Understanding the differences between MIG, TIG, and Stick welding can transform the way businesses approach fabrication and repairs, especially in sectors that demand precision, durability, and efficiency. Each welding technique has its unique features, making them suitable for different projects and materials. These methods, recognized for their specific strengths and limitations, help maintain the integrity and quality of welded structures.
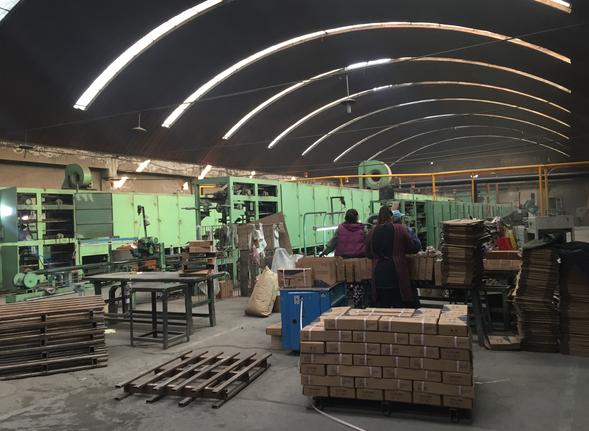
MIG welding, also known as Gas Metal Arc Welding (GMAW), is popular due to its simplicity and speed. It uses a continuously fed wire electrode and a shielding gas to protect the weld from contamination. Ideal for projects requiring efficiency, MIG welding is often used in the automotive industry, manufacturing, and construction. One of its significant advantages is producing cleaner welds with minimal spatter, making post-weld cleanup easier and less time-consuming. It's particularly effective for welding thicker metals like steel and aluminum, providing a strong, effective bond.
TIG welding, or Gas Tungsten Arc Welding (GTAW), stands out for its precision and control. It utilizes a non-consumable tungsten electrode, and unlike MIG welding, it often requires a filler rod. This technique is perfect for projects where detail and aesthetic quality are paramount. Industries such as aerospace, art installations, and high-end automotive restorations frequently depend on TIG welding. Its precision makes it suitable for thinner materials and for working on stainless steel, titanium, and copper alloys. The downside, however, is that it requires more skill and patience, resulting in slower production times.
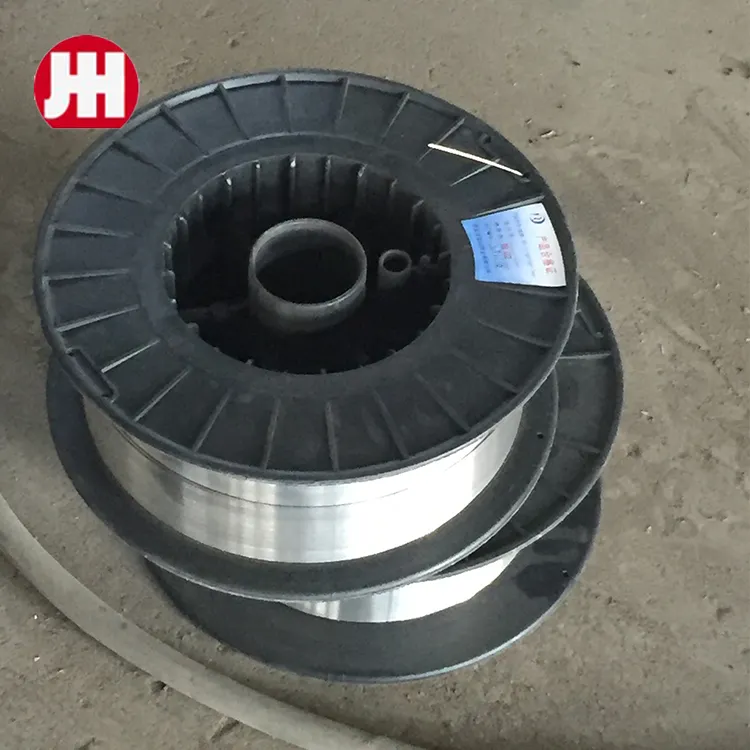
Stick welding, technically termed Shielded Metal Arc Welding (SMAW), is valued for its versatility and portability. It employs a consumable electrode coated in flux to lay the weld, which makes it less reliant on external shielding gas, an advantage in outdoor or windy environments. The robustness of stick welding makes it suitable for construction, pipelines, and heavy equipment repair. It is particularly effective with iron and steel, including cast iron and stainless steel.
Despite being less tidy than MIG and TIG welding, stick welding is favored for its adaptability to less controlled work settings.
mig tig and stick welding
When choosing between MIG, TIG, and Stick welding, consider the material type, project requirements, and environmental conditions. MIG welding offers a quick and clean solution for mass production on heavy materials, while TIG welding ensures delicate precision, ideal for thin metals and detailed artistry. Stick welding provides robustness and adaptability, especially beneficial in undeveloped settings.
Incorporating these welding techniques with a deeper understanding of their strengths can significantly enhance the production process. Each method plays a pivotal role in creating durable, high-quality welds, ensuring longevity and reliability in each product. Consequently, investing in the right welding technology and expertise directly correlates with the quality and efficiency of the final product, making these welding techniques invaluable tools in industry expertise.
Forward-thinking companies that understand and implement these processes benefit from improved product reliability and customer satisfaction. Expertise in these welding techniques not only builds credibility and reputation but also ensures that businesses meet and often exceed industry standards, firmly establishing themselves as authorities in their fields. In conclusion, mastering MIG, TIG, and stick welding provides a competitive edge, characterized by product excellence and service reliability, which are crucial for maintaining and building market trust.