Welding is more than just a technical skill; it's a craft that demands precision, expertise, and a deep understanding of materials and techniques. Among the myriad of welding processes, vertical stick welding using 7018 electrodes stands out for its unique challenges and applications. This method is widely acclaimed in the construction and manufacturing industries for its robust and reliable welds, especially in projects requiring vertical joints.
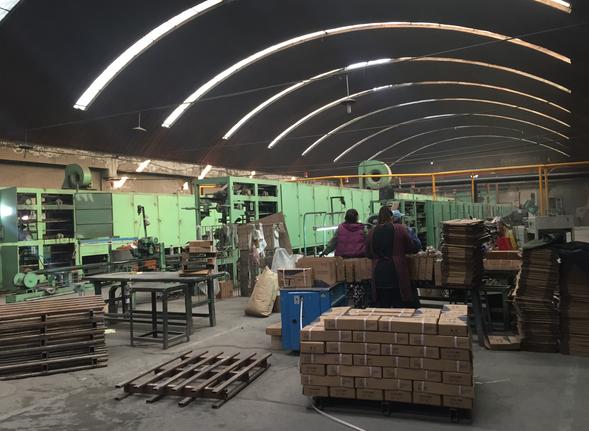
Vertical stick welding, often referred to as shielded metal arc welding (SMAW), involves mastering the gravity-defying techniques required to produce strong, defect-free welds. The 7018 electrode is particularly renowned for its low-hydrogen characteristics, which mitigate the risk of weld cracking due to hydrogen embrittlement — a common concern in vertical or overhead positions.
Experience is paramount in mastering vertical stick welding. Novices often struggle with the nuances of controlling the molten pool and maintaining uniformity in bead appearance. Achieving proper penetration without excessive spatter is crucial. Seasoned welders often emphasize the importance of maintaining a consistent arc length and adjusting the angle of the electrode to accommodate the direction of weld travel. A slight drag angle is often recommended, as it can help control the flow of the molten pool and prevent the formation of undercuts.
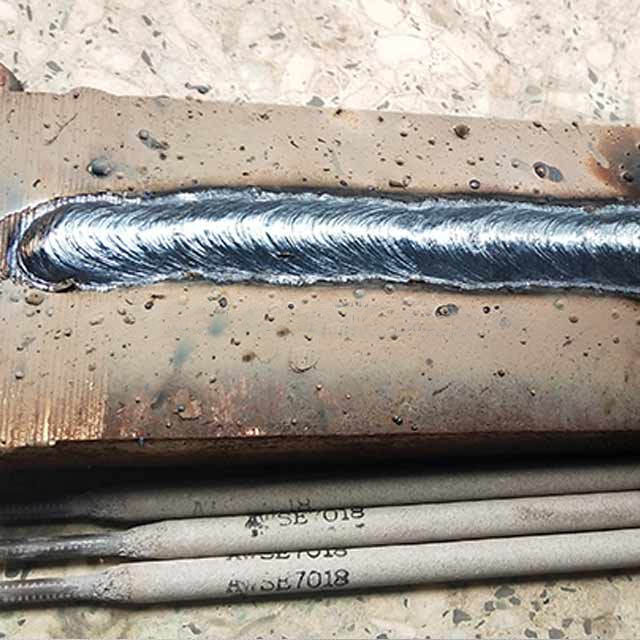
From an expertise perspective, understanding the properties and composition of 7018 electrodes is critical. These low-hydrogen electrodes contain an iron powder in their coating, which enhances their deposition rate, making them ideal for filling large joints. The 7018 electrode operates efficiently on both AC and DC+ currents, offering flexibility in different welding setups. Mastery of the proper techniques ensures that the welds are not only structurally sound but also meet stringent industry standards and specifications.
vertical stick welding 7018
Building authoritativeness in the field involves recognizing the wide range of applications and limitations of vertical stick welding with 7018 electrodes. These electrodes are often used in heavy structures, such as bridges and high-rise buildings, where the integrity of the weld is paramount. They are also favoured in repair and maintenance works, where existing conditions are less than ideal, and the risk of contamination is high. Demonstrating a profound understanding of how the 7018 performs under various environmental conditions, such as extreme temperatures or corrosive environments, further establishes authority.
Trustworthiness in the world of welding is earned through consistent, reliable performance and adherence to safety standards. The 7018 electrode requires proper storage and handling, as exposure to moisture can compromise its low-hydrogen qualities. Welders need to ensure that electrodes are kept in moisture-free environments and consider using rod ovens to maintain optimal conditions. Providing guidance on best practices for storage, as well as showcasing successful projects where vertical stick welding with 7018 electrodes was employed, instills confidence and demonstrates reliability.
Professionals seeking to enhance their welding craft must not only hone their physical technique but also stay informed about advancements in electrode technology and welding machinery. Continuous learning through certifications and attending workshops and seminars is essential in staying competitive and delivering superior results.
In conclusion, vertical stick welding with 7018 electrodes is a challenging yet rewarding endeavor. It requires a profound synthesis of experience, expertise, authority, and trustworthiness, all of which contribute to achieving impeccable weld quality. Welders who master this technique are invaluable assets to their industries, providing the backbone for structures that define our skylines and shape our world.