Investing in the right welding wire is crucial for any fabrication or construction project demanding high-end corrosion resistance and durability. Among the plethora of materials available, 316 stainless steel welding wire stands out as an expert's choice due to its superior attributes. Praised for its impressive resistance to corrosion, particularly in marine environments and in the presence of chlorides, this alloy is a staple for professionals who prioritize longevity and quality in their projects.
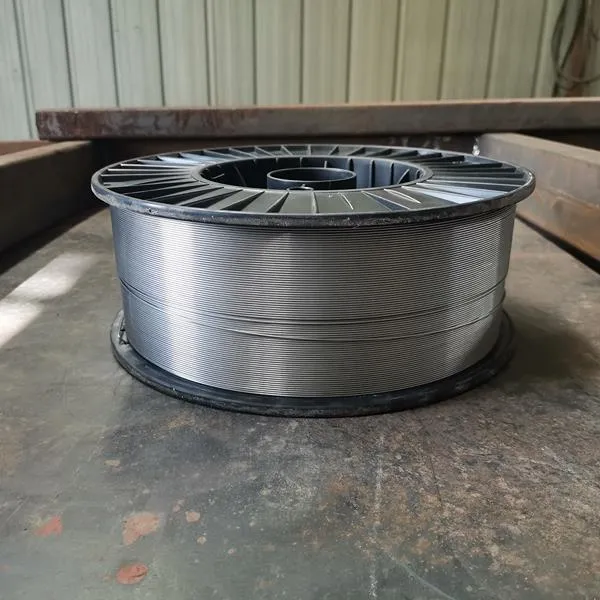
316 stainless steel welding wire is embedded with molybdenum. This element is the game-changer that enhances its capability to withstand severe corrosion conditions, distinguishing it from its counterparts like 304 stainless steel. This makes it particularly useful in industries such as chemical processing, food and beverage, and pharmaceuticals, where exposure to corrosive substances is prevalent. The expanded resistance to pitting corrosion is a critical factor for structures in chloride-heavy environments, such as coastal regions and salty aqueous environments.
The welding process with 316 stainless steel wire is not just about ensuring joints are secure—it's about ensuring those joins last in challenging environments. Skilled welders appreciate this alloy for its workability, even if they encounter varied welding processes such as TIG (Tungsten Inert Gas) or MIG (Metal Inert Gas). On-site professionals attest to the consistency of the welds it provides and the relative ease in achieving those welds with minimal defects. This not only heightens the material's trustworthiness but also its appeal amongst skilled craftsmen who deliver the finest of finishes. Its substantial resistance to intergranular corrosion post-welding, without compromising the mechanical properties, further establishes its authority among materials.
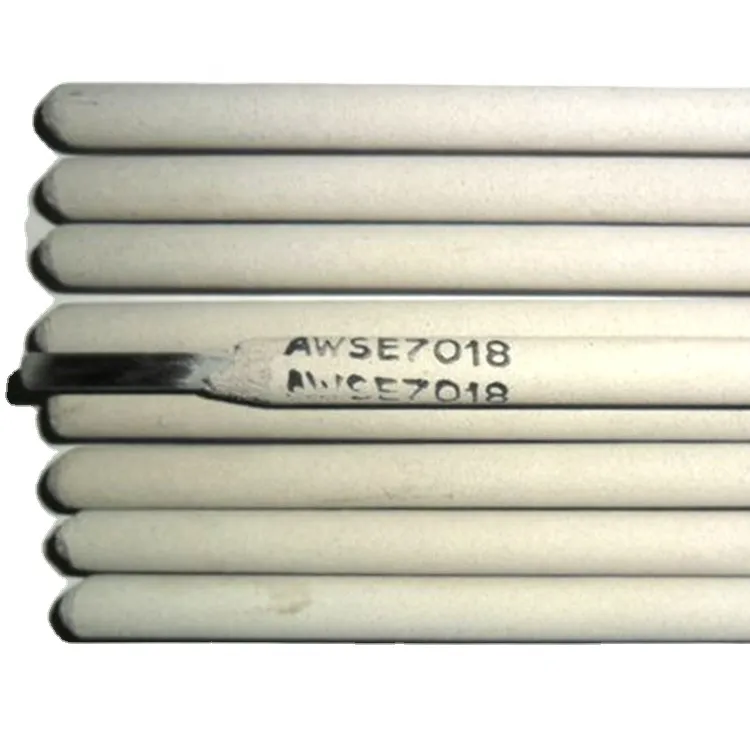
Expertise in welding with 316 stainless steel wire involves understanding the nuances of its behavior under heat. Effective welders know controlling heat input is paramount to prevent distortion and maintain structural integrity. The authoritative knowledge surrounding heat management, along with thorough post-weld cleaning procedures, can dramatically extend the lifetime of a structure. It's an insightful practice to use high-purity shielding gases to achieve optimum weld quality and avoid contamination during the welding process.
316 stainless welding wire
Professionals who have solid experience with 316 welding wire often share anecdotes of its resilience over decades of exposure and the economic efficiencies achieved from fewer repairs and replacements. Opting for 316 over inferior grades can result in substantial savings and enhanced performance, based on its enduring robustness. Decision-makers in construction and manufacturing spheres find added value in these experiences, which reiterate the wire's real-world applicability and benefits.
Furthermore, the authority of 316 stainless steel welding wire is solidified by its compliance with numerous international standards, underscoring its credibility in global markets. This conformity ensures that 316 stainless steel wire meets rigorous performance specifications that trade professionals can rely on, knowing it will perform consistently regardless of geopolitical variances.
Choosing 316 stainless steel welding wire is an investment in excellence. For professionals focused on delivering uncompromising quality, this alloy’s impressive features speak volumes. The accumulated experience, evidence of unparalleled endurance in corrosive environments, and adherence to professional standards render it an authoritative choice. Welcoming this expert-endorsed welding wire into your projects not only fortifies the integrity of your work but also reinforces trust and longstanding reliability in your capabilities as a manufacturer, constructor, or fabricator. Embrace the confidence that comes with employing an industry-recognized material and secure your projects against the harshest of conditions with 316 stainless steel welding wire.