Selecting the right electrode for TIG welding is crucial in defining the quality and efficiency of the welding process. TIG, or Tungsten Inert Gas welding, employs a non-consumable tungsten electrode to produce the weld. Electrode choice can significantly impact the welding results, making expertise in this area vital.
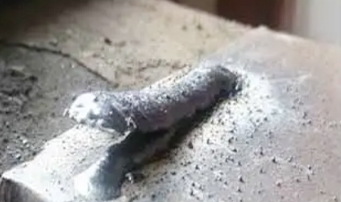
TIG welding owes much of its versatility and effectiveness to the inherent properties of tungsten electrodes. They withstand extremely high temperatures, boast excellent thermal conductivity, and are renowned for their strength and durability. These qualities make tungsten electrodes irreplaceable in achieving precision and low-distortion welding projects.
When considering the best electrode for a specific project, one must take several key factors into account
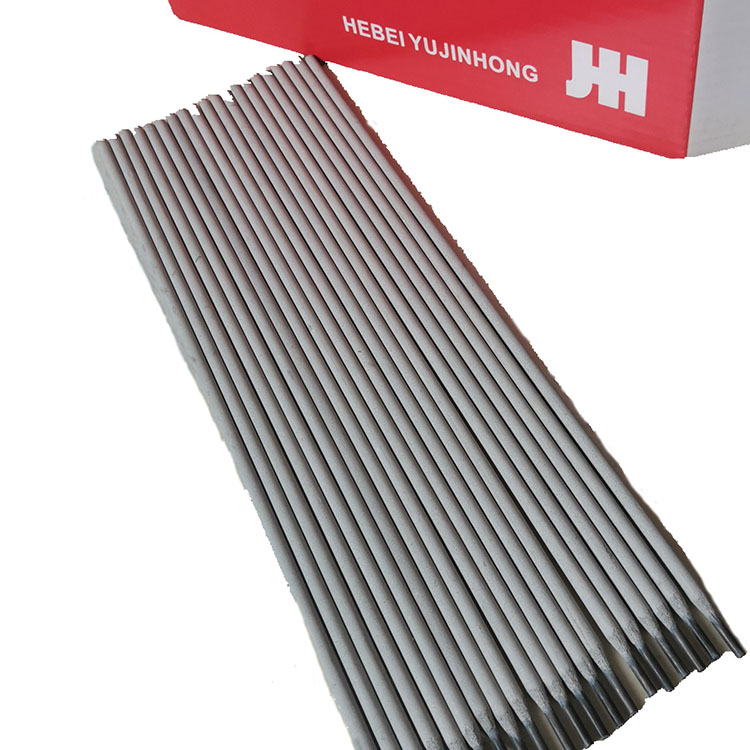
1. Composition of Tungsten Electrodes
Tungsten electrodes are available in a variety of compositions, each offering distinct properties suitable for different applications. The most commonly used types include pure tungsten, thoriated tungsten, ceriated tungsten, lanthanated tungsten, and zirconiated tungsten.
- Pure Tungsten Electrodes (WP, Green) Known for their high level of electron emission, they provide good arc stability and are often reserved for use with AC welding of aluminum and magnesium. However, they wear out more quickly compared to their alloyed counterparts.
- Thoriated Tungsten Electrodes (WT20, Red) Offering better arc stability than pure tungsten, these electrodes contain thorium and are typically used DC applications. Known for their ease of use,
thoriated electrodes are often the choice for carbon and stainless steel welding. Despite their popularity, there are health concerns regarding thorium's radioactivity, which is why alternatives like ceriated or lanthanated electrodes are gaining traction.
- Ceriated Tungsten Electrodes (WC20, Grey) Ideal for welding at lower amperages, ceriated electrodes have proven to perform well with both AC and DC. The addition of cerium oxide increases electron emission, resulting in easier arc starting and more stable arc performance than pure tungsten.
- Lanthanated Tungsten Electrodes (WL15, Gold) These electrodes have slight versatility compared to ceriated and are considered a substitute for thoriated electrodes, with lower toxicity risks. Widely preferred in situations where a strong arc and longevity are paramount, they provide a balance across both AC and DC applications.
electrode for tig welding
- Zirconiated Tungsten Electrodes (WZ3, Brown) Renowned for their capability to withstand contamination, these electrodes are best employed in AC welding where balling occurs. They offer excellent arc stability on aluminum and magnesium alloys and prevent tungsten spitting.
2. Electrode Size and Grinding
The size of the electrode, including its diameter, should be chosen based on the thickness of the material being welded and the amperage. A larger diameter will produce more heat and is consequently used for thicker metals. Proper grinding is also necessary for sharpening the electrode; electro-grinding with precision offers a considerable advantage, as a finely ground point allows for a well-focused arc, essential for detailed work.
3. Health and Safety Considerations
The radioactivity concerns posed by thoriated electrodes underline the importance of safety when handling materials. Ensure adequate ventilation and protective gear, utilizing a comprehensive understanding of each electrode's features and drawbacks.
4. Applications and Projects
Understanding the material being worked on allows for tailored electrode use. For instance, AC welding on aluminum would benefit from a zirconiated tungsten, offering superior stability. For projects requiring deep penetration and dealing with stainless steel or nonferrous metals, lanthanated or ceriated electrodes might be optimal due to their heightened arc stability and easy start-up.
In conclusion, choosing the correct electrode for TIG welding requires a balanced understanding of material properties, electrode composition, and project goals. A welding professional can dramatically improve outcomes by leveraging these insights, ensuring that each weld meets both project specifications and safety standards. Each choice reflects not only on the quality but also on the efficiency and sustainability of the welding practice, reinforcing the importance of expert guidance in achieving top-notch results.