Choosing the optimal CO2 MIG welding wire can significantly impact the efficiency and quality of your welding projects. As a seasoned professional in the welding industry, I've navigated the complexities of welding wire selection, and I understand the importance of aligning the right product with specific project demands.
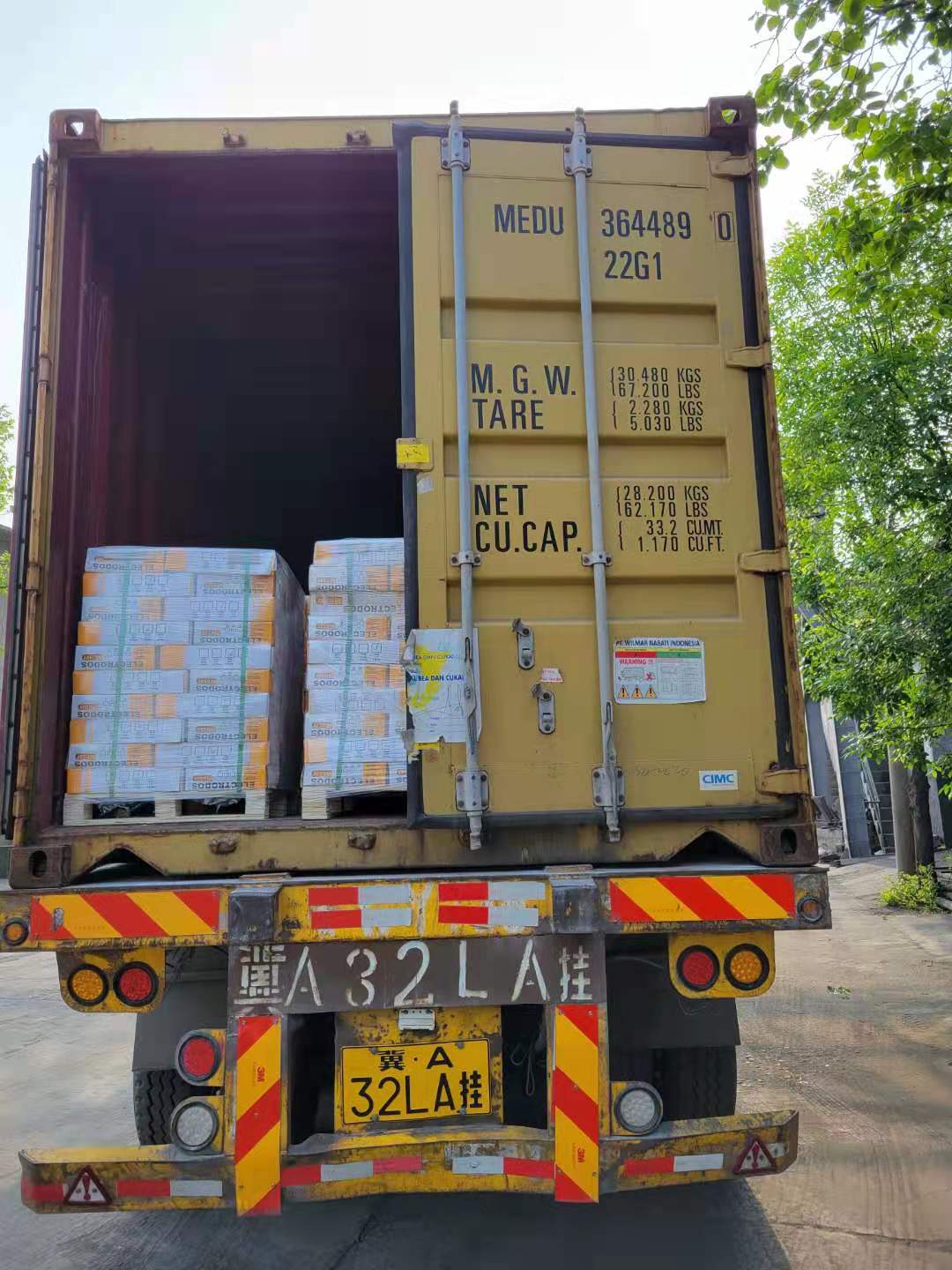
Understanding the significance of CO2 MIG welding wire begins with recognizing its role in the Gas Metal Arc Welding (GMAW) process. This type of welding wire is specifically designed to be used with a shielding gas, typically a mixture of carbon dioxide, to protect the weld from contaminants in the air. This enhances the weld quality, ensuring a strong and durable bond.
In my years of experience, I've worked with various types of welding wire, and CO2 MIG wire stands out for its versatility and efficiency. Its composition, often a mild steel base with added elements like manganese and silicon, is designed to improve weldability and mechanical properties. This composition not only aids in achieving smoother welds but also enhances the wire's ability to handle variations in welding positions and parameters.
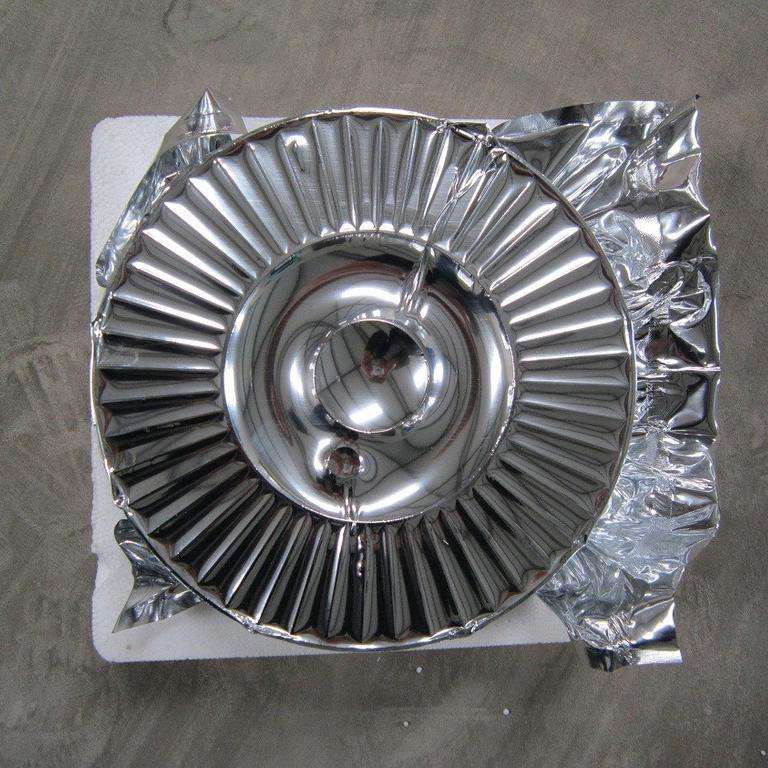
The benefits of using CO2 MIG welding wire are manifold. It allows for high-speed welding, which in turn increases productivity. This makes it an ideal choice for industries where time is of the essence, such as automotive manufacturing or construction. The wire's ability to provide deep penetration and excellent fusion with base metals ensures that even thicker materials can be welded effectively.
Selecting the right grade and diameter is crucial. The wire's diameter can influence the welding current range and deposition rate, affecting the overall heat input and potential for warping or distortion. Experienced welders will recognize the necessity of matching the wire diameter with the material's thickness and the desired penetration depth.
co2 mig welding wire
Another key aspect of CO2 MIG welding wire is its feedability. Properly managing wire feed speed and ensuring consistent delivery is essential to prevent issues like burn-back or bird-nesting. Innovations in wire design, such as improved surface coating and lubrication, have considerably enhanced feeding performance, reducing downtime and maintenance needs.
In terms of expertise, using CO2 MIG welding wire requires a strong understanding of the relationship between wire properties and welding settings. Successful welders continuously adapt their techniques to the specific wire being used, which often involves adjusting welding speed, voltage, and gas flow to optimize performance. This adaptability is honed through extensive experience and a deep understanding of material science.
Industry authority underscores the notion that a high-quality CO2 MIG wire should conform to established standards, such as the American Welding Society (AWS) specifications. Certification from reputable organizations reflects adherence to stringent quality and safety guidelines, ensuring reliable performance in critical applications.
Trust in CO2 MIG welding wire also stems from its consistent delivery of results across various projects. Feedback from welders and manufacturing professionals plays a substantial role in determining product reliability. A wire's reputation, bolstered by positive evaluations and case studies, can greatly influence purchasing decisions, serving as a testament to its efficacy.
Overall, CO2 MIG welding wire remains an indispensable component in the arsenal of a skilled welder. By aligning the right wire with project requirements, welding professionals can achieve unmatched precision and efficiency. Every project is an opportunity to leverage industry expertise, ensuring that the chosen welding wire maximizes performance while maintaining rigorous standards of quality and safety.