In the world of metal fabrication, welding electrodes are nothing short of essential tools, driving the success of many projects across various industries. The welding electrode, a core component in arc welding processes, plays a pivotal role in determining the quality and strength of the welds produced. Understanding its significance and the nuances of choosing the right electrode can markedly impact the integrity and durability of the finished product.
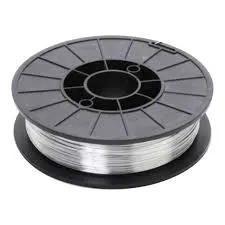
Welding electrodes, commonly referred to as sticks, are integral in forming the electrical circuits needed for welding. During the arc welding process, an electric arc generates intense heat, melting the metal at the welding joint. Here, electrodes serve dual purposes—not only do they maintain the electrical arc, but they also contribute to the weld itself. This involvement necessitates that they be manufactured with care and precision to withstand the demanding thermal and electrical conditions of welding.
The expertise in selecting the appropriate welding electrode cannot be understated. Each project has unique requirements that must be met to ensure optimal outcomes. Factors such as base metal type, welding position, and even the environmental conditions of the workspace should be meticulously assessed.
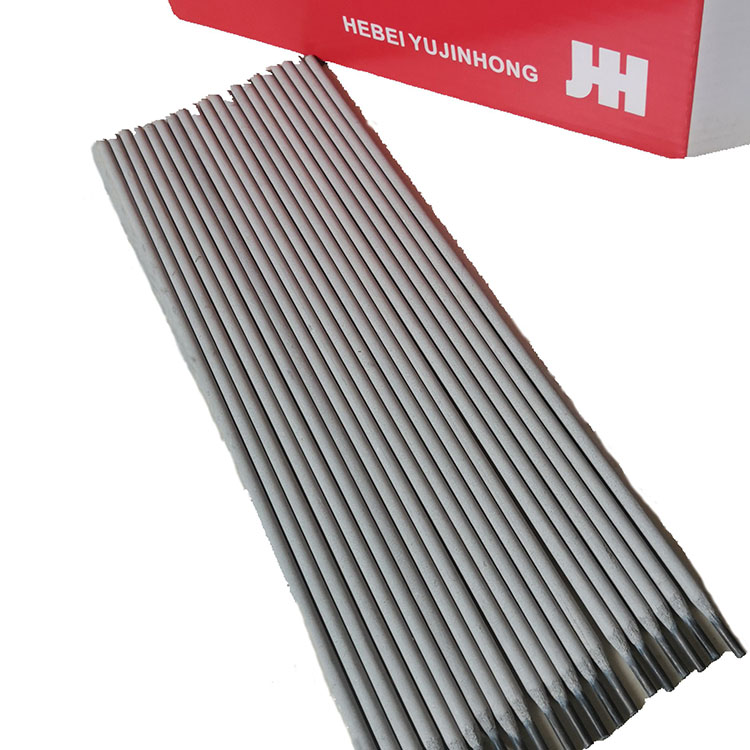
For instance, the choice between consumable and non-consumable electrodes is one that demands expert insight. Consumable electrodes, primarily used in Shielded Metal Arc Welding (SMAW) and Gas Metal Arc Welding (GMAW), become part of the weld, providing filler material. Meanwhile, non-consumable electrodes, typically made from tungsten, are favored in Gas Tungsten Arc Welding (GTAW), where they do not melt and therefore, do not contribute to the weld pool. An accurate choice based on these attributes impacts the weld's mechanical properties and longevity.
welding electrode
From a position of authority,
understanding the coating on electrodes is crucial for any welding project. Coatings are designed not just for protection but to influence arc stability, penetration, and even oxidization rates. For example, the selection of a cellulose-coated electrode could be ideal for vertical down welding, ensuring penetration and speed. Conversely, a rutile coating selection might be beneficial for its easy slag removal and visually appealing welds, reducing cleanup time and post-weld processing costs.
Building trustworthiness among industry leaders hinges on the ability to deliver projects with precision and reliability, and this begins with selecting a reputable electrode brand. Brands that consistently meet international welding standards and garner certifications for quality and safety demonstrate reliability—offering peace of mind to contractors and engineers.
In deploying welding electrodes, real-world experience emphasizes the importance of practicing safety protocols. The handling of electrodes, correct storage to prevent moisture absorption, and disposing of spent electrodes are practical concerns that, when managed appropriately, cement an organization’s commitment to operational safety and environmental stewardship.
In conclusion, the welding electrode stands as a symbol of craftsmanship, with its successful application rooted deeply in expertise and authoritative practices. When organizations leverage authoritative knowledge and trustworthiness in selecting and utilizing these tools, they not only enhance their project outcomes but also solidify their reputation as leaders in the welding industry. This amalgamation of experience, expertise, authority, and trustworthiness sets the foundation for unparalleled success in metal fabrication endeavors.