The 7018 welding rod, sized at 3/32 inches, is a remarkable tool in the world of fabrication and construction, renowned for its unparalleled performance and reliability in producing high-quality welds. This article explores the features, benefits, and applications of the 7018 welding rod, emphasizing its critical role in achieving efficient and lasting welds in various industrial contexts.
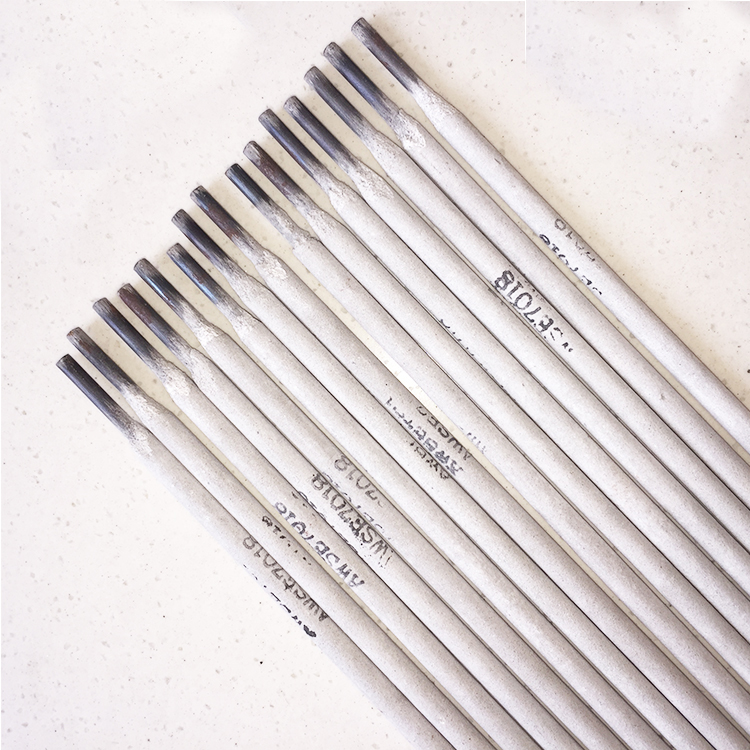
Celebrated among welders for its low-hydrogen, iron powder design, the 7018 welding rod facilitates the creation of welds that are not only exceptionally strong but also have a pleasing aesthetic appearance. One of its standout qualities is its ability to produce smooth, scanty spatter weld beads, contributing to reduced cleanup time and enhanced overall work efficiency. Moreover, this rod excels in tackling tasks that demand precision and the highest degree of structural integrity, especially in areas prone to high-stress levels.
The 7018 electrode is particularly effective when working with carbon steel and low-alloy steel, making it a preferred choice in sectors such as bridge construction, shipbuilding, and pressure vessel manufacturing. The versatility of the 3/32 inch rod allows for high-quality, detailed work in situations where larger rods might prove cumbersome or inappropriate. It’s an excellent suit for fillet welds and other detailed applications, offering considerable flexibility across a wide range of welding positions, including flat, horizontal, and vertical welds.
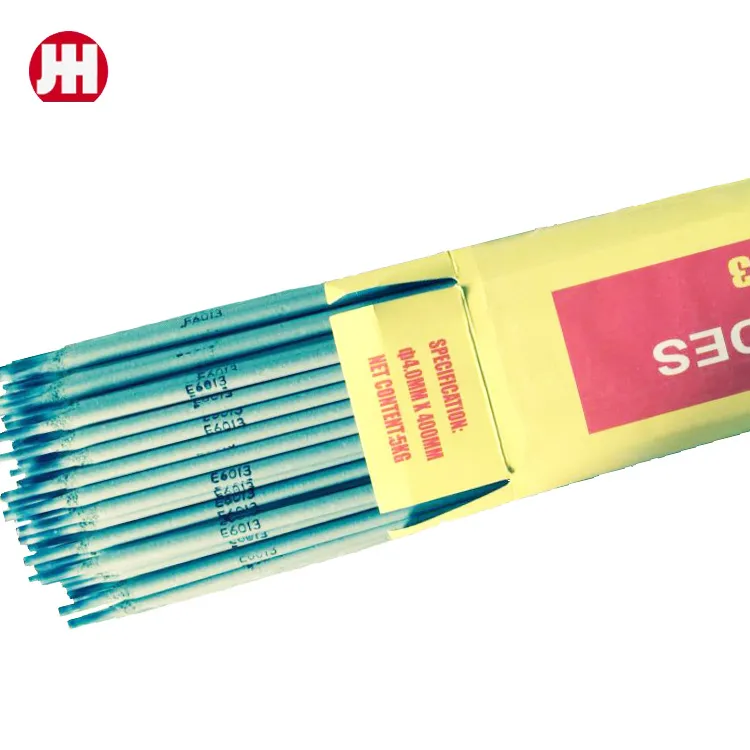
Among its defining attributes is the way the 7018 rod delivers consistent arc stability and ease of use. Even for beginner welders, this rod provides an approachable pathway to professional-quality welds, as its nature helps to control the arc better than many alternatives in its class. A common choice for repairs and maintenance tasks, the 7018 ensures durability and lasting performance in repair jobs, where welding speed is crucial and the risk of defects needs to be minimized.
Reliability in varied conditions also characterizes the 7018. Given its ability to handle high amperage without compromising weld quality, it is ideal for projects involving components that undergo dynamic loading and fatigue stresses. This electrode's nuanced design minimizes hydrogen absorption, significantly reducing the risk of cold cracking and contributing to the weld's fitness for even the most demanding applications.
7018 welding rod 3/32
To further highlight the importance of storage and preparation, the 7018 welding rod requires specific storage conditions to maintain its low-hydrogen properties. These rods should be kept in a dry storage oven to prevent moisture absorption, which could otherwise impair the rod's performance and the integrity of the weld. This attention to maintenance underscores a commitment to quality that aligns with its industrial applications, where precision and reliability are non-negotiable.
Moreover, the reputation of the 7018 welding rod is not merely confined to its technical specifications but extends to its recognition across the welding community as a staple of professional practice. Its ubiquity in industrial applications testifies to its reliability and the trust professionals place in its capabilities. Experts endorse this rod as a go-to option due to its consistency and the impeccable finishing it lends to welding projects, reinforcing its status as an industry-standard.
Leveraging its potential fully, welders are advised to hone their technique and preparation when deploying the 7018. Mastering the intricacies of this welding rod can substantially elevate the quality of outputs and fortify a welder’s repertoire of skills. As the welding industry evolves with advances in technology and method, the 7018 remains an indispensable tool, proving its resilience and adaptability across changing parameters.
In summary, the 7018 3/32 inch welding rod is more than just a consumable; it's a cornerstone of welding technology that embodies excellence and precision for a multitude of demanding applications. Its proven track record makes it a trusted resource for welders worldwide, forging the construction of safe, robust, and durable structures.