Spot welding electrodes are a critical component in manufacturing processes that require the joining of metal sheets. This essential tool enhances efficiency and product quality in industries ranging from automotive to consumer electronics. To maximize the benefits of these electrodes, understanding their properties, types, handling, and maintenance is crucial.
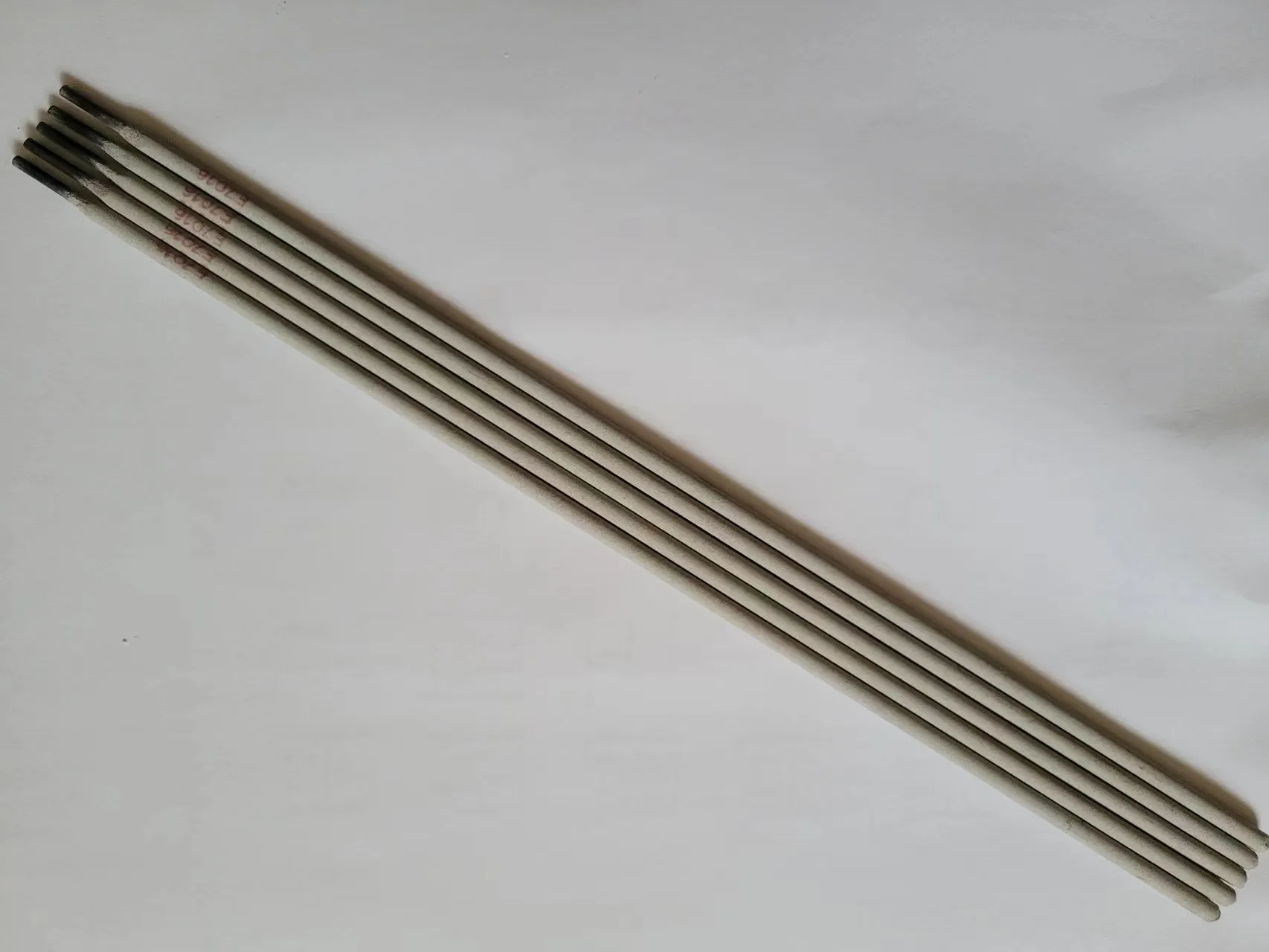
Manufacturers and engineers highly regard spot welding for its ability to produce strong, reliable welds quickly. The process concentrates heat precisely at the joint, fusing metal sheets without the need for additional materials such as solder or adhesives. The electrodes play a pivotal role in directing the electrical current and pressure necessary for the welding process, ensuring efficient energy use and high-quality welds.
The choice of electrode material and design can greatly impact the effectiveness of spot welding. Copper and its alloys are commonly used due to their excellent electrical conductivity and thermal diffusivity. However, within the family of copper alloys, specific types like Copper-Chromium and Copper-Tungsten offer unique properties that cater to different manufacturing needs. Copper-Chromium electrodes, for example, are valued for their hardness and resistance to deformation, making them suitable for high-pressure applications. On the other hand, Copper-Tungsten electrodes offer superior wear resistance and are preferred in high-heat conditions.

Proper handling and maintenance of spot welding electrodes are vital to extend their lifespan and maintain welding quality. Regular inspection is necessary to check for wear and tear, especially on the tips, which are subject to high temperatures and pressures. Dressing the electrodes to maintain the correct tip profile is essential for consistent welds. Using a dressing procedure tailored to the material and type of electrode can prevent premature failure and ensure optimal performance.
Incorporating automated systems for electrode maintenance can provide significant advantages in high-volume production environments. These systems can perform routine dressing and inspections, minimizing downtime and increasing productivity. Moreover, real-time monitoring technologies can alert operators to potential issues before they lead to defects or breakdowns, maintaining a continuous production flow.
spot welding electrode
Training and expertise in handling spot welding electrodes cannot be overstated. As technology advances, the integration of digital controls and monitoring in welding operations depicts an ever-increasing complexity. Understanding the nuances of electrode materials, settings, and configurations forms the core knowledge required by modern welding engineers. This expertise not only ensures adherence to industry standards but also facilitates innovation and improvements in welding practices.
Developing a keen understanding of the interactions between different metals and electrodes will enhance weld quality. Factors such as the thickness and type of metal being welded affect the choice of electrode material and shape. For example, thicker materials may require electrodes with greater thermal mass to dissipate heat effectively, preventing overheating that could compromise the weld integrity.
In recent years, the push towards sustainable and environmentally friendly manufacturing has also impacted the development of spot welding electrodes. Advances in materials science have led to the creation of electrodes with reduced environmental impacts, incorporating recycled materials wherever possible. These initiatives support the broader industry trend towards sustainability without compromising the quality and efficiency of the welding process.
Spot welding electrodes are more than just simple tools; they are a key to unlocking efficient and effective manufacturing processes. By understanding their properties, and maintaining them properly, manufacturers can enhance their productivity and product quality. Continuous development and research into new materials and technologies promise to keep spot welding at the forefront of metal joining techniques, meeting the evolving demands of industries worldwide.