Mastering the nuances of MIG welding can be a transformative experience for both hobbyists and professionals. The pivotal role of MIG wire SS, or stainless steel MIG wire, in this process cannot be overstated. Understanding its properties and application techniques is critical for achieving high-quality welds that stand the test of time.
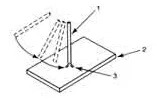
MIG wire SS, typically crafted from durable stainless steel alloys, is designed to resist oxidation and corrosion, making it an ideal choice for projects exposed to harsh environments. This wire’s unique formulation ensures that it provides a superior metallic sheen and robustness, critical for both structural integrity and aesthetic appeal.
One of the fundamental experiences of utilizing MIG wire SS involves selecting the correct diameter and alloy composition. A common choice is 308L, which is versatile and provides optimal results in a range of applications from household repairs to industrial uses. The wire’s thickness needs to align with the workpiece; too thin might lead to burn-through, while too thick may result in an unstable arc.
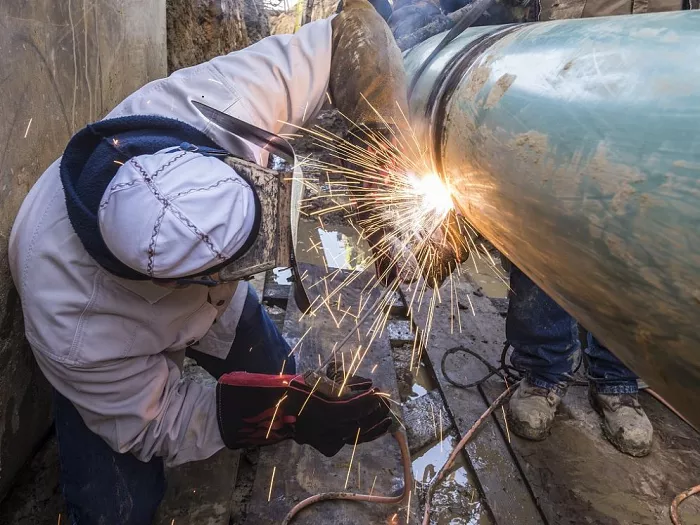
Professional welders emphasize the importance of setting up the MIG welder accurately. This involves adjusting the voltage and wire feed speed to match the type of wire and the thickness of the material. A balanced setup ensures a smooth arc and minimizes the risk of warping or welding defects. The selection of shielding gas is also crucial. A blend of argon and carbon dioxide is often favored for its ability to deliver cleaner and more stable arcs, crucial for stainless steel.
mig wire ss
Expertise in welding is further refined by managing the technique. The push or forehand technique, where the welder pushes the torch away from the weld puddle, is often recommended for MIG wire SS. This technique facilitates better gas coverage, ensuring the integrity of the weld, and minimizes spatter, a common challenge when dealing with stainless steel.
Authoritativeness in stainless steel MIG welding is built through rigorous training and a deep understanding of the metallurgy involved. Professionals often refer to established welding standards set by organizations like the American Welding Society (AWS), which offer guidelines on the appropriate wire types and parameters for different applications.
Trustworthiness in executing a flawless weld with MIG wire SS lies in the meticulous preparation of the workpieces. Ensuring a clean surface free of contaminants such as oil or rust is essential. Using stainless steel brushes and cleaning agents designed for stainless steel helps in maintaining the workpiece's integrity. Additionally, practicing on scrap pieces can help in fine-tuning the welder settings and perfecting the technique without compromising the actual workpiece.
In conclusion, the utilization of MIG wire SS is not merely about choosing a product but involves a comprehensive understanding of welding dynamics. Success hinges on selecting the appropriate wire type, precisely setting up the welding equipment, and employing suitable techniques. By doing so, welders can ensure their projects boast both structural reliability and aesthetic excellence, standing as a testament to their craft and skill.