Stick welding, also known as shielded metal arc welding (SMAW), remains one of the most versatile and essential methods in the welding industry. As the backbone of numerous construction, repair, and industrial projects, understanding the nuances of AC stick welding is crucial for both seasoned professionals and newcomers seeking to master this skill.

AC (alternating current) stick welding is an effective technique for various applications that require deep penetration and strong welds, particularly on ferrous metals like steel and iron. One of its main advantages is its ability to work well with materials that are rusty, dirty, or slightly contaminated—a challenge for other welding processes. This resilience is attributed to the electric arc formed between the welding electrode and the workpiece, which creates intense heat to melt and fuse the materials together.
In terms of expertise, it's vital to select the right equipment and electrodes for AC stick welding. The choice of electrode is fundamental; commonly used ones include the E6011 and E6013, each providing specific benefits depending on the welding conditions and the desired strength of the weld joint. The E6011 electrode is particularly favored for its excellent performance on dirty or weathered surfaces due to its aggressive arc and deep penetration capabilities, making it suitable for outdoor construction work. The E6013, on the other hand, offers smoother arcs and is ideal for beginners working on cleaner surfaces with thinner materials.
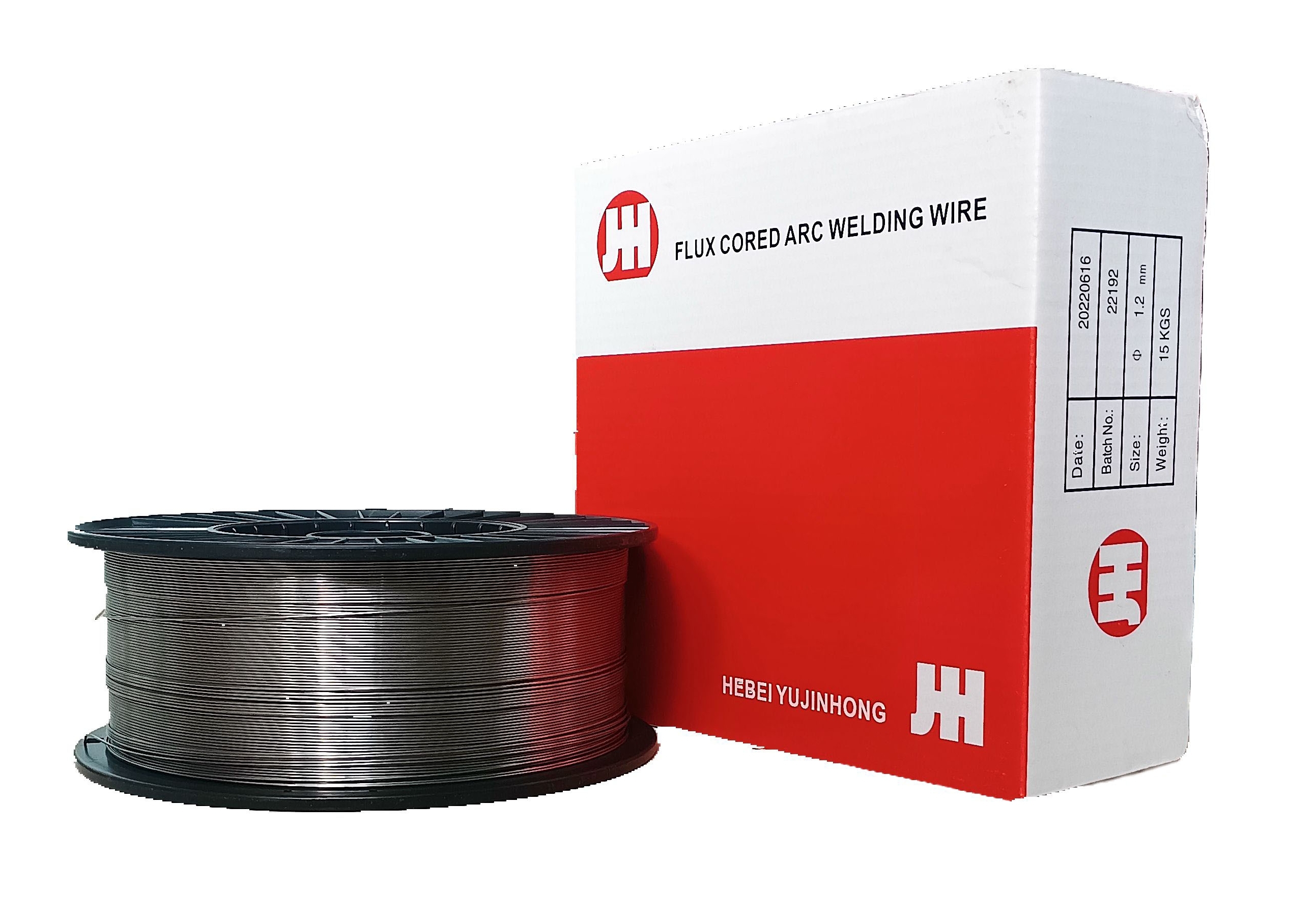
When you delve into the technicalities of stick welding, AC power supply can be both a strength and a challenge. Unlike DC (direct current), AC poses a bit of a hurdle due to its tendency to create arc blow, which can distort the welding arc. However, this very characteristic of AC can be an advantage when welding over long joints or when high currents are required, as it tends to distribute heat more evenly, minimizing distortion of the workpiece.
ac stick welding
Safety is a paramount concern in stick welding. An authoritative understanding of safety equipment is essential. This includes wearing a quality welding helmet with an appropriate shade lens to protect against harmful UV and IR rays, welding gloves to safeguard hands from spatter and heat, and protective clothing made of flame-resistant materials. Adequate ventilation should also be ensured to avoid the inhalation of potentially hazardous fumes. By adhering to these safety precautions, welders can create a secure environment while maintaining the quality of their work.
An underdiscussed angle in the stick welding discourse is the skill and practice required to perfect the technique. Mastery of hand positioning, travel speed, and electrode angle directly impacts the quality of the weld. Expert techniques involve maintaining the correct arc length, typically equivalent to the diameter of the electrode, to ensure a stable arc and consistent bead. These aspects of technique often differentiate professional-grade welds from amateur attempts. Regular practice and understanding feedback from previous welds are integral to improving one's welding prowess.
AC stick welding's relevance is further underscored by its accessibility and cost-effectiveness. It does not require shielding gas, as the electrode coatings provide the necessary protection from atmospheric contamination throughout the welding process. This makes it an economically viable option, especially in settings where portability and immediate setup are priorities. Consequently, stick welding remains a reliable choice for remote jobs and fieldwork where transport of bulky equipment is impractical.
In conclusion, the merit of AC stick welding is evident through its adaptability, efficacy under less-than-ideal conditions, and lower operational costs. Its capabilities span across numerous applications, making it an indispensable tool in the welding repertoire. True expertise in this field is achieved by understanding the interplay of the equipment, technique, materials, and safety protocols. By combining these elements, welders can produce robust, high-quality welds that meet industry standards and exceed client expectations.