The 7018 welding rod, particularly in the 1/8 inch size, is a staple in the arsenal of many welding professionals. Known for its versatility and ease of use, it offers a perfect blend of strength and performance that caters to a variety of welding needs. This article delves deep into the attributes that make the 7018 welding rod a preferred choice, its applications, and essential practices to get the most out of it, all while adhering to the principles of SEO optimization to aid your search for reliable, expert information.
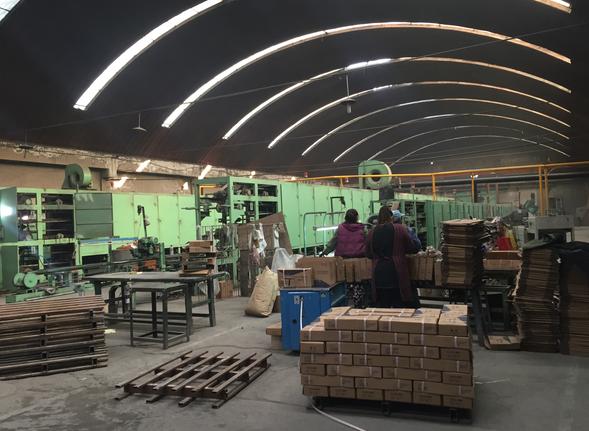
The prominence of the 7018 welding rod stems from its low hydrogen content, which significantly reduces the risk of weld cracking. This feature alone makes it indispensable in industries where structural integrity is paramount. Often referred to as a low-hydrogen stick electrode, the 7018 rod is classified under the American Welding Society (AWS) A5.1 specification, denoting its suitability for welding carbon and low alloy steels.
One of the standout features of the 7018 rod is its impressive tensile strength, rated at 70,000 psi. This makes it ideal for projects requiring high-strength welds, such as infrastructure, shipbuilding, and heavy equipment repair. The 1/8 inch diameter is particularly popular due to its balance between support and precision, making it suitable for a wide range of metal thicknesses.
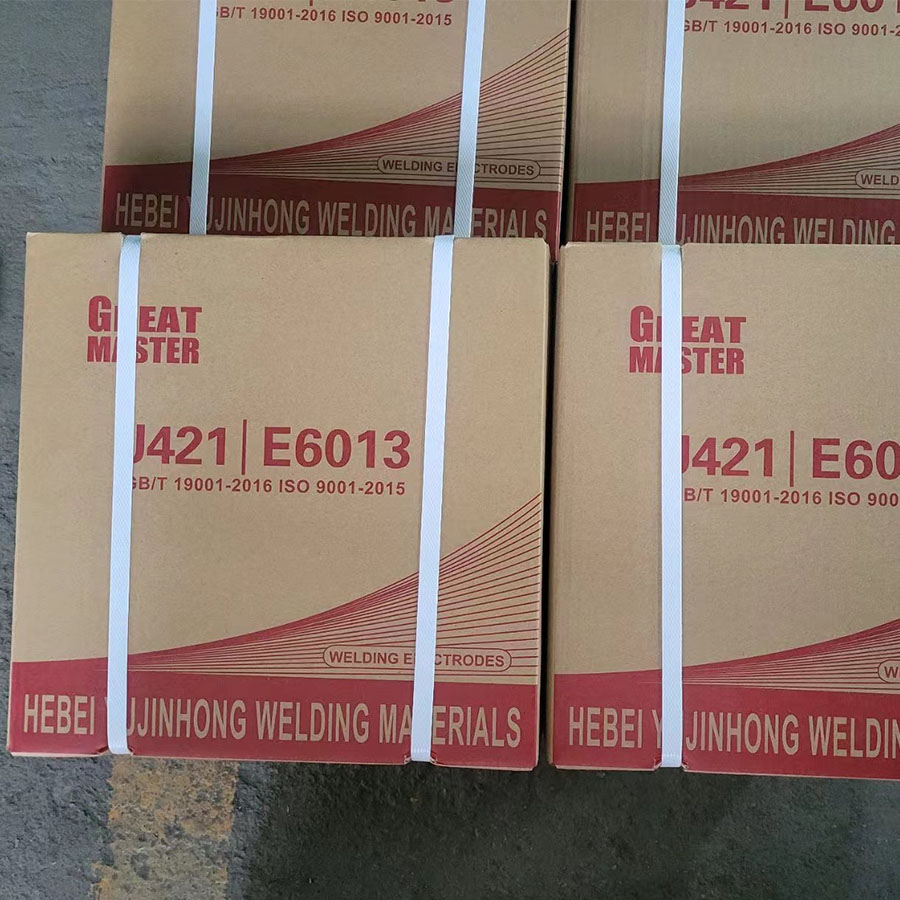
In terms of usability, the 7018 rod is lauded for its smooth arc and minimal spatter, providing a cleaner weld every time. This characteristic not only enhances the appearance of the welds but also reduces post-weld cleaning labor, thus emphasizing efficiency. For those new to welding, this rod's forgiving nature makes it an excellent introduction to more complex welding tasks.
Experience dictates that storage of the 7018 welding rod is crucial. Exposure to moisture can lead to hydrogen absorption, increasing the risk of weld defects. Professionals recommend storing these rods in a dry, controlled environment or using rod ovens to maintain maximum efficacy. Proper storage extends the shelf life of the rods and ensures consistent results, crucial for maintaining the quality of work on large-scale projects.
7018 welding rod 1/8
When discussing expertise, the preferred technique involves running the 7018 rod in a slightly dragging position, compared to other rods which may require different angles. This helps maintain a larger puddle, which solidifies to form a sturdy bond. The experience highlights that consistent speed and angle are paramount in achieving uniformity and penetration—key factors to weld quality.
For those in pursuit of enhancing their welds with the 7018 rod, those with authority in the field stress the importance of practicing bead patterns and adjusting amperage settings according to material thickness. A common pitfall is improper amperage, which can lead to overheating or underpenetration. Expert welders often advise starting with a midpoint amperage for a 1/8 inch rod, then adjusting based on metal behavior during welding.
Trustworthiness in welding often arises from using tried and tested equipment along with quality materials, such as the 7018 rod. Manufacturers like Lincoln Electric and Hobart offer reputable options, known for adhering to industry standards and offering consistent performance. Ensuring welders use genuine products from these manufacturers guarantees reliability and optimal results.
Ultimately, the 7018 welding rod 1/8 inch is an invaluable tool for welders ranging from hobbyists to seasoned professionals. Its combination of strength, usability, and application versatility makes it an irreplaceable component in crafting structurally sound welds across numerous industries. By adhering to recommended storage practices, mastering technique, and choosing reputable materials, welders can fully leverage the potential of this robust rod, ensuring safety and durability in every project.