When investing in welding equipment and materials, choosing the right wholesale flux-cored welding wire can significantly impact productivity and weld quality. The flux-cored welding process, known for its efficiency and versatility, is crucial for various industrial applications, particularly in situations where traditional MIG welding may not suffice. Here, we delve into the nuances of selecting high-quality wholesale flux-cored welding wire, shedding light on the essential factors to consider to achieve optimal welding results and cost efficiencies.
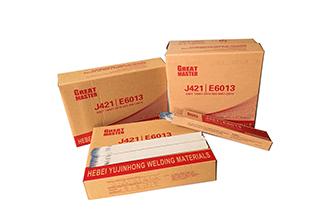
First and foremost,
understanding the composition and functionality of flux-cored welding wire is imperative. This type of wire is designed with a hollow core filled with fluxing agents, which serve multiple functions during the welding process, such as increasing deposition rates and improving arc stability. The importance of these features is primarily observed in heavy-duty industrial setups, where weld integrity is paramount.
Incorporating experience from seasoned welders, one can appreciate the nuanced differences in the performance of various brands and types of flux-cored welding wires. According to industry experts, selecting wires that offer consistent feedability, minimal spatter, and excellent slag removal can expedite clean-up processes and enhance overall workflow efficiency. Additionally, wires that maintain their integrity under varying environmental conditions—such as humidity or temperature fluctuations—are often recommended for maintaining consistent weld quality.
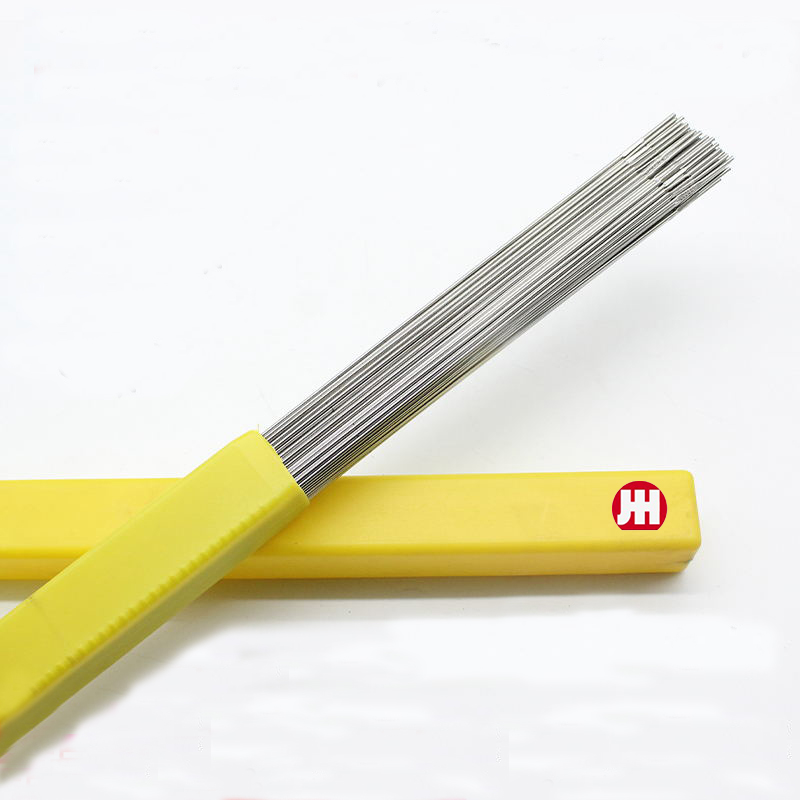
From a professional standpoint, expertise in matching the right type of flux-cored wire with the specific base material and welding position is vital. For instance, using a general-purpose wire for carbon steel often suffices for routine tasks, but more complex projects with alloyed metals might require specific alloy compositions in the wire to prevent oxidation and enhance joint strength. Thus, consultation with technical data sheets and material safety data sheets (MSDS) provided by reputable manufacturers is advisable to guide the selection process.
wholesale flux-cored welding wire
The authority of a flux-cored welding wire supplier can also play a substantial role in ensuring dependable product quality. Established manufacturers who adhere to rigorous quality control processes and comply with international welding standards, such as AWS or ISO certifications, tend to offer wires that consistently meet performance expectations. Some key players in the industry provide thorough technical support and training, fostering long-term partnerships characterized by mutual growth and enhanced technical acumen, which can greatly benefit welding operations.
Trustworthiness in the realm of flux-cored welding wire is fundamentally about reliability and performance consistency. Welders and procurement personnel often rely on word-of-mouth recommendations and verified customer testimonials in determining a supplier’s credibility. Furthermore, transparency in sourcing raw materials and the manufacturing process contributes significantly to a supplier's trustworthiness, assuring customers of the quality and safety of the welding wire used in their operations.
For those seeking wholesale purchases, price negotiations and bulk discounts are also strategic considerations. Assessing the total cost of ownership, which includes not just the purchasing price but also factors like the ease of use and maintenance requirements, can guide buyers in making informed decisions.
In conclusion, selecting the right wholesale flux-cored welding wire involves a comprehensive evaluation of its characteristics and the credibility of its manufacturer. Utilizing experience gleaned from field applications, aligning with expert guidance, and choosing products from authoritative and trustworthy sources are key to optimizing the welding process. Such an approach ensures enhanced operational efficiency and weld quality, ultimately leading to successful project outcomes and long-term business sustainability.