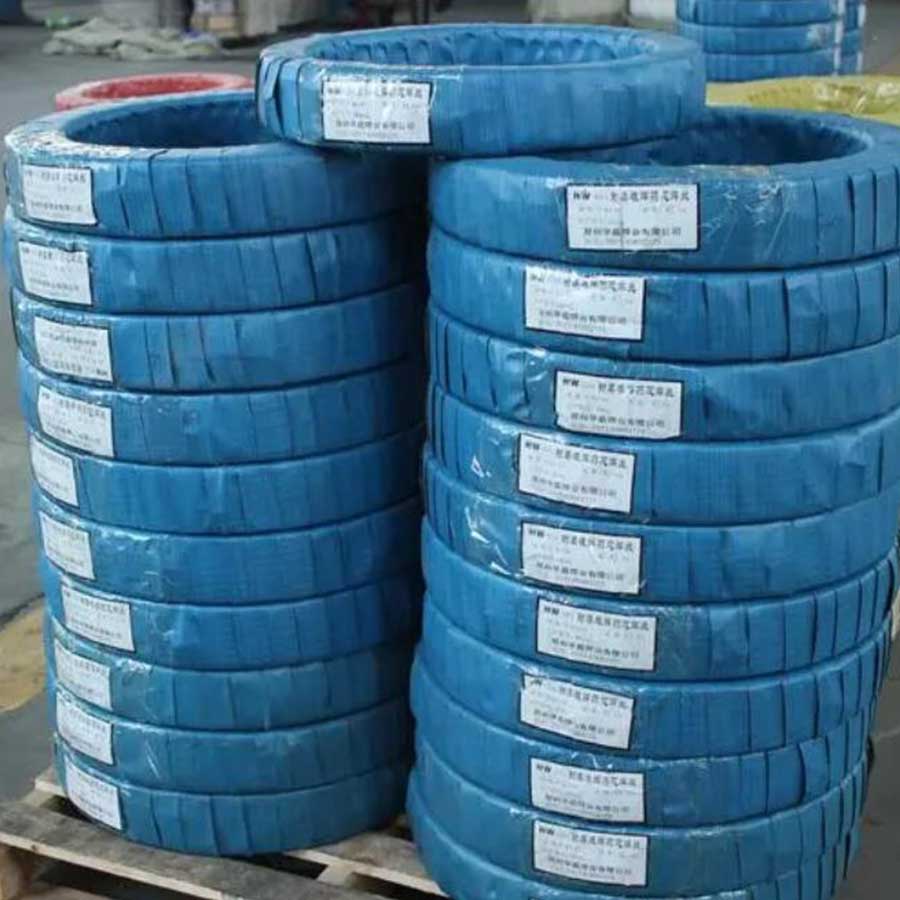
Authoritativeness in using 1.6 mm stainless steel welding wire stems from knowledge of its applications in various industries. For instance, in the food and beverage industry, stainless steel is the preferred material due to its cleanliness and resistance to oxidation. Welding with this wire ensures the preservation of these properties at the joints, maintaining the overall hygiene and compliance with industry standards. This knowledge empowers businesses to meet regulatory requirements while optimizing the longevity and safety of their products.
Trustworthiness in handling and applying stainless steel welding wire aligns closely with adherence to standards and using certified materials. When sourcing welding wire, it's imperative to verify its certification for industry-specific applications. Certified wires guarantee that the composition and performance meet the necessary criteria, reducing the risk of joint failure or material degradation over time. Reliable suppliers provide documentation and compliance details, which are critical for maintaining trust in the quality of the finished welded product.
stainless steel welding wire 1.6 mm
Experience and expertise go hand in hand when handling stainless steel welding wire of any diameter, particularly 1.6 mm. Welding professionals underline the importance of proper machine calibration, as incorrect settings can impair the welding process and the structural integrity of the weld. Ensuring the welding equipment is correctly configured for stainless steel prevents inconsistencies and enhances productivity by reducing the likelihood of rework.
Moreover, using 1.6 mm stainless steel welding wire effectively involves a solid grasp of pre-weld and post-weld processes. Proper cleaning of components before welding reduces contamination and ensures high-quality welds, while post-weld treatments like passivation remove iron particles from the surface, reinstating corrosion resistance and enhancing the appearance of the weld.
Professionals acknowledge that hands-on experience with stainless steel welding wire can vastly improve the outcomes of welding projects. Hands-on training and ongoing education contribute to a deeper understanding of how the wire interacts with different metals and welding machines, elevating the skill level over time.
In conclusion, the strategic use of 1.6 mm stainless steel welding wire requires a combination of technical knowledge, practical experience, and a commitment to quality standards. As you continue to explore the capabilities of this material, prioritizing expertise and adherence to industry best practices will ensure successful projects and solidify your reputation for delivering reliable, high-quality welds across various applications.