The use of stainless steel MIG wire has become a cornerstone in industries demanding high-quality welding outcomes. This wire is indispensable in sectors such as automotive, aerospace, construction, and manufacturing due to its corrosion-resistant properties and excellent welding characteristics. Understanding the nuances of stainless steel MIG wire can significantly enhance the welding process, ensuring structurally sound and aesthetically pleasing results.
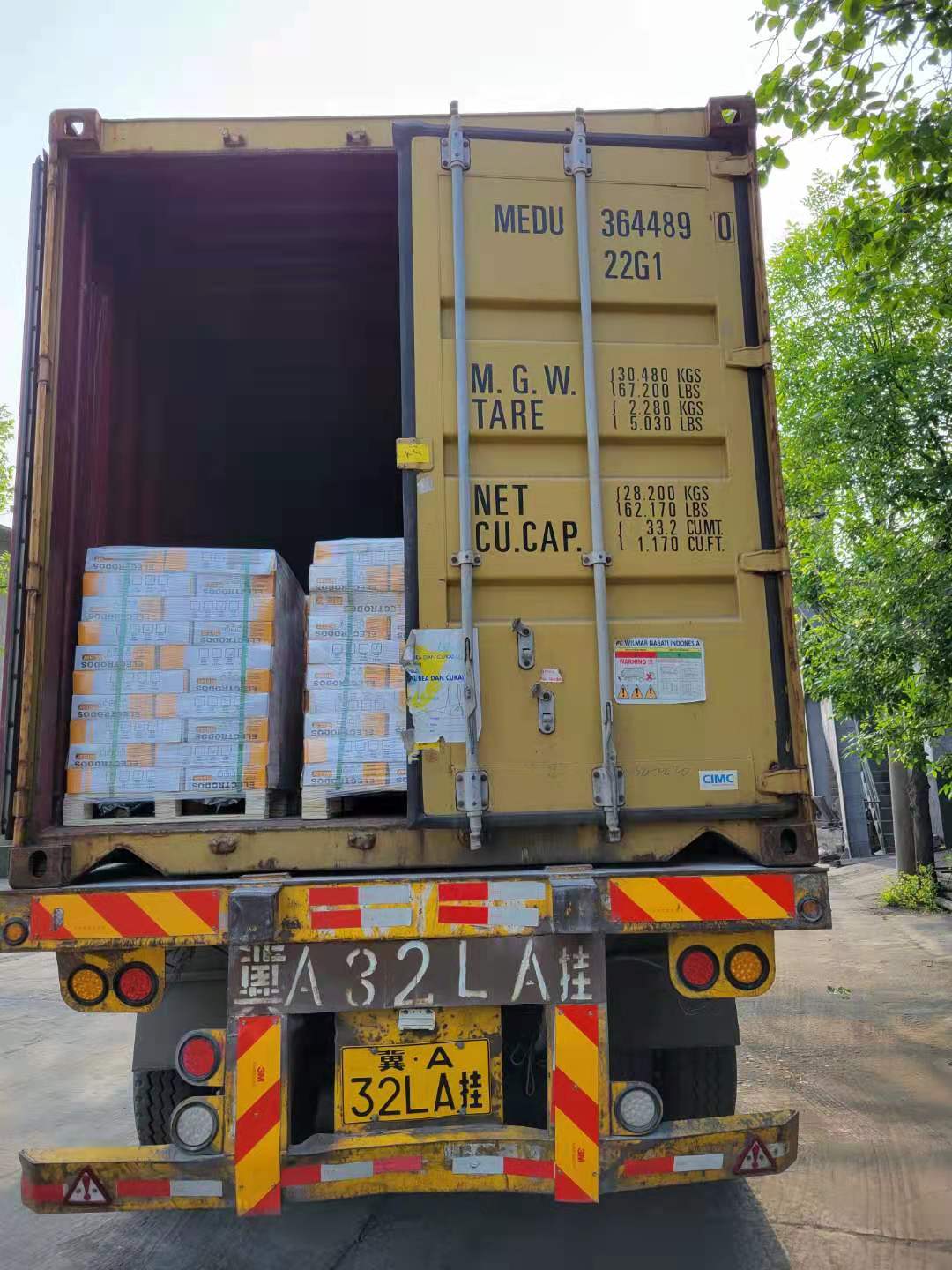
Stainless steel MIG wire is primarily valued for its ability to provide a clean and robust weld without compromising the parent metal's integrity. This is crucial in industries where material durability and finish quality are non-negotiable. With its higher resistance to heat and oxidation, stainless steel MIG wire ensures that the welded joint remains intact even in challenging environments, enhancing the longevity of the finished product.
The versatility of stainless steel MIG wire is unrivaled. It is available in various grades and alloys, each designed to cater to specific welding requirements. For instance, Type 308 stainless steel MIG wire is commonly used for general stainless steel welding, offering a smooth bead and excellent fusion characteristics. Meanwhile, Type 316 provides superior performance in highly corrosive environments, such as marine applications, due to its enhanced molybdenum content.
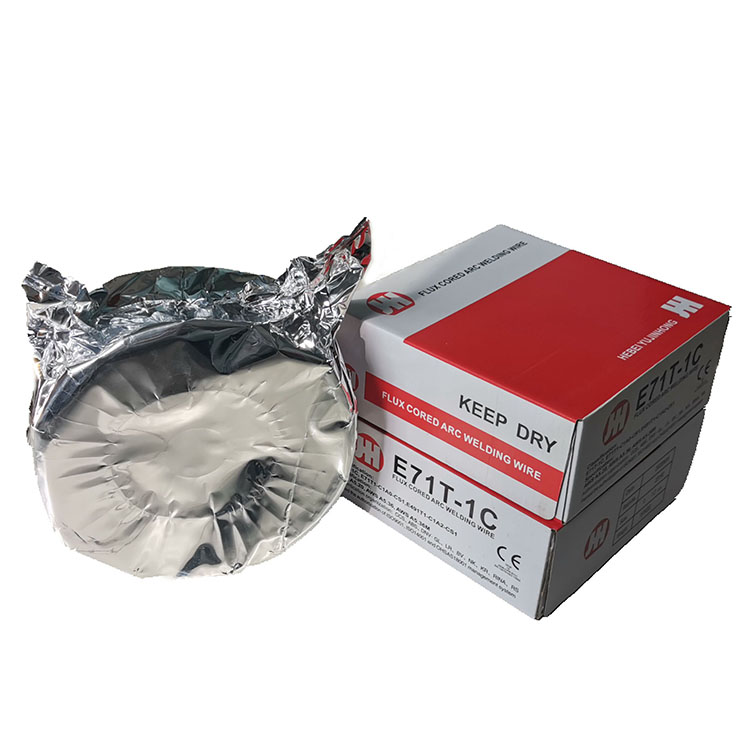
Selecting the right stainless steel MIG wire involves understanding the base material and the conditions the final weld must withstand. Professional welders emphasize the importance of matching the wire to the base metal to avoid discrepancies in thermal expansion and contraction, which could lead to weld failures. Consulting with material specialists or experienced welders for recommendations specific to the application can be incredibly beneficial.
An essential factor in the successful use of stainless steel MIG wire is the equipment setup. Ensure that the welding machine is properly calibrated to the wire's specifications, including polarity settings, wire feed speed, and voltage. The wire feed mechanism should operate seamlessly to prevent interruptions in the welding process, which can create defects in the weld bead. Moreover, maintaining consistent pre- and post-cleaning procedures is vital to avoid contamination of the weld area, which could compromise its corrosion resistance.
The environment where welding takes place can also impact the performance of stainless steel MIG wire. While stainless steel inherently resists corrosion, welding in a humid or dusty environment can introduce contaminants to the weld pool. Employing a shield gas, such as argon with a small percentage of carbon dioxide, can help protect the weld from atmospheric interference, ensuring a clean and strong weld.
stainless steel mig wire
Another critical consideration is the skill level of the welder. Stainless steel MIG welding requires a precise technique and a steady hand to produce optimal results. Investing in training or certification programs can significantly enhance a welder's proficiency, leading to improved quality and productivity.
Weld inspection and testing play crucial roles in validating the structural integrity of the finished work. Techniques such as non-destructive testing (NDT) can detect flaws without compromising the weld’s strength. Ultrasonic or radiographic testing can identify subsurface issues that might be missed in a visual inspection. Adhering to industry standards and safety regulations ensures that the welding practices not only meet quality benchmarks but also uphold workplace safety.
Economic considerations also come into play. While stainless steel MIG wire might initially be more expensive than other materials like carbon steel, its longevity and reduced need for maintenance can result in significant cost savings over time. This makes it a financially judicious choice for projects where quality and durability are paramount.
Incorporating stainless steel MIG wire into your welding practice is more than just a technical decision; it is a strategic move that reflects an understanding of material science, engineering principles, and industry demands. As industries continue to evolve and demand higher standards, the role of stainless steel MIG wire in delivering excellence remains paramount.
For industry professionals and businesses devoted to quality craftsmanship, the investment in knowledge and resources surrounding stainless steel MIG wire underscores a commitment to not just meeting, but surpassing, client expectations. This dedication to excellence cultivates trust and establishes authority within the market, reinforcing a reputation for delivering products that stand the test of time and environment.