Stainless steel is a foundational material in numerous industries, and choosing the right MIG wire is essential for any welding project. The 1.2mm stainless MIG wire has emerged as a popular choice for professionals who require precision, reliability, and high performance. Its popularity stems from several key factors that enhance its suitability for a wide range of applications, from construction to automotive manufacturing.
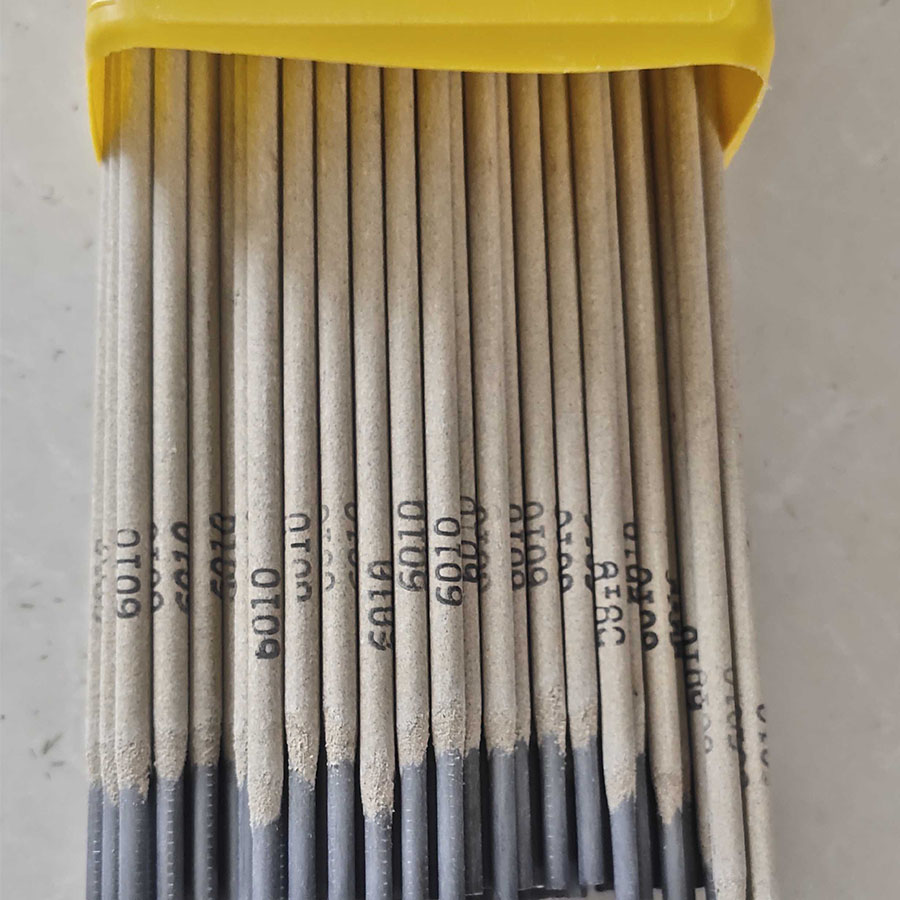
One of the foremost advantages of 1.2mm stainless MIG wire is its versatility. This particular diameter strikes a balance between strength and adaptability, making it suitable for both thicker and medium-gauge materials. Its use reduces the need for multiple wire types on-site, streamlining operations. Welders appreciate how this wire maintains high tensile strength while allowing greater flexibility in application, which is critically important when dealing with dynamic or structurally demanding projects.
From an expert perspective, the composition of stainless MIG wire significantly impacts its performance. High-quality 1.2mm wires often consist of alloys such as 308LSi, 316LSi, and 309LSi. These variants are engineered to provide enhanced arc stability, reduced spatter, and improved corrosion resistance. For applications exposed to harsh environments, such as marine or chemical exposure, 316LSi is often recommended due to its superior resistance to corrosion and oxidation. Thus, the selection of the right alloy composition is crucial and depends largely on the operational environment and material specifics.
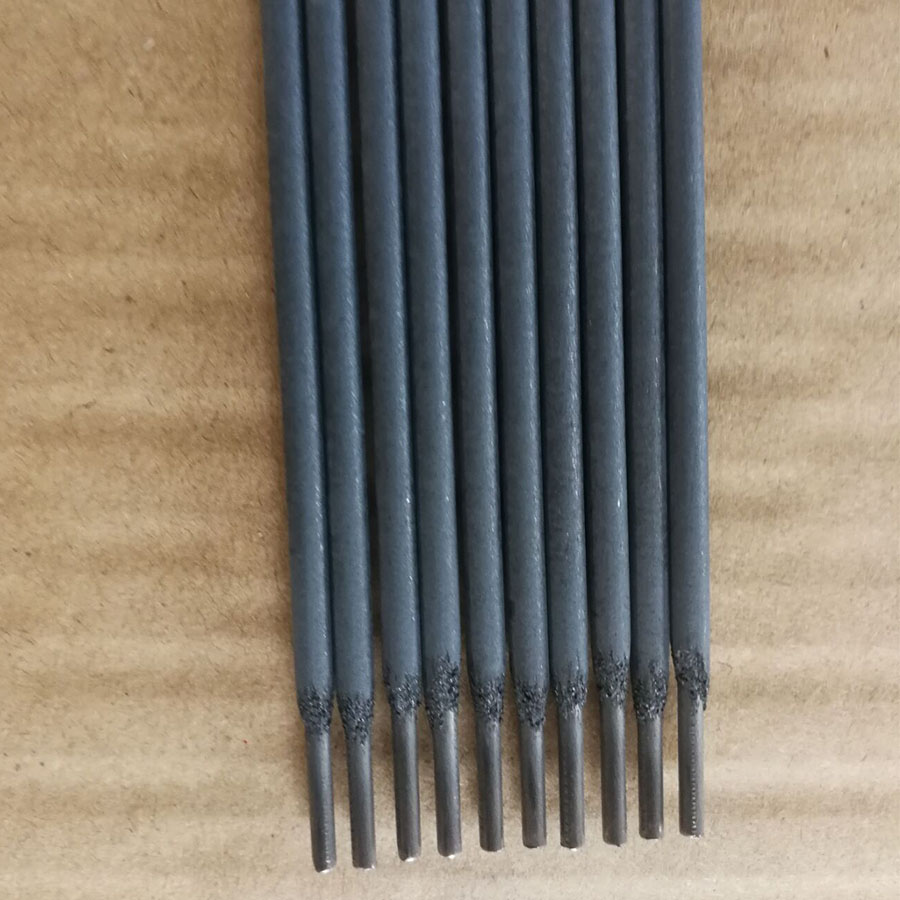
Reliability and ease of use further bolster the trustworthiness of 1.
2mm stainless MIG wire. Welders consistently report cleaner welds with minimal post-weld cleanup, thanks to the precision of this wire. This efficiency contributes to cost savings over time, reducing the need for extensive grinding and polishing. Novice welders and seasoned professionals alike benefit from wires designed to enhance bead appearance and reduce the likelihood of defects such as porosity and incomplete fusion.
stainless mig wire 1.2mm
In terms of authoritativeness, leading manufacturers subject these wires to rigorous testing under varied stress conditions to ensure compliance with industry standards. The reputation of manufacturers plays a significant role in ensuring product quality. Renowned producers like ESAB, Lincoln Electric, and Kobelco are known for their stringent quality assurance practices, ensuring that each spool delivers consistent performance. Their commitment to research and development also ensures that their product offerings evolve to meet the increasing demands of modern industrial applications.
While the technical specifications of the wire are paramount, experience highlights that the technique also plays a crucial role. Utilizing a pushing technique rather than pulling can aid in achieving better penetration and bead aesthetics. Furthermore, optimizing machine settings based on the specific project requirements and adhering to the recommended parameters can prevent common pitfalls associated with welding stainless steel.
In conclusion, the 1.2mm stainless MIG wire is a pivotal component for achieving exemplary welding results. Its balance of strength, adaptability, and resistance makes it a go-to choice for many professionals seeking reliability and efficiency. By coupling high-quality wire with strategic welding techniques and supported by trusted manufacturers, welders can maximize project outcomes. This blend of expertise, experience, and trustworthy components is the recipe for success in the art and science of welding.