The use of stainless steel welding wire for MIG (Metal Inert Gas) applications, particularly the 316-grade, is pivotal in several industrial sectors. This particular welding wire is crafted for superior performance in challenging environments, thanks to its robust mechanical properties and excellent corrosion resistance.
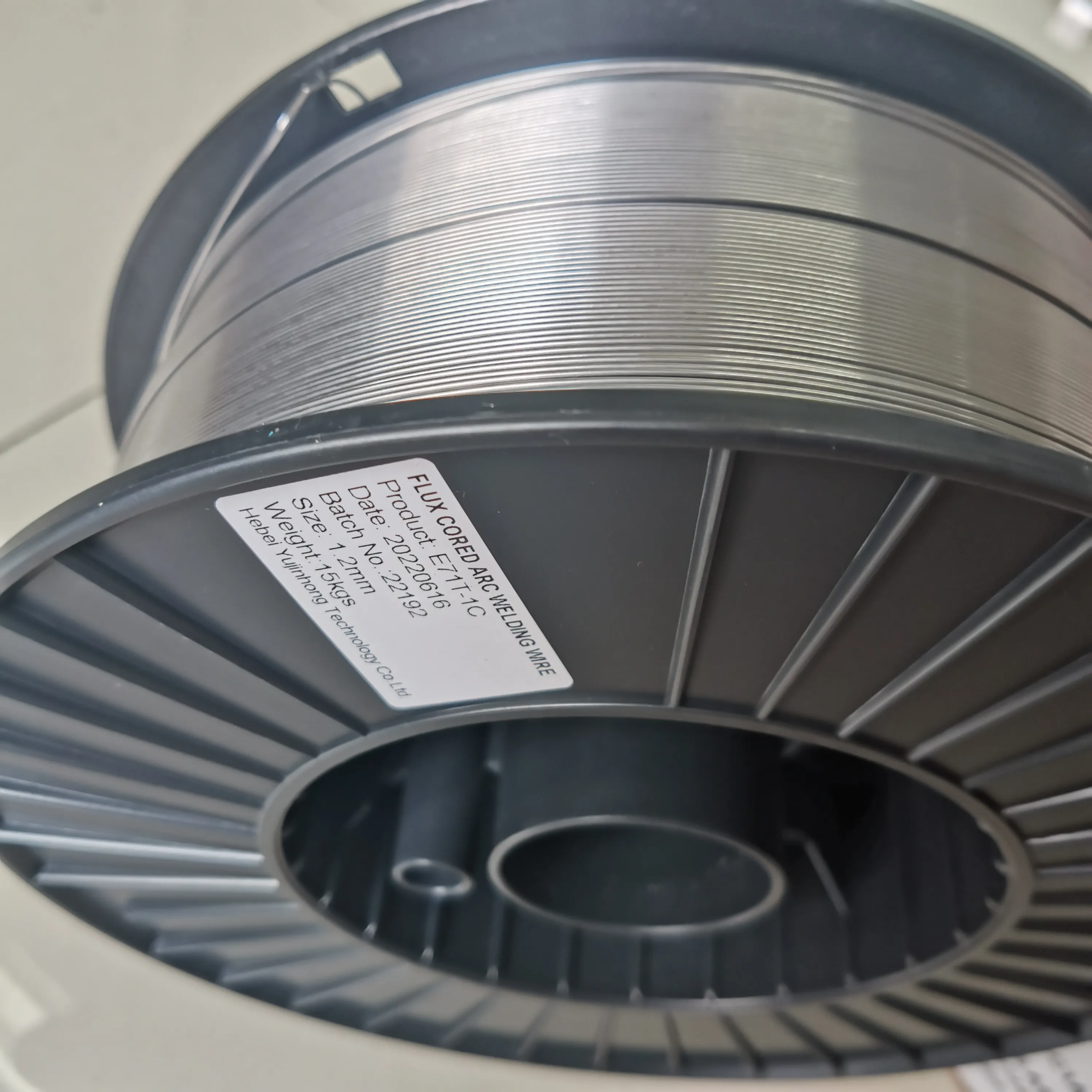
MIG 316 stainless steel welding wires are highly valued in industries where their unique properties are indispensable. One of the most celebrated characteristics of 316-grade stainless steel is its remarkable resilience to chloride environments, making it highly resistant to pitting and crevice corrosion. This makes it ideal for marine and coastal applications where exposure to saltwater can drastically degrade other materials. Engineers and fabricators working on maritime vessels, oil rigs, and underwater pipelines choose 316-grade wires for their unparalleled durability and efficiency in preventing corrosive damage.
Beyond its corrosion resistance, 316 stainless steel MIG welding wire offers excellent toughness, even at extreme temperatures. This is particularly significant in cryogenic and high-heat industrial environments. Manufacturing plants that operate under such conditions rely on the consistent performance of 316-grade welding wire to maintain the integrity and strength of their constructions, ensuring that equipment and infrastructure remain safe and reliable.
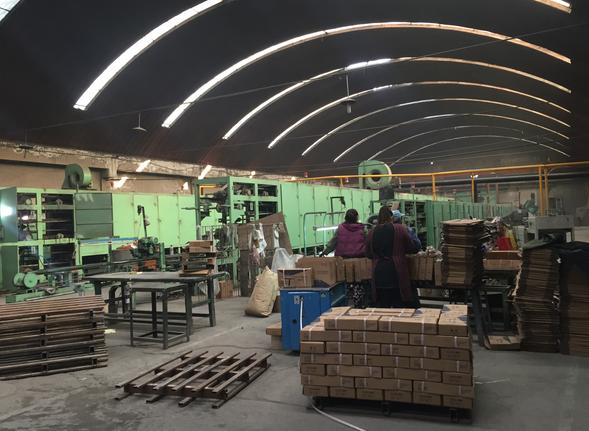
From a welding perspective, operators appreciate the usability of MIG 316 stainless steel wire. Its smooth feeding and stable arc allow for high-quality welds, which reduce the need for rework and ensure that projects are completed efficiently and on time. The uniform weld bead and minimal spatter characteristic of this wire not only enhance the aesthetic quality of the welds but also mean less post-weld clean-up, saving valuable time in large-scale manufacturing processes.
stainless steel welding wire mig 316
In terms of safety and compliance, 316 stainless steel welding wire meets stringent industry standards for both health and environmental regulations. Users can trust that when they select a high-quality MIG 316 wire, they are adhering to best practices that prioritize both worker safety and minimal environmental impact. This adherence forms the backbone of responsible manufacturing and production practices that industries are increasingly adopting worldwide.
The adaptability of stainless steel welding wire MIG 316 is another testament to its engineering excellence. It can be used with various gases like Argon with Helium, CO2, or a mix, providing flexibility that enhances its attractiveness across different applications. Fabricators can achieve consistent results across different setups, which is a crucial advantage when working on complex projects that may involve diverse materials and welding conditions.
As industries continue to evolve, the demand for reliable, high-performance materials like MIG 316 stainless steel welding wire is expected to grow. Advancements in technology, particularly in additive manufacturing and automated welding processes, are likely to expand the potential uses of this versatile material even further. Experts in material science and welding technology continually explore new frontiers, enhancing the properties and potential applications of stainless steel alloys, including the much-revered 316-grade.
Choosing the right welding wire is not just about meeting the immediate needs of a project, but also about ensuring long-term reliability and safety. With its unmatched combination of strength, resilience, and efficiency, stainless steel welding wire MIG 316 is a trusted ally for professionals across the globe who demand nothing less than the best.