Choosing the right wholesale CO2 welding wire is crucial for achieving optimal welding performance and ensuring the quality and durability of welded products. With a myriad of options available in the market, understanding how to select the best product necessitates a thorough understanding of welding processes, the materials involved, and the specific requirements of the job.
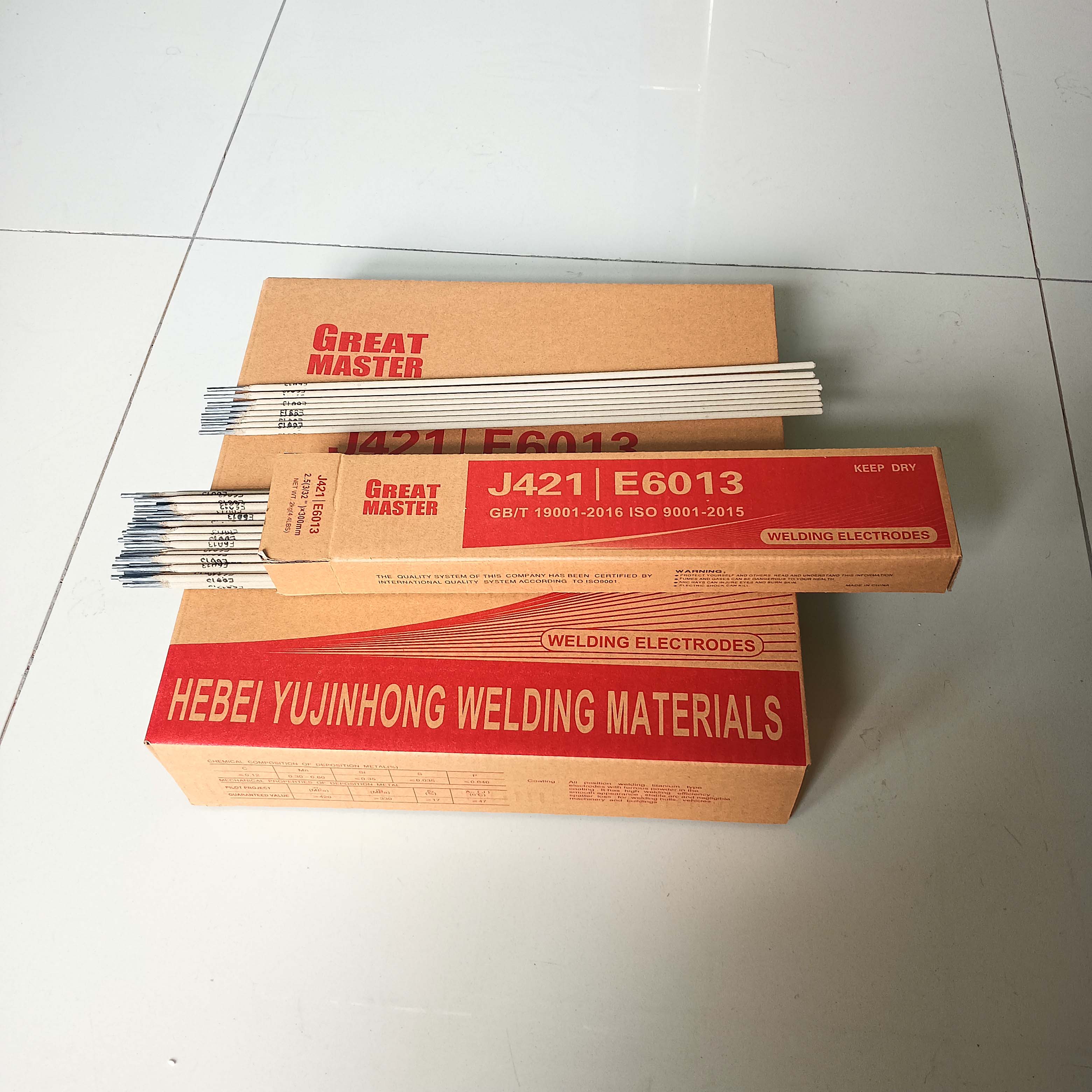
CO2 welding, also known as MIG (Metal Inert Gas) welding, is widely favored in industries such as automotive, construction, and shipbuilding due to its efficiency and effectiveness in joining various metals. The welding wire used in this process is one of the key components that directly affect the quality of the weld. Wholesale CO2 welding wire suppliers offer a range of options, and selecting the right one involves evaluating multiple factors including composition, diameter, and tensile strength.
One of the frequently cited experiences among industry experts is the importance of choosing welding wire composed of high-quality materials. The composition of welding wire determines its compatibility with the metals being welded and its performance under different conditions. For instance, wires with higher manganese content are preferred for welding high-strength steel as they provide better tensile strength and ductility. As an industry professional, ensuring that the welding wire adheres to the requisite standards, such as AWS (American Welding Society) or EN (European Norm), is vital. Certified products not only guarantee quality but also enhance trustworthiness among clients and partners.
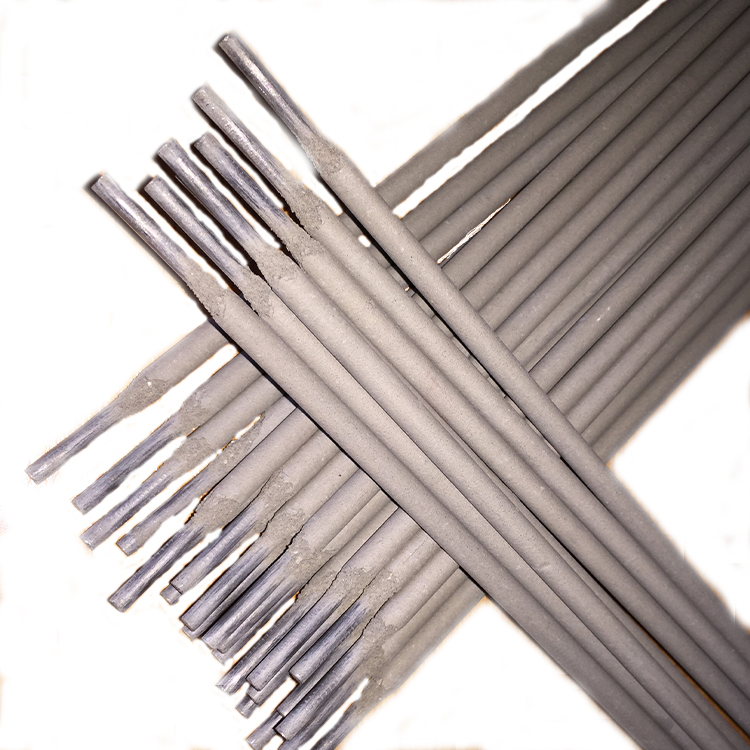
The diameter of the welding wire is another critical aspect that experienced welders pay attention to. The appropriate wire thickness can vary depending on the thickness of the metal being welded and the specific welding technique used. Larger diameter wires are typically used for thicker materials, whereas thinner wires are suitable for thin metals. Choosing the correct diameter ensures efficient weld penetration and reduces issues such as burn-through or inadequate joint strength. Professionals rely on charts provided by manufacturers or conduct practical tests to determine the most suitable wire diameter for specific projects.
wholesale co2 welding wire
Expertise in using wholesale CO2 welding wire also involves understanding how different coatings on the wire can impact the welding results. Copper-coated wires are widespread as they provide excellent feedability and resistance to corrosion, thus enhancing the wire’s lifespan and stability during welding. The choice between copper-coated or non-coated wires should be based on the specific requirements of the application and environmental considerations.
Authoritativeness in this domain is displayed by suppliers who offer extensive technical support and additional resources such as detailed product data sheets and welding parameters. Suppliers who have built a reputation for reliability and quality often provide instructional materials and on-site support to assist welders in optimizing their processes. This level of support is invaluable in complex welding projects where precise control over welding parameters is necessary to achieve desired outcomes.
Finally, trustworthiness is established through consistent quality assurance and transparency. Leading wholesale suppliers implement strict quality control measures, ensuring each batch of welding wire meets high standards before dispatch. They offer warranties or quality guarantees, providing clients with confidence in their purchase. Transparent communication regarding the supply chain, from manufacturing processes to delivery timelines, further solidifies a supplier’s position as a trusted partner.
In conclusion,
selecting the ideal wholesale CO2 welding wire involves more than just cost considerations. It requires a profound understanding of welding processes, material compatibility, and the specific demands of the project at hand. Experienced welders and industry experts emphasize the significance of material composition, wire diameter, coating types, and the support offered by suppliers to ensure high-quality, reliable, and durable welds. By prioritizing these factors, welding professionals can enhance their operations and deliver exceptional results while maintaining an edge in a competitive industry.