When it comes to the realm of industrial welding, choosing the right materials can significantly impact the quality, durability, and overall success of any project. One fundamental component is the filler welding rod, a seemingly small element that plays a crucial role in the welding world. Understanding the nuances of filler welding rods and how they can be best utilized offers a distinct advantage for professionals in this field.
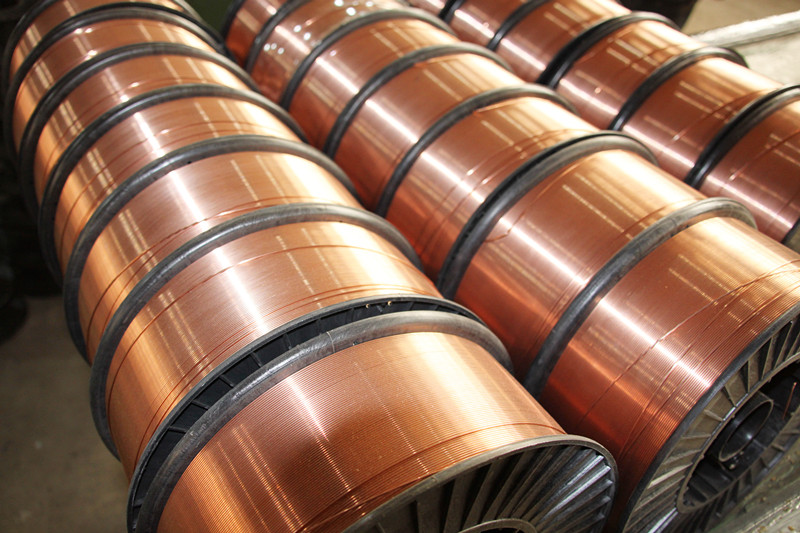
Filler welding rods, also known as consumable electrodes, are critical in projects where two or more metal pieces are being joined. These rods melt alongside the base materials, becoming an integral part of the weld. The success of the welding process heavily relies on selecting a filler rod with compatible chemical composition and mechanical properties with the materials being welded.
When discussing expertise, nothing stands more crucial than the composition of filler rods. Typically made from a variety of metals like steel, aluminum, nickel, or copper, each type offers distinct characteristics suited for specific applications. For instance, mild steel rods are incredibly versatile, ideal for general-purpose welding where strength and ductility are required. Alternatively, aluminum rods are perfect for projects needing lightweight and corrosion-resistant joints.
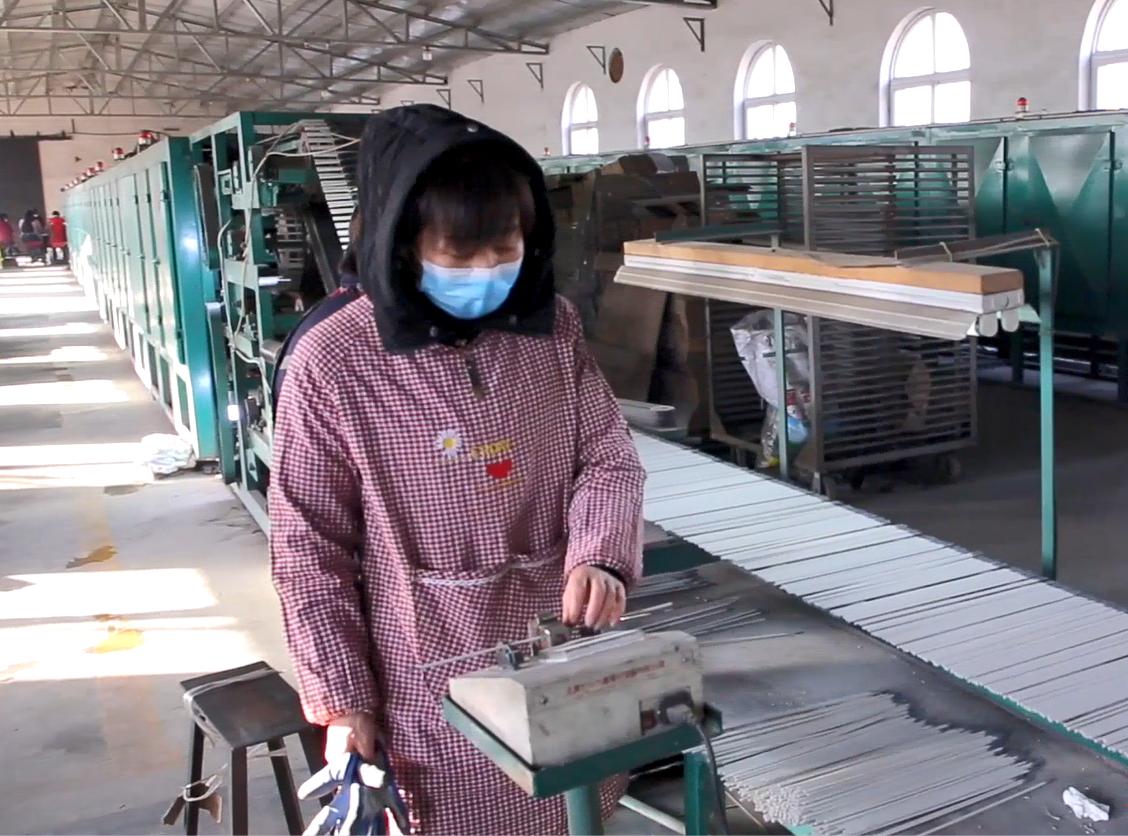
The choice of filler rod also significantly impacts the thermal properties of the welded joint. For instance, stainless steel welding rods provide superior heat resistance and can maintain structural integrity in environments that experience high thermal stress. This highlights the importance of understanding the metallurgy and thermal conductivity of the materials involved to achieve a reliable weld.
From an authoritative perspective, industry standards and specifications further guide the selection of filler rods. Standards such as the American Welding Society (AWS) coding system classify rods by tensile strength, positioning capabilities, and coating types. This authoritative guideline ensures the rod selected is suitable for the specific application needs, whether the project involves the construction of bridges, manufacturing of automotive parts, or even the assembly of aerospace components.
filler welding rod
Experience tells us that beyond choosing the right material composition, the physical dimensions of the filler rod also matter. The diameter of the rod influences the deposition rate and penetration of the weld. Large diameter rods are typically used in thicker materials needing higher deposition rates, while smaller rods offer greater control and are ideal for precise applications or thinner materials. Understanding and experimenting with these variables through hands-on experience can significantly enhance the quality of the weld.
Moreover, trustworthiness in the welding process is deeply rooted in recognizing and mitigating potential issues that could arise from poor quality filler rods. Quality control checks such as ensuring rods are stored in proper conditions to prevent contamination or oxidization can preserve their effectiveness. Additionally, rods should be examined for uniformity and homogeneity to avoid inconsistencies in the weld.
Another consideration is the adaptability of modern filler welding rods in various welding techniques, including MIG, TIG, and stick welding. Each technique demands specific rod types and skills, emphasizing the importance of training and technical know-how. For instance, TIG welding, known for producing high-quality welds on thinner materials, requires rods with excellent melting characteristics and minimal impurities.
To cultivate a high level of trust with clients and stakeholders, welders should also convey confidence in their knowledge of filler welding rods. This can be demonstrated through certifications, extensive training, and continuous learning to keep abreast of the latest advancements and innovations in welding technology.
In essence, the filler welding rod, while a small component, wields significant influence over the success of a welding project. A comprehensive understanding encompassing the composition, industry standards, application techniques, and quality assurance not only elevates the standards of work but also builds a foundation of trust and authority within the welding industry. Recognizing these facets ensures projects are completed with the highest degree of precision and reliability, ultimately enhancing long-term performance and client satisfaction.