Choosing the right welding wire for your projects is crucial to achieving optimal results, particularly when considering the specifications such as diameter and material. The 0.030 welding wire, a common choice across various applications, offers a perfect balance between ease of use and weld quality, making it a go-to choice for both amateur and professional welders. This article delves into the specifics of the 0.030 welding wire, its applications, and benefits while ensuring that you have the most precise and trustworthy information to guide your purchasing decisions.
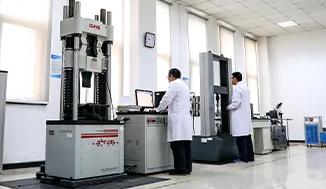
The 0.030 welding wire, often used in metal inert gas (MIG) welding, strikes an ideal balance between thickness and control. This wire size provides optimal control for detailed and delicate welds, where precision is paramount. Its relatively thin diameter allows for smoother feeding through the welding gun, reducing the risk of wire jamming — a common issue in welding that can disrupt workflow and cause potential defects in the weld. This feature makes it a favorite among hobbyists and professionals who seek efficient workflow and high-quality results.
When choosing a welding wire, considering the material is as important as the diameter. The 0.030 size is compatible with a variety of material options like stainless steel, mild steel, and aluminum. Each material has distinct properties, impacting the application and the final outcome of the weld. For instance, a mild steel 0.030 wire is often praised for its versatility across construction and automotive repairs due to its strong welds and affordability. In contrast, a stainless steel 0.030 wire is preferred for projects requiring rust and corrosion resistance, such as in food processing or marine environments.
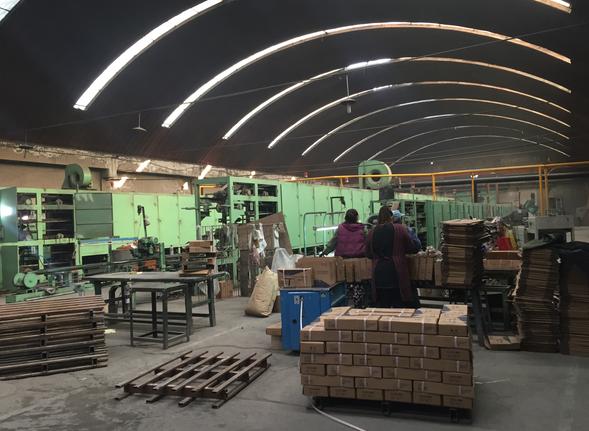
The versatility of the 0.030 welding wire extends to its application settings. In automotive repair, it facilitates detailed and precise welding on thinner materials, where material distortion and burn-through are concerns. Its precision enables welders to repair body panels and structural components effectively. Additionally, in household and small-scale projects, this wire size helps in achieving clean and attractive welds on materials such as fencing, furniture frames, or decorative metal features, with minimal post-welding cleanup required.
Professional welders often note the economic value of 0.030 welding wires. Due to its size, it is efficient in wire consumption, reducing wastage and consequently lowering overall material costs. For businesses, this efficiency translates to increased productivity and reduced overheads, a critical factor for profitability in competitive industries. The precision and control that come with this wire size reduce the need for revisits and reworks, thus saving time and labor costs.
0.030 welding wire
Trust in a product often grows from its reliability and performance, both attributes found in the 0.
030 welding wire. Expert welders often stress the importance of choosing reputable brands that adhere to industry standards, as these wires have undergone rigorous testing to guarantee consistent performance and safety. Brands that follow ISO standards, for instance, ensure that the wires maintain uniform diameter throughout the coil, a factor that significantly influences the quality of the weld.
In terms of welding setups, the 0.030 wire is highly adaptable. It performs exceptionally well with both basic welding machines used by hobbyists and advanced equipment found in commercial workshops. The ability to fine-tune feed rates and voltage settings with this wire makes it suitable for both beginners and seasoned welders, offering a smoother learning curve for newcomers and precise adjustments for complex projects.
Finally, the future of welding is leaning heavily towards sustainable practices, and this is another area where the 0.030 welding wire shines. Its precision reduces spatter and subsequent metal wastage, contributing to environmentally friendly welding practices by minimizing waste. Innovators in the welding industry are constantly improving alloy compositions and wire coatings to further this cause, ensuring each weld is as efficient and sustainable as possible.
In conclusion, the 0.030 welding wire embodies a blend of versatility, reliability, and cost-efficiency that is hard to match. Its precise application across various materials and projects, supported by industry-leading standards, makes it an invaluable tool for welders seeking to deliver quality work consistently. Whether used in small-scale endeavors or large industrial applications, this wire size contributes significantly to the advancements in welding technology and practices, reinforcing its role as a staple in the welding community.