In the welding industry, the selection of welding wire plays a critical role in determining the quality and durability of a weld joint. Among the myriad of options, 70s6 welding wire stands out due to its specific advantages tailored for various applications.
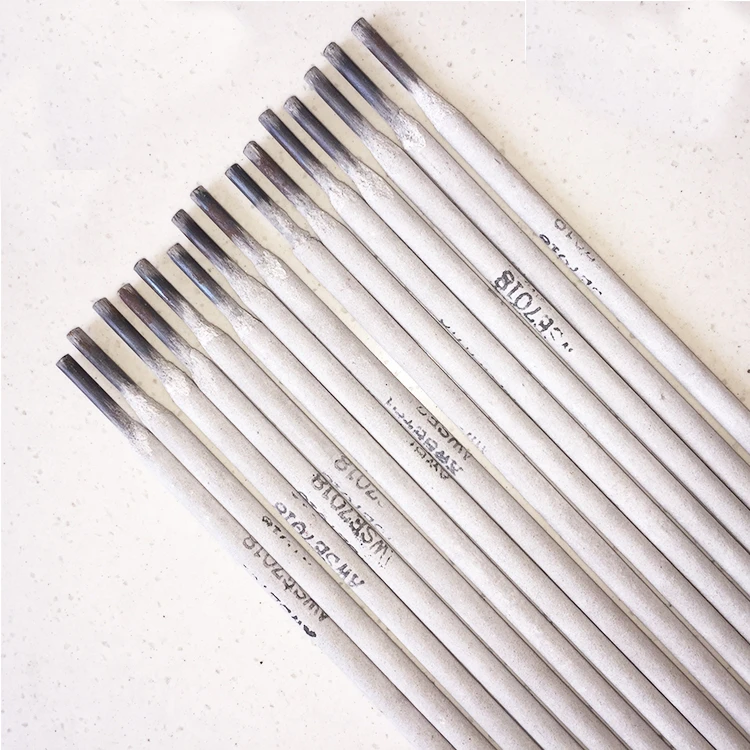
70s6, a well-recognized designation within ER70S-6 wires, is engineered with a chemical composition that includes higher levels of manganese and silicon. This particular formulation enhances the arc quality, enabling it to produce a stable arc that is easy to control. Welders across the globe value this stability as it significantly reduces spatter, leading to a cleaner weld zone and minimizing the time and effort spent on post-weld cleanup.
One of the standout features of 70s6 welding wire is its versatility in dealing with mill scale and rust. In real-world applications, achieving perfectly clean base metal prior to welding is not always feasible. The deoxidizers in 70s6 wire provide excellent bead wetting and allow it to compensate for slightly contaminated surfaces, thus improving weld aesthetics and reducing defects. This makes it exceptional for maintenance and repair operations where surface preparation might be less than ideal.
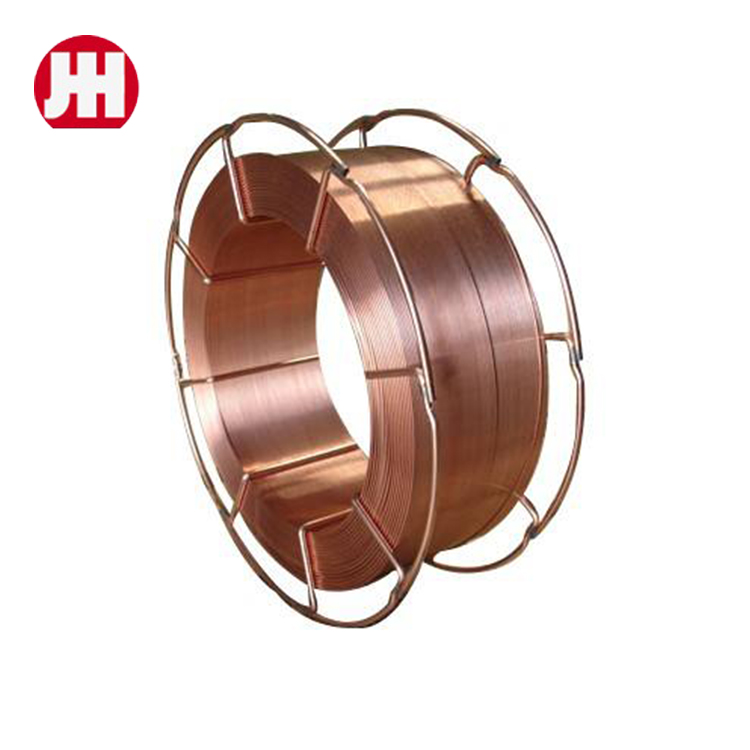
From a mechanical standpoint, welds produced with 70s6 wire exhibit impressive tensile strength, often reaching or exceeding the base material's capabilities. The wire also ensures good notch toughness, which is vital for applications subjected to dynamic loads or impact. Industries such as automotive, heavy machinery, and structural steel fabrication often rely on this wire for its dependable performance in demanding scenarios.
Professionals in the welding field because 70s6 welding wire can be effortlessly utilized with a variety of shielding gases. When used with 100% CO2, it provides deep penetration, making it suitable for thicker materials. Alternatively, a mixture of Argon and CO2 enhances the arc stability even further, making the weld bead more visually appealing and easier to control.
70s6 welding wire
Additionally, 70s6 is available in various diameters suitable for different welding machines and applications. Its adaptability extends to both manual and automated welding processes, making it a preferred choice for production environments with varying welding setups.
Safety is another vital area where 70s6 demonstrates its reliability. Its formulation minimizes the potential for hazardous fumes, creating a safer workplace environment. However, adhering to standard protective measures in welding environments is crucial to ensure worker safety.
For businesses looking to optimize their operational costs, 70s6 presents a cost-effective option without compromising on quality.
Its high deposition rate reduces welding time and ultimately improves project turnaround. By leveraging this, organizations can maintain production schedules while adhering to budget constraints.
Choosing 70s6 welding wire does not simply rely on its technical specifications but extends to supplier reliability, ensuring consistency and quality delivered time after time. Reputable manufacturers often back their products with certifications and rigorous quality control, enhancing trustworthiness. Collaborating with suppliers who provide robust technical support services can further empower users to tackle specific welding challenges and reach optimal results.
In conclusion, ER70S-6 (70s6) welding wire's unique blend of deoxidizers, excellent mechanical properties, and versatility with different welding gases make it an indispensable component for welding professionals. Ensuring safe, efficient, and strong welds across various applications affirms its position within the market. By carefully selecting a trusted supplier, businesses and individual welders alike can benefit from the reliable performance offered by this exemplary welding wire.