Selecting the right titanium welding rod is a critical factor in achieving successful welding outcomes, especially for projects that demand precision and durability. Titanium, known for its impressive strength-to-weight ratio and resilience against corrosion, has become a preferable choice in industries like aerospace, automotive, and medical equipment manufacturing. However, working with this metal requires a deep understanding of its properties and the tools that will ensure a quality weld.
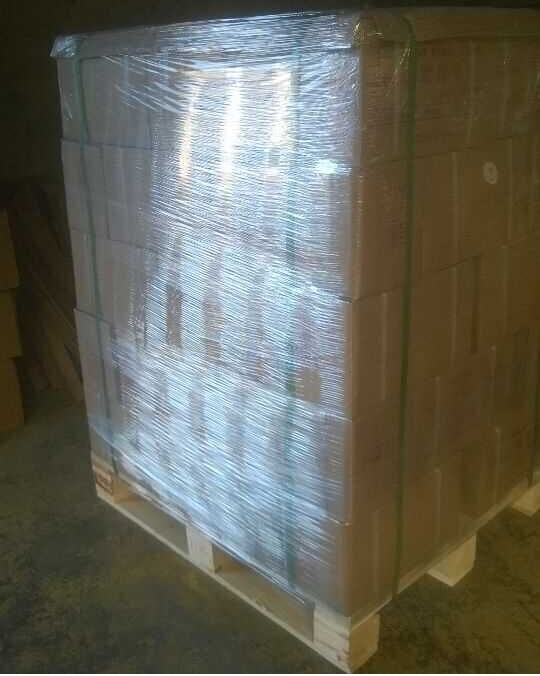
Experience plays a fundamental role in mastering the use of titanium welding rods. Experienced welders acknowledge that the key to using titanium rods effectively lies in consistent practice and a genuine understanding of the metal’s unique characteristics. One crucial experience-based tip is always to maintain a clean working environment. Titanium is highly sensitive to contamination, and even minute particles can compromise the weld’s integrity. Expert welders recommend regular cleaning of the welding area and tools to prevent any form of contamination. This practice ensures that the protective oxide film present on titanium surfaces is not disrupted, maintaining the metal’s resistance to corrosion.
Expertise in welding also involves choosing the right type of titanium rod. Titanium welding rods vary in their alloy composition, each designed for specific applications and conditions. For instance, CP (Commercially Pure) Grade 1 rods are often used for their excellent corrosion resistance and ductility, making them ideal for chemical tanks and desalination structures. In contrast, Ti 6Al-4V is widely utilized for high-strength requirements in aerospace components. A professional welder must assess the project's specific needs and select a rod that offers the best balance of strength, weight, and corrosion resistance.
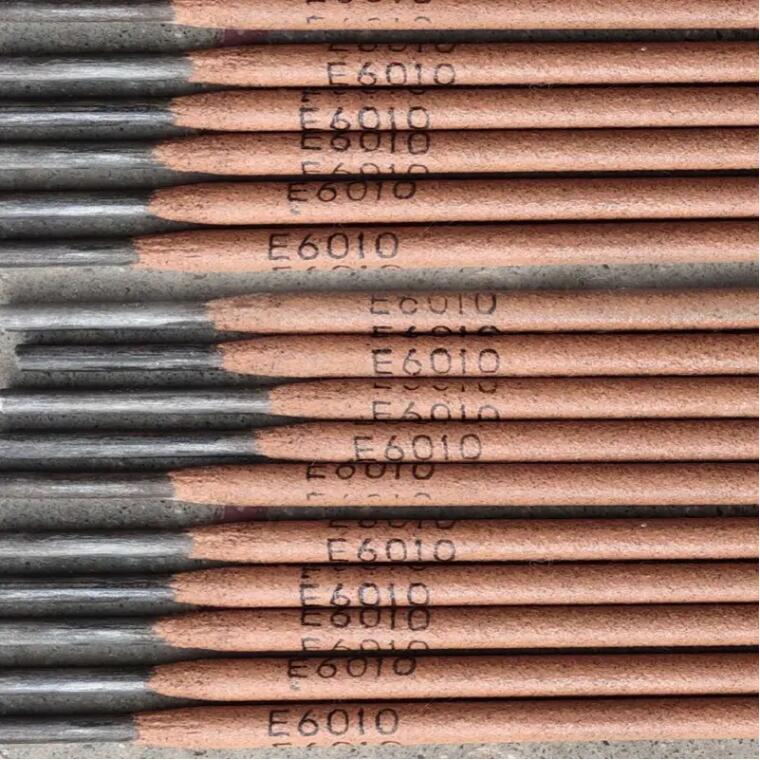
Quality equipment selection highlights authoritativeness in titanium welding. Using advanced tools and technology like inverter welding machines, which provide more control over the welding process, is recommended by industry authorities. Such machines help in maintaining stable arcs and meeting the critical thermal management needs during welding. Authoritative sources suggest using a gas lens in gas tungsten arc welding (GTAW) to ensure improved gas coverage, reducing the risk of any unwanted reactions with oxygen or nitrogen.
titanium welding rod
Trustworthiness in the context of titanium rod welding is underpinned by adherence to safety standards and continuous learning. Trust is built by operating with a commitment to both personal safety and the quality of the project. This involves wearing adequate personal protective equipment, such as gloves and masks, to safeguard against burns and inhalation of potentially harmful fumes. Additionally, staying updated with the latest industry standards and welding techniques reflects a trusting and professional approach to the craft.
For welders aiming to refine their titanium welding skills, there are numerous resources and training programs available. Engaging with welding communities, participating in workshops, and taking certification courses can significantly boost one’s expertise and credibility in the industry. As technology evolves, staying informed about innovations in welding techniques and equipment is paramount. Publications from welding societies and industry conferences serve as excellent resources for acquiring new knowledge and enhancing one’s welding practices.
In conclusion, the art of welding with titanium rods hinges on a combination of hands-on experience, technical expertise, authoritative equipment usage, and a trustworthy attitude toward safety and continuous improvement. As industries increasingly lean towards lightweight and high-strength materials like titanium, the role of skilled welders becomes even more vital. Mastery in using titanium welding rods not only ensures high-quality results but also reinforces the safety, efficiency, and innovation within the manufacturing processes that define modern engineering.