Understanding the Essentials of Welding Electrodes A Guide to Professional Choice and Application
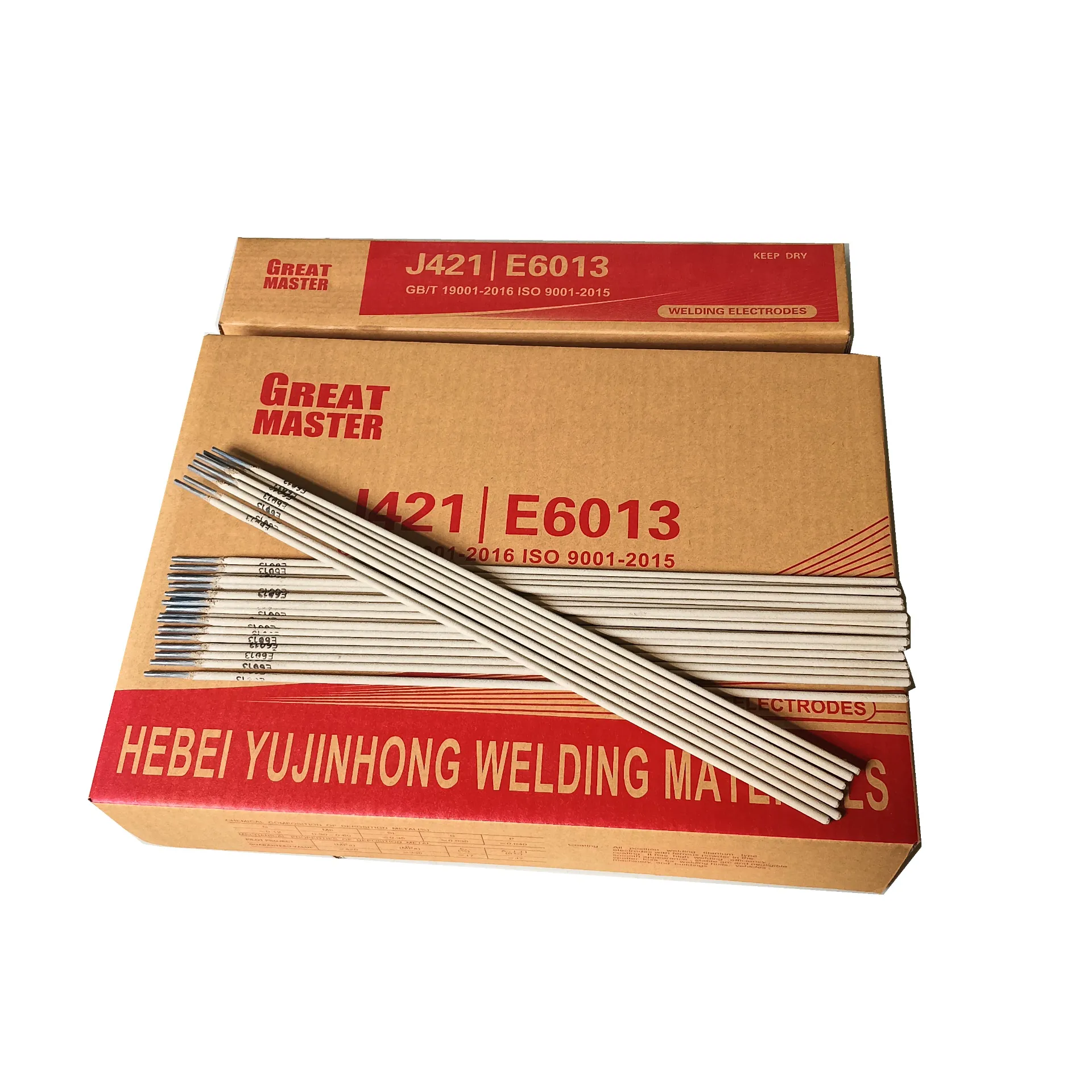
The welding industry stands as a core pillar in the construction and manufacturing sectors, necessitating precise tools and materials. Welding electrodes, critical components in the welding process, have a profound impact on the quality and durability of welded structures. These electrodes, which carry the current to the weld joint, melt to form a fused metal joint between two surfaces. Selecting the right welding electrode entails understanding their types, applications, and the specific needs of your project.
In the realm of welding electrodes, various types exist, each tailored for specific applications. The primary classification distinguishes between consumable and non-consumable electrodes. Consumable electrodes, which form weld metal as they melt during the welding process, are commonly made from materials similar to the workpieces to ensure compatibility. Non-consumable electrodes, predominantly tungsten, are used in processes where the electrode is not meant to melt into the weld, such as Tungsten Inert Gas (TIG) welding.
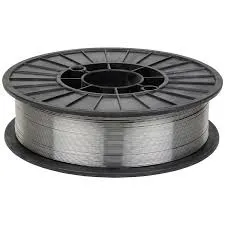
Consumable electrodes, often referred to as stick electrodes or welding rods, are categorized further based on their coating and core material. Each category offers distinct advantages and is suited for particular tasks. For instance, electrodes with a rutile coating are valued for their ease of use and smooth weld appearance, making them ideal for thin materials and non-critical jobs where aesthetics are a factor. Basic electrodes, with a low hydrogen coating, provide superior toughness and are imperative in structural applications where weld integrity must withstand hefty stresses.
The choice of an electrode extends beyond the type and coating. Factors such as the welding position, base metal composition, and environmental conditions play crucial roles. Horizontal, vertical, overhead, and flat positions require specific electrode characteristics to ensure easy handling and effective results. Additionally, the composition of the base metal must align with the electrode material to minimize the risk of weld failure. Conditions such as temperature and humidity further influence the electrode selection, as certain coatings may absorb moisture, leading to hydrogen-induced cracking.
welding electrode
Gaining proficiency in selecting the appropriate welding electrode not only enhances the quality of the welds but also boosts efficiency and safety.
Experience in diverse welding scenarios contributes to this expertise. Master welders often rely on tried-and-true combinations of metallurgy and technique, honed through years of practice. Consulting authoritative sources, such as industry standards and manufacturers' guidelines, provides invaluable insights into the properties and recommended uses for different electrodes.
Trustworthiness in electrode performance is paramount, especially in applications where failure is not an option. Evaluating manufacturers based on quality certifications and adherence to international welding standards aids in making informed decisions. Many renowned brands offer detailed product specifications and testing data to affirm the reliability of their electrodes, fostering confidence among professionals.
Finally, it is essential to remain current with advancements in welding technology and materials. Innovations in electrode design, such as the development of environmentally friendly coatings and enhanced durability, can offer advantages in efficiency and sustainability. Engaging with professional welding communities and continuing education opportunities ensures that knowledge remains relevant and up-to-date.
In conclusion, welding electrodes are more than consumables in the welding process; they are pivotal elements that dictate the success and longevity of welds. By leveraging experience, expertise, authoritativeness, and trustworthiness, professionals can ensure high-quality, dependable welding outcomes. Through a careful assessment of project requirements and an informed selection of welding electrodes, welders can achieve optimal results while adhering to safety and quality standards.