Rod welding stainless steel stands as a crucial aspect in the fabrication and repair industry. Stainless steel, known for its corrosion resistance, aesthetic appeal, and strength, requires precise techniques and knowledge for welding tasks. Here, we delve into the nuanced world of rod welding stainless steel, uncovering expert insights and providing authoritative guidance to enhance your projects.
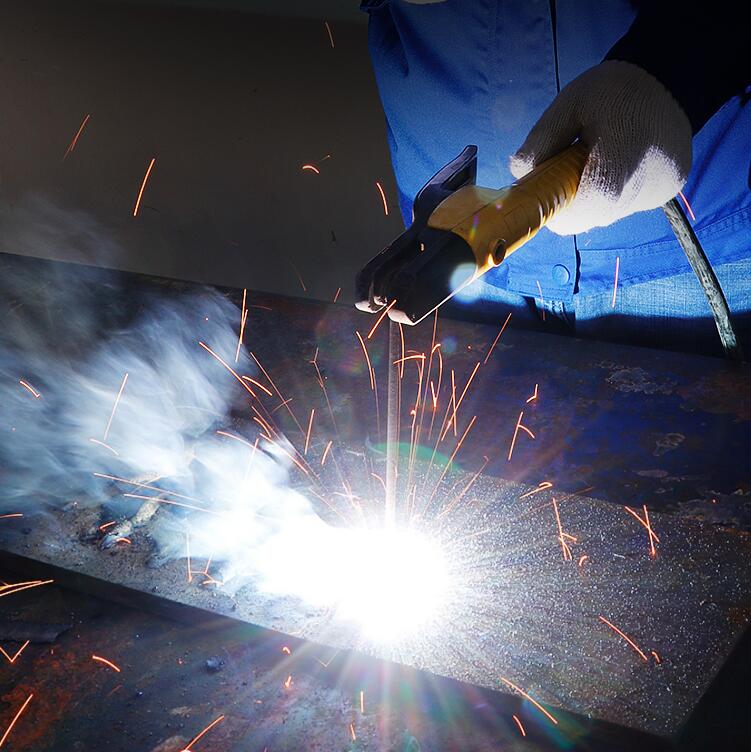
Firstly, understanding the material's characteristics is paramount. Stainless steel, an alloy with at least 10.5% chromium, forms a self-repairing oxide layer that resists rusting and corrosion. This property, however, makes it more challenging to weld compared to other metals such as carbon steel. The coefficient of thermal expansion is notably high, meaning welders must account for potential warping or distortion during the welding process.
Selecting the appropriate welding rod is critical. For stainless steel, rods must be chosen based on the stainless alloy being welded. For instance, the E308L rod is widely used for 304 stainless steel, one of the most common stainless alloys. Its low carbon content minimizes carbide precipitation, reducing the risk of intergranular corrosion.
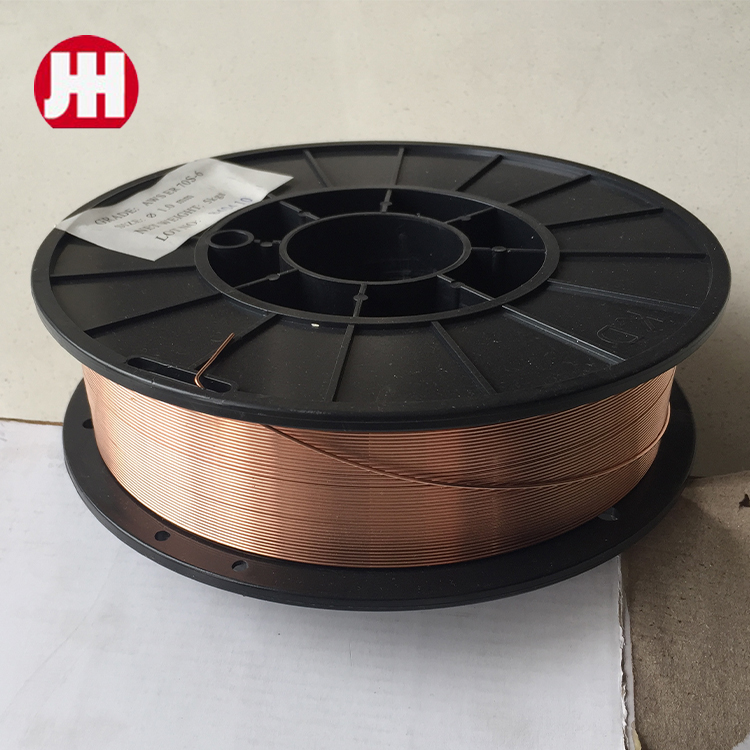
Preparation is equally crucial. Cleaning the surfaces to remove contaminants such as dust, oil, and fingerprints can prevent inclusions and weld defects. A clean joint ensures a strong weld and maintains the stainless steel’s corrosion-resistant properties. Mechanical or chemical cleaning methods may be deployed, depending on the scale and requirements of the project.
The welding process itself demands precision. Techniques such as TIG (Tungsten Inert Gas) welding are preferred for stainless steel due to the control it offers over the heat input. This method also helps in maintaining the stainless steel's properties by reducing oxidation. The choice of shielding gas also plays a significant role, with argon or a mix of argon and helium being preferred for their ability to produce clean, high-quality welds.
rod welding stainless steel
Post-welding treatment cannot be overlooked. The heat from welding can alter the chromium oxide layer, especially if proper procedures aren’t followed. Acid passivation may be employed to restore and enhance corrosion resistance by dissolving iron contaminants and promoting the formation of a chromium-rich oxide layer.
Furthermore, expertise in rod welding stainless steel involves understanding and minimizing potential pitfalls. Among these are hot cracking, which can occur if the weld cools too quickly, and sensitization, where areas near the weld become prone to corrosion. Advanced techniques, including preheating and controlling the cool-down rate, can mitigate these issues.
Trust and authority are built on experience and adherence to best practices. Professionals in the field, whether fabricators or repair technicians, continually update their skills and techniques to ensure high-quality outcomes. Certifications and adherence to industry standards, such as those from the American Welding Society (AWS), underpin both competence and credibility.
Lastly, ongoing innovations and research contribute to the evolving landscape of welding technology. Advances in filler materials, welding machines, and procedural guidelines expand the possibilities and efficiencies achievable in stainless steel welding. Participating in workshops, continuous learning, and engaging with the welding community are ways professionals maintain a competitive edge.
In summary, rod welding stainless steel requires a thorough understanding of the material, meticulous preparation, and an execution grounded in expertise. By embracing best practices and remaining aware of technological advancements, welding professionals not only ensure superior project outcomes but also build a reputation grounded in authority and trustworthiness. These elements, combined, deliver unparalleled performance and longevity in stainless steel applications.