Choosing the right MIG welder wire can significantly impact your welding experience and the quality of your final product. With years of experience in metalworking and welding, I understand the nuances that go into selecting the best wire for specific applications, and I’m here to share insights into making an informed choice backed by expertise, industry authority, and trustworthiness.
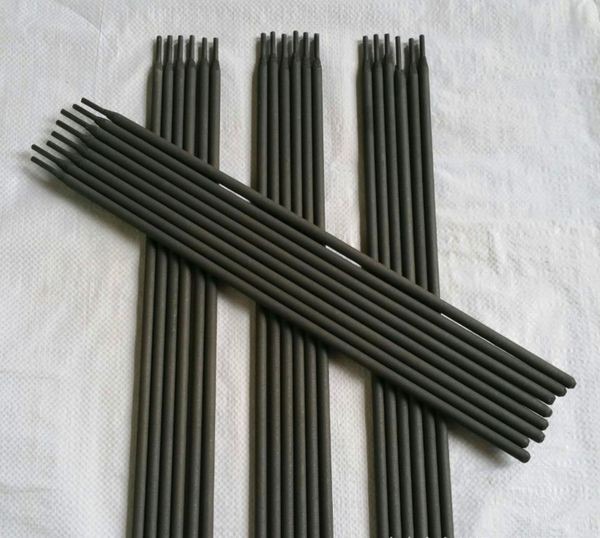
Firstly, understanding the composition of MIG welder wire is fundamental to comprehending its performance. MIG wire is typically made from mild steel, stainless steel, or aluminum, each serving distinct purposes based on the materials being welded. Mild steel wire is cost-effective and versatile, making it a popular option for everyday welding. Stainless steel wire, though more expensive, resists corrosion and provides excellent strength; while aluminum MIG wire is ideal for lightweight, non-magnetic welding projects. Your decision regarding the wire material will largely depend on the project specifications and the base metals being worked on.
When it comes to MIG wire sizes, commonly referred to by their diameter (such as .023, .030, .035, .045), the choice affects both the arc stability and the metal deposition rate. For example, thinner gauges, like .023, are suitable for sheet metals and autobody work where less penetration is needed. In contrast, .035 wire offers a higher deposition rate that is beneficial for thicker materials and structural applications. Experts suggest starting with .030 wire for general use, as it provides a versatile balance between speed and control.
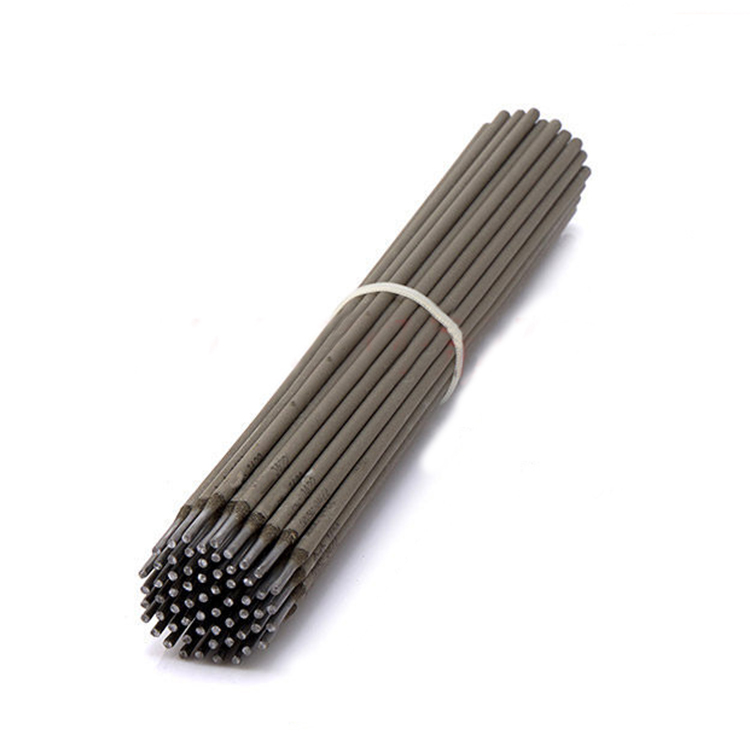
Furthermore, the type of shielding gas used in conjunction with your MIG wire plays a crucial role in achieving quality welds. For mild steel applications, a popular choice is the C25 gas mix (25% CO2 and 75% Argon), which provides a clean weld bead with minimal spatter. Conversely, using pure CO2 can be more cost-effective and delivers deeper penetration, though it may cause more spatter.
mig welder wire
Equally significant is the consideration of welder settings. I recall a challenging project where adjusting the voltage and wire feed speed was instrumental in achieving optimal weld quality. Employing a higher voltage typically allows for better penetration, essential for welding thicker materials, while moderate voltage settings are suitable for thinner gauges. Additionally, fine-tuning the wire feed speed to match the material and thickness ensures a stable arc and adequate penetration.
It is crucial to consider the manufacturer’s reputation when selecting MIG welder wire. Established brands like Lincoln Electric, ESAB, and Hobart provide assurance of quality control and consistent performance. Over the years, I've found that investing in premium wires from trustworthy brands reduces the incidence of defects such as inconsistent bead appearance or unexpected porosity.
Lastly, factor in the environment where the welding occurs. Training seminars and fieldwork experiences have repeatedly demonstrated the impact of environmental conditions on weld quality. In outdoor or drafty environments, flux-cored wires, which don’t require a shielding gas, equip a MIG welder to produce better results despite adverse conditions.
Choosing the right MIG welder wire is as much an art as it is a science, necessitating a blend of practical experience and technical knowledge. The considerations of wire composition, size, shielding gas, manufacturer, and environmental factors constitute the core of making an informed decision. By heeding these expert insights, welders can ensure precision, quality, and efficiency in their welding projects, fostering trust and authority in their craft.