For welding professionals and enthusiasts seeking unparalleled performance in stainless steel projects, 316L welding wire emerges as an indispensable component. This high-quality wire, renowned for its corrosion resistance and durability, serves as a cornerstone in various industries, including construction, automotive, and medical manufacturing. With an in-depth exploration into its unique properties, applications, and benefits, we delve into the expertise behind 316L welding wire and uncover its essential role in delivering premium results.
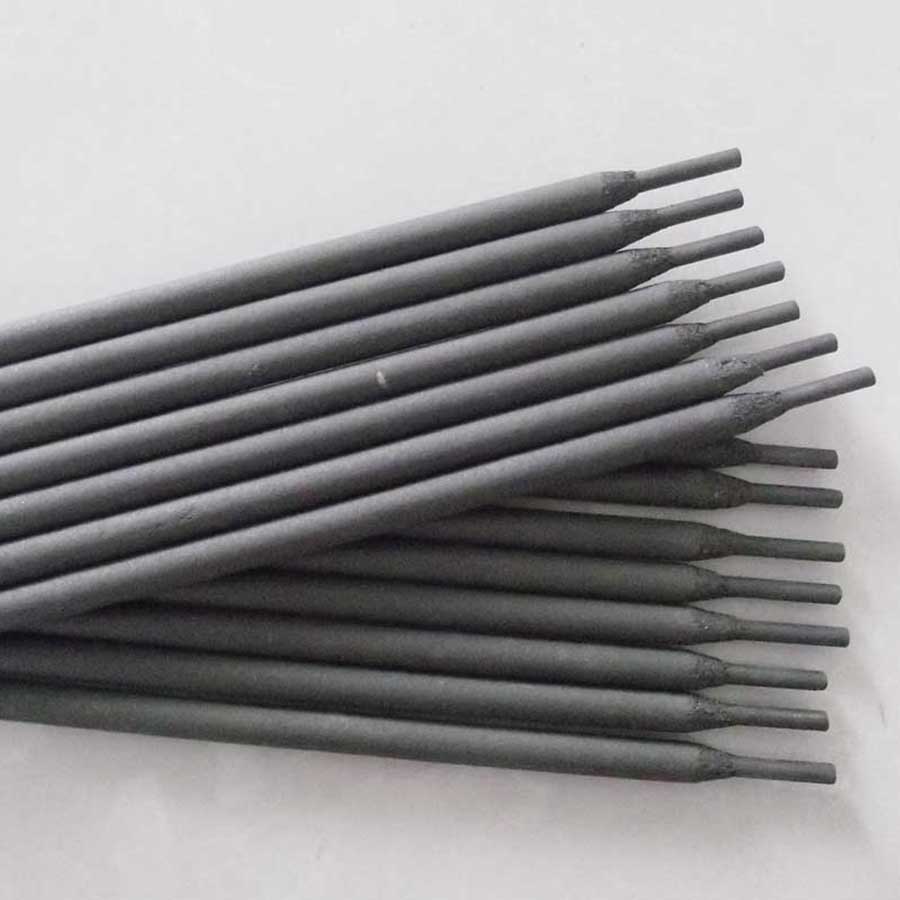
316L welding wire is crafted from a low-carbon version of the 316 alloy, making it a preferred choice for environments where corrosion and oxidation are significant concerns. Unlike other types of welding wire, 316L boasts exceptional resistance to chlorides and other industrial chemicals, which positions it as an authoritative material in marine and chemical processing applications. The low carbon content minimizes carbide precipitation during welding, enhancing its corrosion resistance, especially in the heat-affected zones.
The expert craftsmanship in producing 316L welding wire ensures superior mechanical properties. It offers remarkable tensile strength and thermal conductivity, which are critical for maintaining the structural integrity of welds under various stress conditions. This expertise is validated through rigorous industry standards and certifications, providing assurance of the wire's quality and performance capabilities. Professionals in the field rely on 316L for its proven track record, which translates to trustworthy and long-lasting welds.
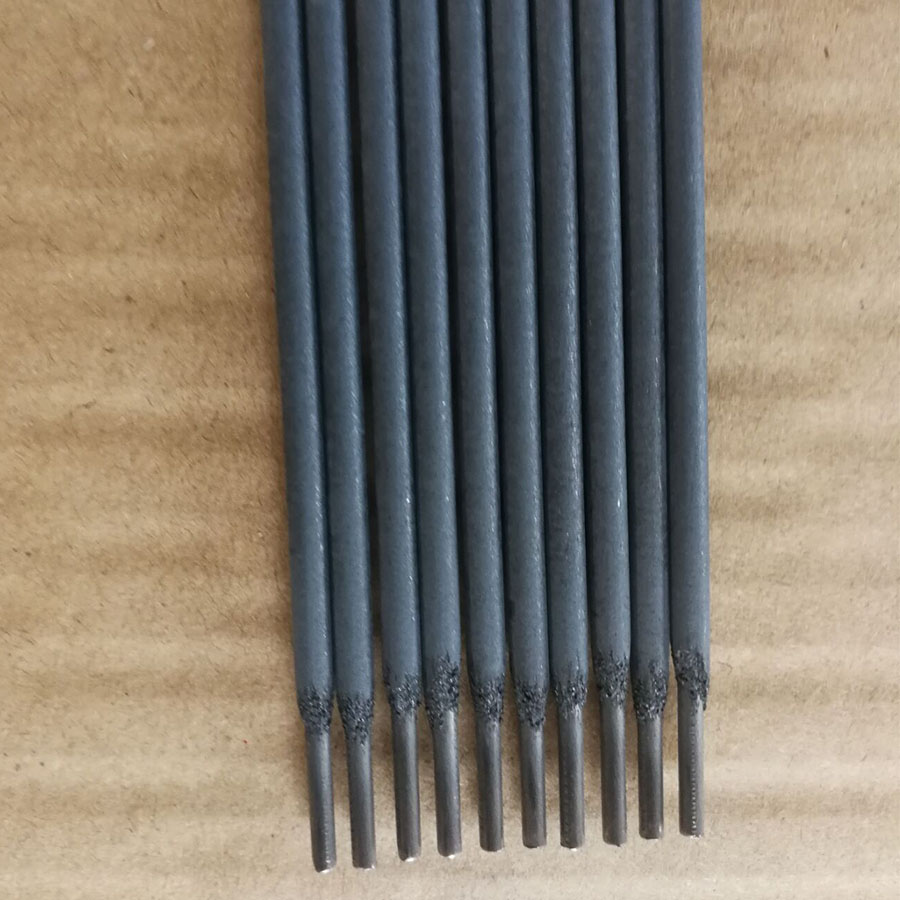
Experience in utilizing 316L welding wire unveils its flexibility across multiple welding processes, including GTAW (Gas Tungsten Arc Welding), GMAW (Gas Metal Arc Welding), and SAW (Submerged Arc Welding). Each technique benefits from 316L’s adaptable nature, ensuring that the precise requirements of different projects meet their targets efficiently. Welders experienced with 316L appreciate its ability to produce smooth and clean welds, reducing the need for extensive finishing work and thus improving productivity and cost-effectiveness.
316l welding wire
An authoritative voice in 316L welding wire emphasizes the importance of selecting the right filler material for welding stainless steel components. Given its heightened corrosion resistance and strength, it is particularly effective in fabricating vessels and equipment that are subjected to harsh environments. Its widespread trust is further highlighted by the endorsements from leading manufacturers and certifications from renowned quality assurance bodies.
The trustworthiness of 316L welding wire stems from its extensive testing and validation across a range of applications. Manufacturers conduct thorough inspections to ensure optimal performance under diverse conditions, which solidifies its reputation as a reliable choice for critical welds. The longevity of the wire's functionality reaffirms its status as a dependable solution, safeguarding infrastructure and machinery from premature wear and tear.
Professionals gravitating towards 316L welding wire can attest to its seamless application, enhancing both small-scale projects and large industrial tasks. The wire’s dependable performance in constructing high-pressure tanks, pipelines, and architectural structures makes it invaluable in industries demanding precision and reliability. Trust is reinforced through every successful application, where the quality of a well-performed weld speaks volumes about the material's efficacy.
In conclusion, 316L welding wire represents a synthesis of experience, expertise, authoritativeness, and trustworthiness. Its specialized composition and proven durability underscore its critical role in achieving excellence in stainless steel welding. Choosing 316L is not merely a material selection; it’s an investment in enduring quality and performance that meets the rigorous demands of today’s innovative projects. Welding professionals draw upon their experience with 316L to deliver superior craftsmanship that upholds the highest standards of safety and effectiveness.