The world of welding can be intricate, yet it's a critical aspect of many industries, whether in construction, automotive, or even the arts. Among the essential tools in a welder's arsenal are high-quality welding electrodes, and the 6013 welding electrodes have long been a staple for professionals and hobbyists alike. Understanding the characteristics of these electrodes, their benefits, and their usage scenarios can significantly enhance one's welding projects and ensure superior results.
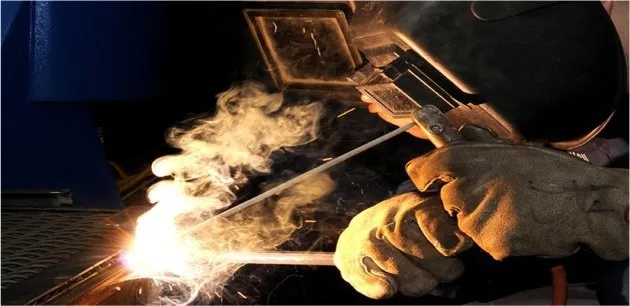
6013 welding electrodes are particularly favored for their ease of use and versatility. Designed for general-purpose welding, the 6013 electrodes are suitable for a variety of metals and positions, including flat, horizontal, vertical, and overhead positions. This flexibility makes them an indispensable choice for both beginners and seasoned welders who need reliable performance across different welding scenarios.
One of the primary attributes of the 6013 electrodes is their rutile-based flux coating, which facilitates smooth arc action and ease of slag removal. Rutile coatings are known for producing a stable arc and a visually appealing bead, which is fundamental for projects where aesthetics are as important as functionality. The slag layer produced by the 6013 electrodes peels away effortlessly after welding, which saves time and enhances productivity on the job site.
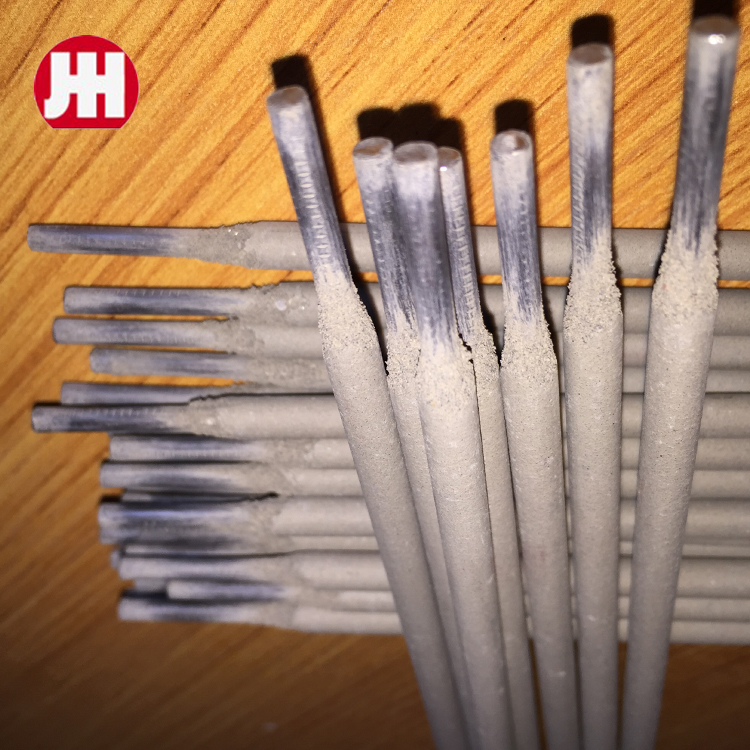
Additionally, the 6013 electrodes are known for their ability to produce soft arc characteristics, contributing to minimal spatter. This means less post-weld cleaning and finishing, which can be crucial for maintaining tight project timelines and ensuring cost-effectiveness. They also provide good weld penetration, which is essential for achieving strong, durable joints, particularly in mild steel applications.
Professional welders often appreciate the 6013 electrodes' consistent performance and reliability. Their forgiving nature makes them an excellent choice for welding thinner materials, often used in sheet metal work, vehicle bodies, and fabrication tasks where precision is key. Moreover, their capacity to perform at lower amperage settings enables greater control during the welding process, which is invaluable for achieving accurate and high-quality welds.
6013 welding electrodes
In terms of expertise, choosing the 6013 welding electrodes can significantly impact your project's success. These electrodes work efficiently with both AC and DC power sources, expanding their utility across different welding setups. Focus on matching electrode size to the metal thickness for optimal results. For instance, using a 1/8 inch rod for 1/8 inch metal ensures sufficient penetration and strong results without excessive bead size.
Authority in welding stems from the products and techniques used. For those seeking to build a reputation for excellence, the consistent results delivered by 6013 welding electrodes cannot be underestimated. They are a testament to a welder's commitment to quality and technical precision, a crucial component in establishing credibility and trust with clients.
From a trustworthiness standpoint, 6013 welding electrodes are a reliable choice endorsed by experienced welders and industry standards. Their proven track record of performance in various conditions makes them a go-to solution for a wide range of welding tasks. Using these electrodes means relying on a product that has been developed and refined through extensive research and field-testing, a crucial point for ensuring safety and quality in every weld.
In summary, the 6013 welding electrodes offer a combination of user-friendly features, versatile application, and robust performance that satisfies both novice and expert welders. Their ability to adapt to various welding conditions and their contribution to achieving strong, clean welds make them an irreplaceable component in the welding industry. By choosing 6013 electrodes, welders enhance their craftsmanship's quality, demonstrating a dedication to excellence and trustworthiness in their work.