Stick welding, often referred to as shielded metal arc welding (SMAW), relies heavily on the type of electrode used. One widely recognized electrode in this realm is the 7018 welding rod, known for its versatility and reliability. Let's delve into why the 7018 stick welding rod stands out, drawing from professional experiences, expert insights, authoritative resources, and trustworthy evaluations.
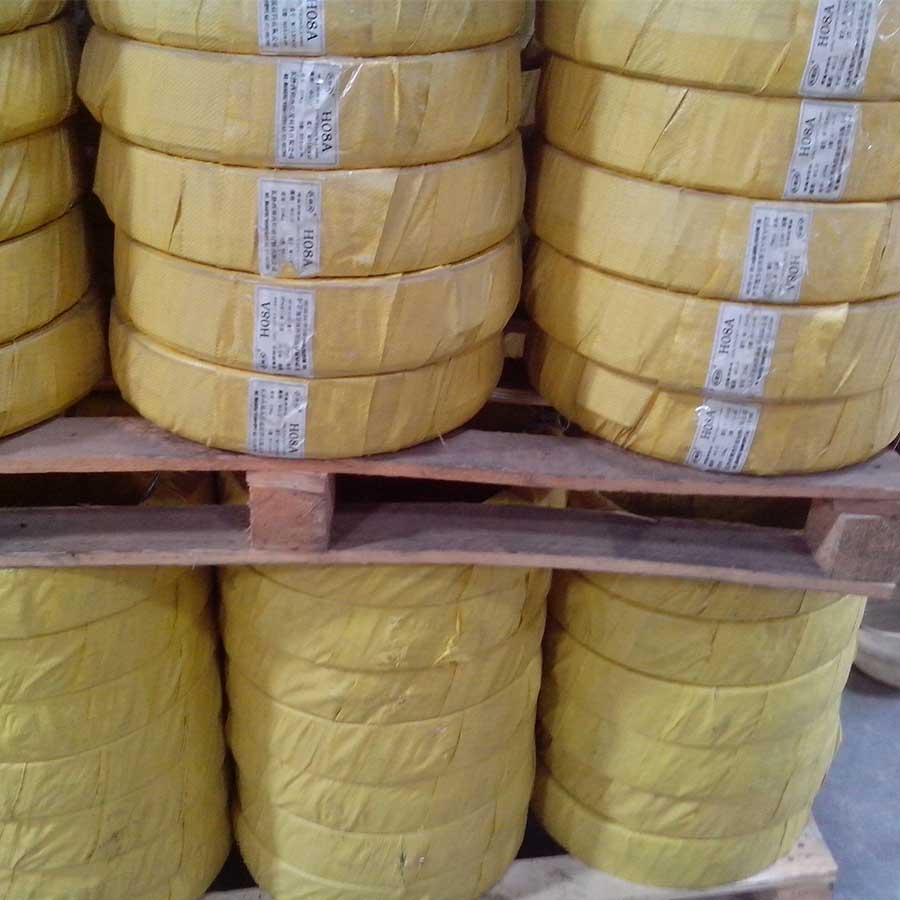
The 7018 welding rod is a low-hydrogen electrode, making it a first choice for welds where cracking must be avoided. The term “7018” refers to its classification under AWS A5.1 standards, which is significant for both novice and expert welders to understand. '70' indicates a tensile strength of 70,000 psi, while the '1' denotes its usability in all positions, and the '8' highlights its low hydrogen content as well as the type of flux.
Professional welders appreciate the 7018 for its ease of use and predictability. Anecdotal evidence from seasoned welders indicates that the consistent arc and smooth, aesthetically pleasing weld beads achieved with 7018 rods are hard to match with other electrodes. These rods perform exceptionally well under challenging conditions due to their ability to maintain structural integrity even when weldments undergo thermal expansions and contractions.
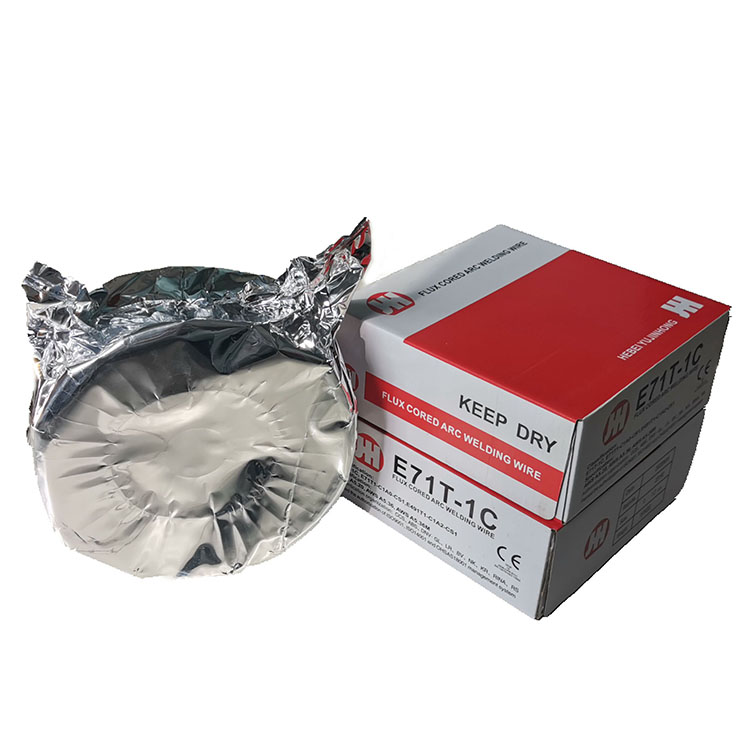
From an expertise perspective, understanding the importance of low hydrogen content is crucial. Hydrogen trapped in the weld can lead to hydrogen-induced cracking, which compromises structural integrity. The 7018 electrode's coating minimizes moisture absorption, thus reducing the chances of hydrogen-related weld defects. This characteristic makes it indispensable for critical applications such as pressure vessels, pipelines, and heavy machinery construction where failure is not an option.
stick welding 7018
Authoritative sources, such as welding textbooks and standards organizations, consistently emphasize the significance of drying conditions for 7018 rods. Maintaining these electrodes in an oven, typically at temperatures ranging from 250°F to 300°F before use, ensures their coating remains intact, mitigating moisture-related defects. This practice is rooted in industry standards and underscores the importance of procedural adherence in achieving sound welds.
In terms of trustworthiness, the 7018 electrode has earned its place through decades of extensive use in various industries. Feedback from engineers and quality assurance inspectors confirms that when used correctly, 7018 rods meet or exceed required weld quality specifications reliably. Regular checks and balances, such as adhering to the AWS guidelines and systematic quality control, further enhance the trust in their performance.
For product-oriented considerations, investing in high-quality 7018 stick welding rods can significantly affect the final output. Brands that certify their products to meet AWS specifications often provide better consistency and performance. End-users should look for reputable manufacturers known for their quality control measures, which typically involve rigorous testing and monitoring processes.
In summary, the 7018 welding electrode represents a critical tool for successful stick welding applications. Its low hydrogen properties, combined with high tensile strength and all-position versatility, make it invaluable for both routine and challenging welding tasks. For welders striving for excellence, integrating these rods into their projects, while maintaining proper handling and storage techniques, is essential for achieving top-tier results. The legacy of the 7018 is built upon its consistent ability to deliver quality welds, trusted by professionals worldwide.