The role of welding rods in the world of metal fabrication and repair is indispensable. Selecting the right welding rod is crucial for ensuring the durability and quality of welded materials. This article delves into the various aspects of welding rods, offering readers a comprehensive understanding of their function, selection, and application.
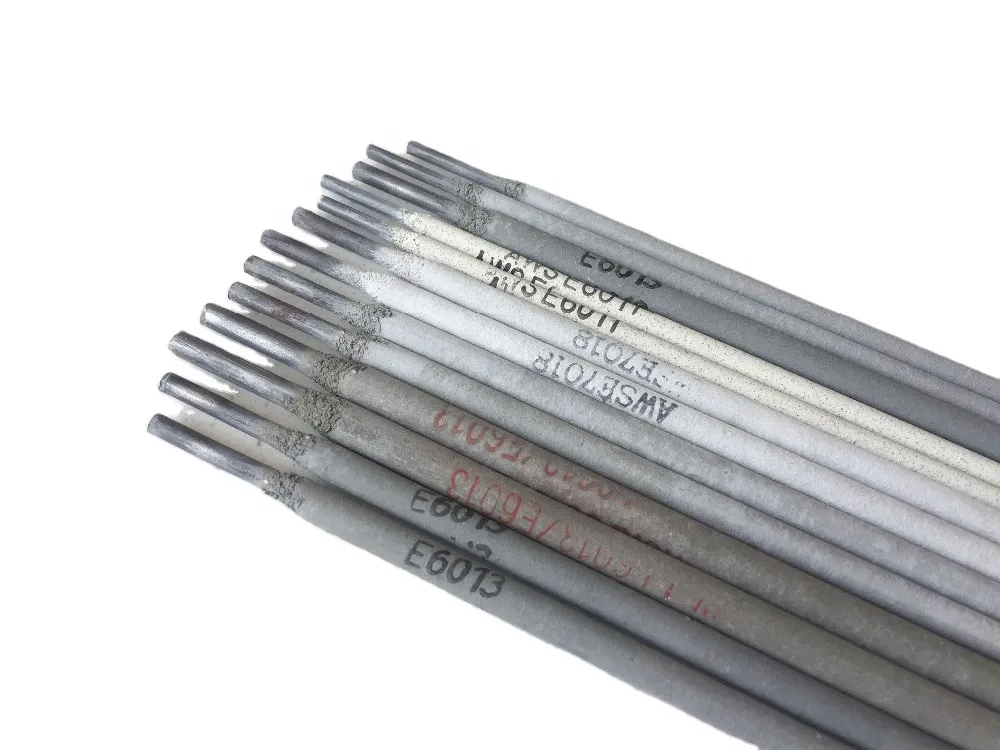
Welding rods, also known as filler metals, are central to the welding process. They are used to join two pieces of metal together, providing additional material that melds with the base metals to create a strong bond. The variety in welding rods is significant, with each type designed for specific materials and welding conditions. Their composition can range from mild steel and stainless steel to aluminum, nickel, and other alloys, each offering unique properties that affect the weld's strength and longevity.
Experience plays a significant role in understanding welding rod selection. A seasoned welder understands that choosing the correct rod greatly determines the weld’s outcome. Factors like the material to be welded, the position of the weld, and the required strength all influence rod selection. For instance, rods such as E6010 and E6011 are often used for their deep penetration capabilities, making them ideal for welding through rust, oil, or dirt. Conversely, E7018 rods are preferred for their low-hydrogen characteristics, which prevent cracking in high-strength steels.
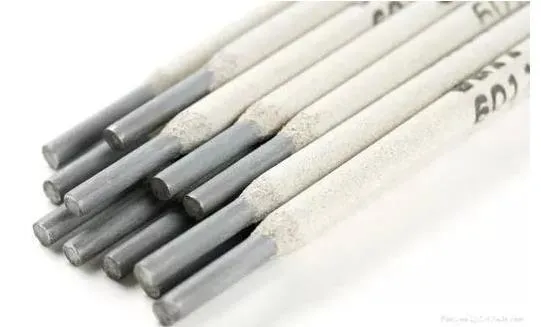
Expertise in welding also involves knowing how various rods perform under different conditions. Certain rods are engineered to work in specific positions—flat, horizontal, vertical, or overhead—making them preferred choices for projects that require position-specific welding skills. Furthermore, the diameter of the welding rod also plays a critical role; larger rods are suited for thicker materials, providing robust welds, while smaller rods are beneficial for thin materials, avoiding burn-through.
welding rod
The authority of selecting the correct welding rod also extends to understanding industry standards. Adherence to guidelines set by organizations like the American Welding Society (AWS) ensures the rods used are up to the mark in terms of quality and reliability. Compliance with these standards not only guarantees structural integrity but also boosts client trust by ensuring that the best practices are being followed.
Trustworthiness in the use of welding rods comes from the reliability and consistency they provide in weld quality. Manufacturers of welding rods, like Lincoln Electric, ESAB, and Hobart, invest heavily in research and development to produce rods that meet rigorous testing standards. This commitment to quality ensures that when welders choose these brands, they are choosing a product with a track record of excellence and dependability.
In conclusion, welding rods are the backbone of metalwork, vital for ensuring the structural integrity of welded projects. Their selection is a blend of experience, expertise, industry authority, and trust in manufacturers' reputations. As the field of welding technology continues to evolve, the role of high-quality welding rods remains crucial, ensuring that welders can achieve the strongest, most reliable welds possible. Selecting the right rod not only dictates the quality of the weld but also impacts the overall efficiency of the welding process, making it a cornerstone of successful metal fabrication and repair projects.